近年来,随着3D打印技术的不断创新和进步,这一技术也被逐渐应用于建筑行业。3D打印建筑模板相较于传统的建筑模板,如木质模板或钢模板,只需将设计模型输入3D建筑打印机中,转化为打印指令,即能获得特定形状的3D建筑模板。由此可见,3D打印建筑模版在效率提升和可持续发展方面有明显优势。
此次,Polymaker选用旗下的PolyCore™系列粒料产品—— PolyCore™ ABS-5012 作为打印材料。这是一款20% 玻纤增强的 ABS 复合材料,是3D打印低温模具和工装(使用温度不超过80℃)的经济高效之选。利用这款材料作为模具打印,并结合3D打印建筑模版技术的大尺寸和高精度优势,我们浇筑制作完成了苏州聚复科技股份有限公司的品牌墙(长5m * 宽0.4m * 总高2m)。
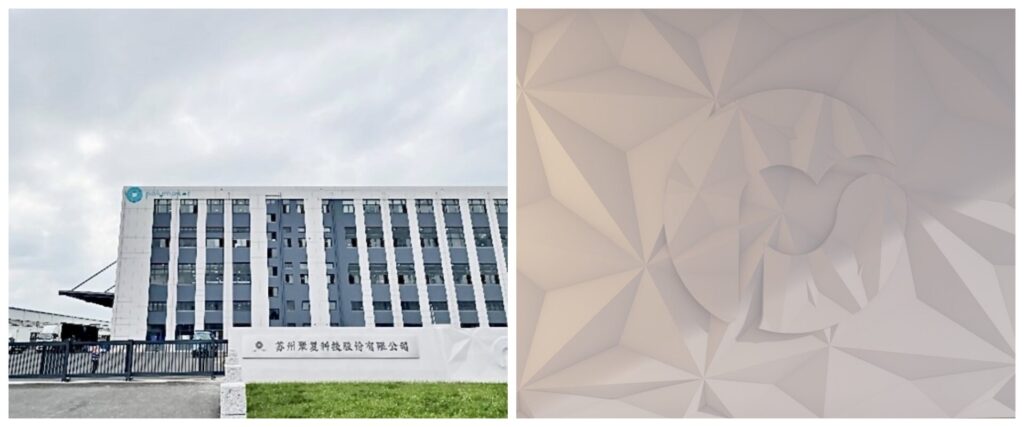
接下来,我们将按一步步揭秘如何用PolyCore™ ABS-5012打造建筑墙体。
首先,建筑设计师突破传统模具的设计局限,从飘飘雪花中汲取设计灵感,并打造成凹凸立体的造型。这一造型自带光线折射效果,从设计上将3D打印技术和创意想象付诸实践。
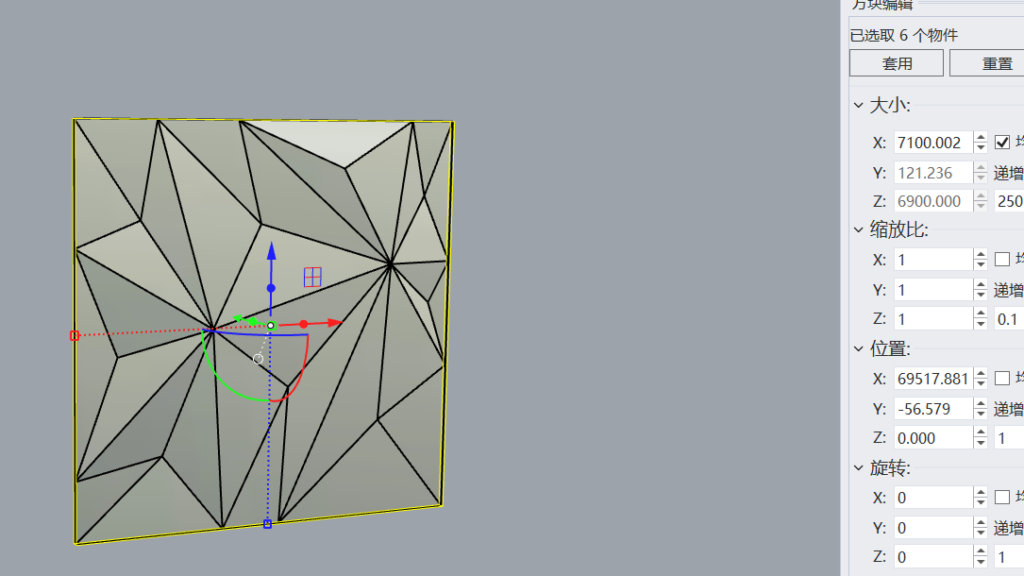
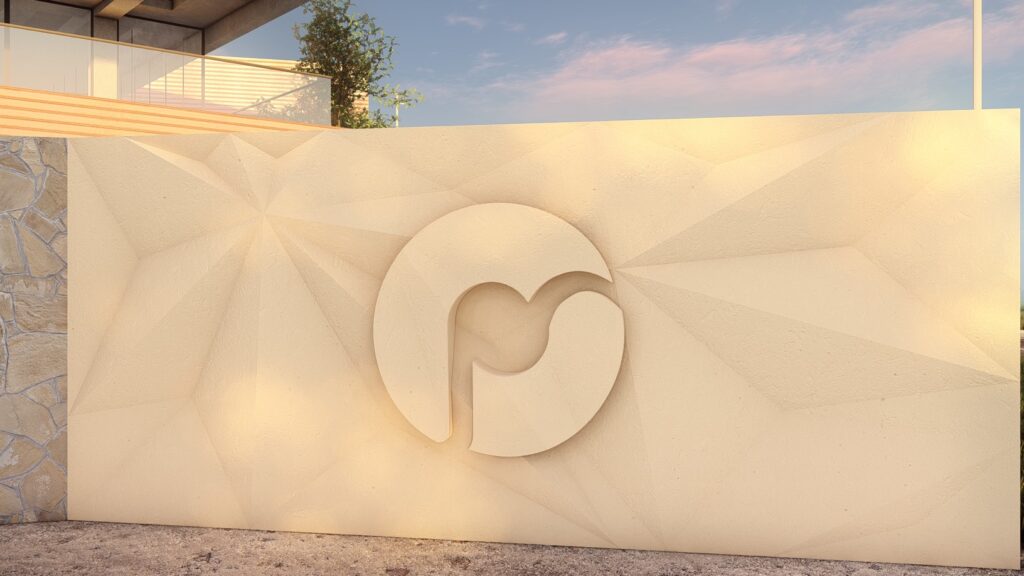
其次,进入到对设计模版打印和处理的阶段。全套模版打印下来,总计耗时16小时。完成模版打印后,我们将最终的这一大尺寸模板切分成四个部分,继续进行初期打磨和模板内表面的两次腻子批涂,以消除层纹,确保混凝土浇筑件的表面美观平滑。
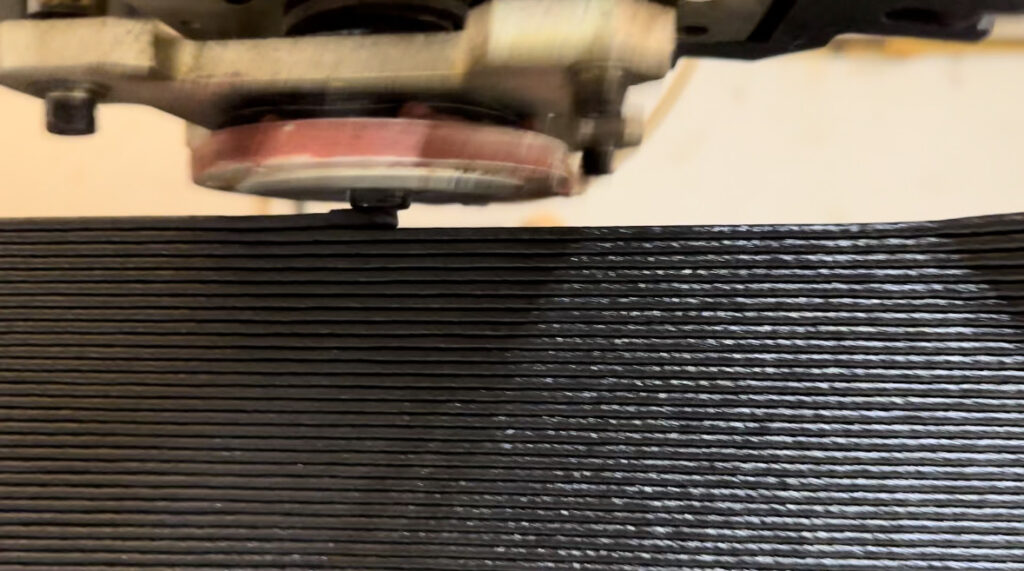
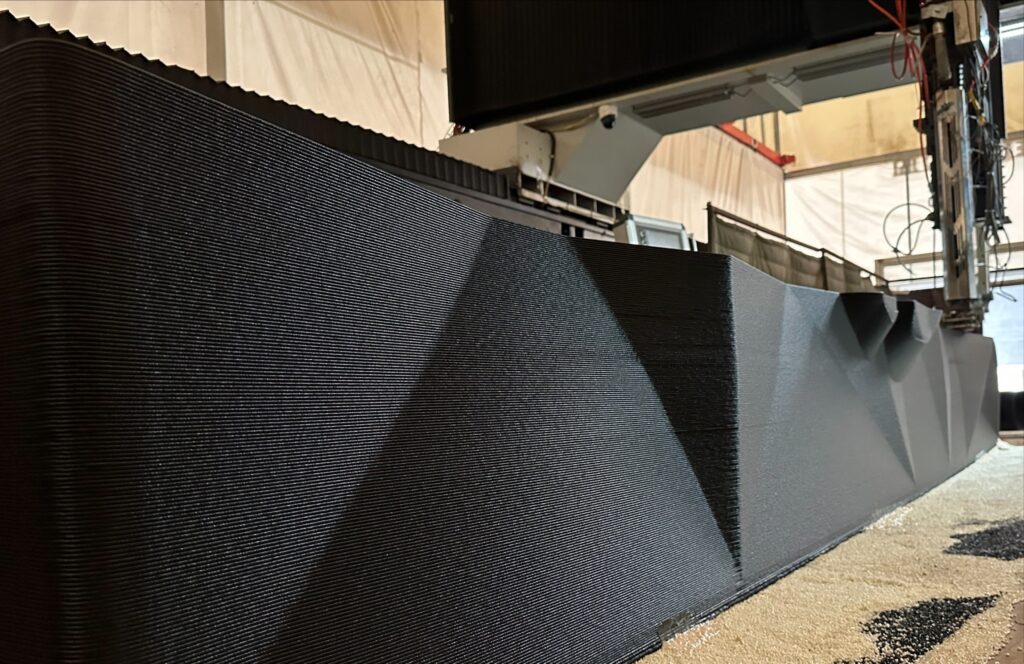
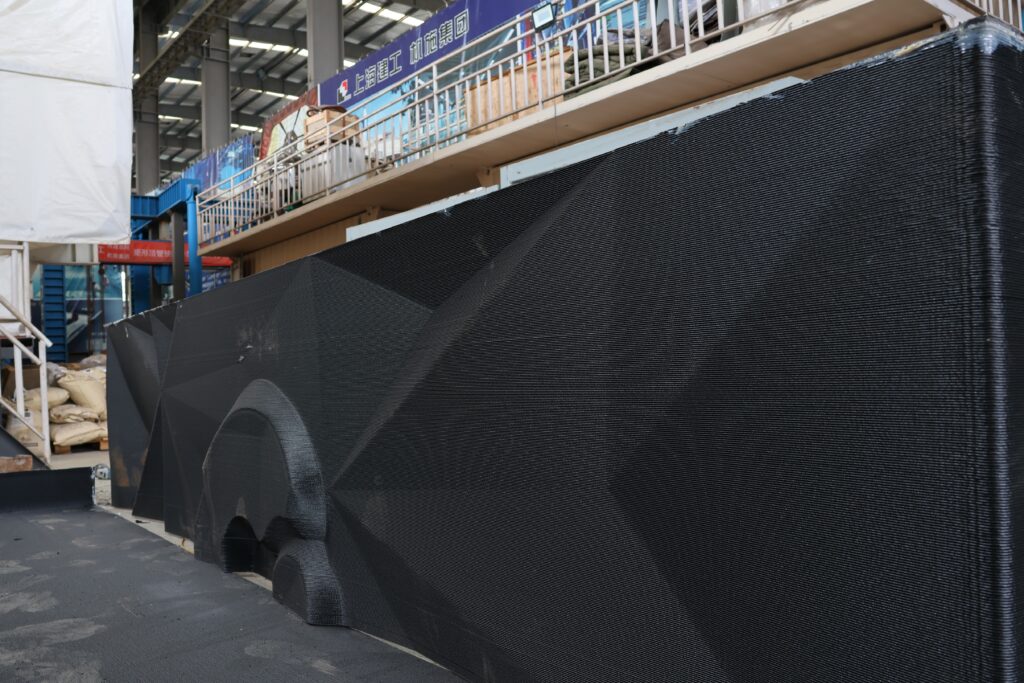
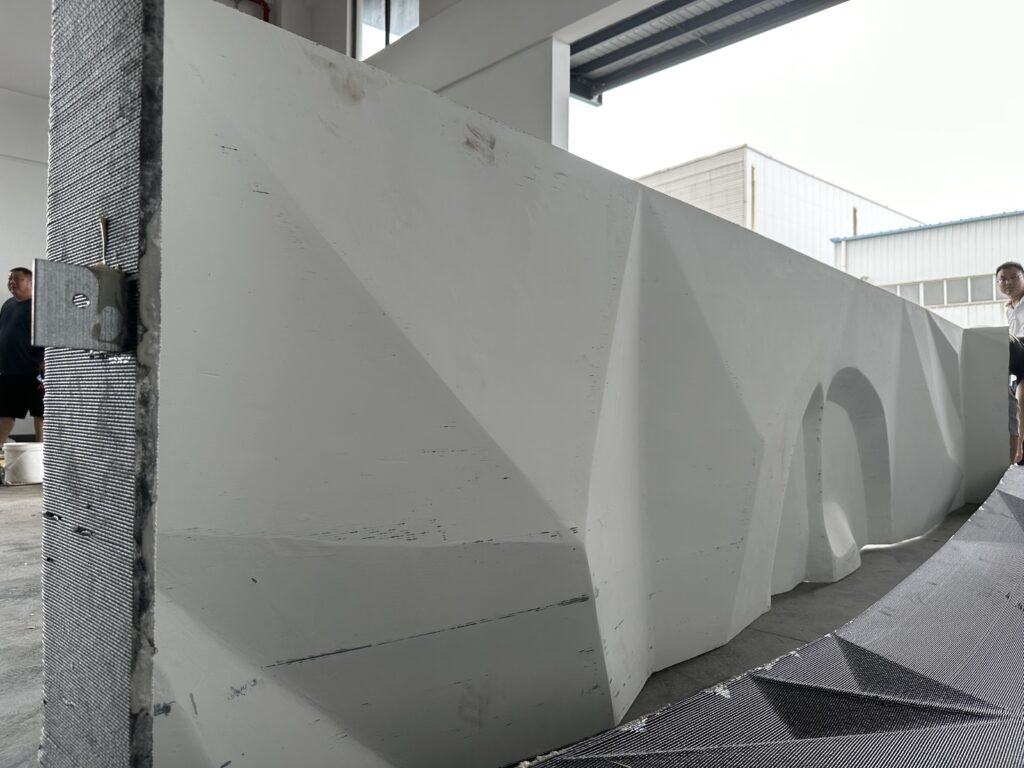
接着,使用角钢和螺栓等进行模版拼接,并在外部搭建支撑结构,确保混凝土浇筑过程的稳固。

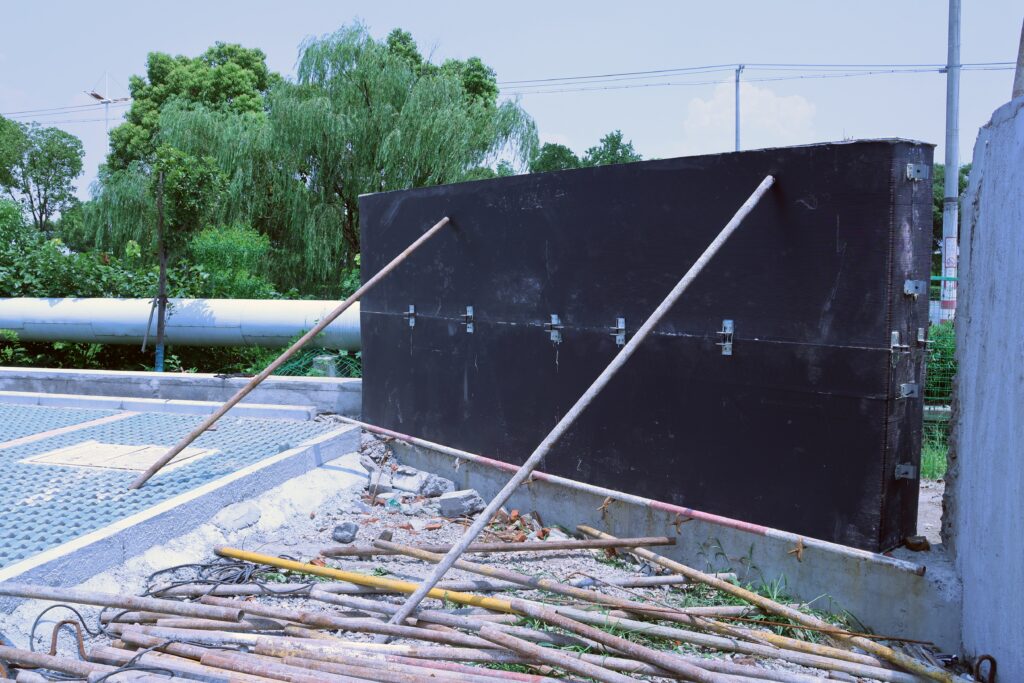
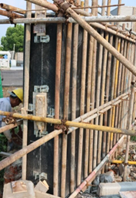
最后,正式进入到混凝土浇筑和脱模阶段。这一阶段需要在3D打印建筑模板内部先搭建钢筋网片结构,随后浇筑C30混凝土,待风干后再进行脱模与上色。
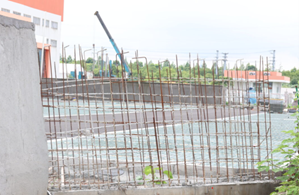
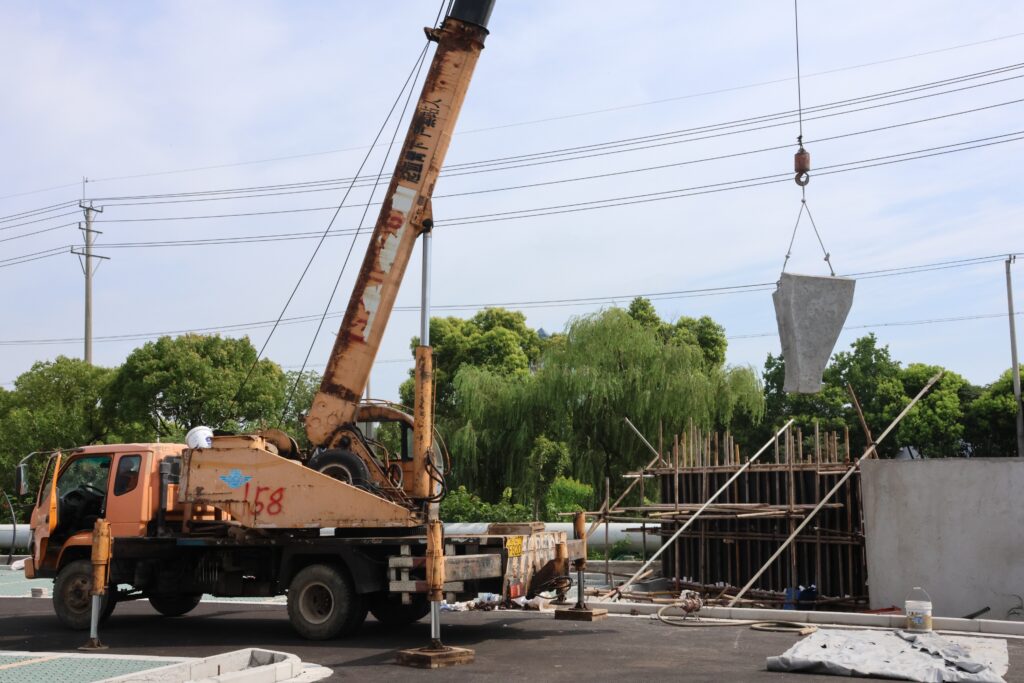
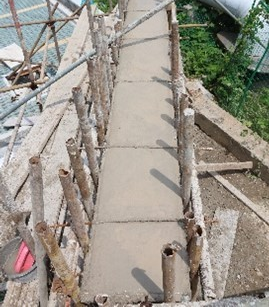
最终呈现出这一Polymaker logo在雪花中熠熠生辉的品牌墙。这一品牌墙也在2024年荣获TCT亚洲展最佳应用奖之最佳工业案例。
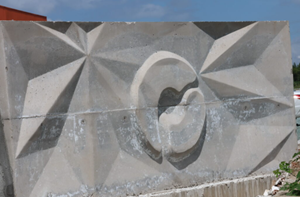

Polymaker通过在建筑材料领域的创新研发和持续改进,不断提高其材料,尤其是粒料在该领域的使用稳定性和耐用,助力3D打印技术在建筑领域实现更高水平的设计自由度、缩短交付周期、直接降低生产成本并减少制造过程中的碳足迹。
相信在不久的未来,3D打印建筑将成为建筑业发展的重要动力之一,通过这一全新的增材制造方式为城市带来更多美妙的设计与惊喜,让创新无处不在。
2024年5月6日,上海—— 近日,Polymaker凭借其PolyCore™系列产品在3D打印建筑模版领域的优秀表现,荣获了TCT亚洲展最佳应用奖之最佳工业案例。这一荣誉不仅是对Polymaker在创新和卓越方面的认可,也是对其在3D打印行业中持续领导地位的肯定。

随着3D打印技术的不断创新和进步,这一技术被逐渐应用于建筑行业。此次获奖案例正是Polymaker在建筑领域的深耕之作:利用3D打印的高精度和大尺寸优势,Polymaker选用旗下PolyCore™系列材料,浇筑制作完成了Polymaker(及苏州聚复科技股份有限公司)长达5米,宽0.4米,总高2米的品牌墙。墙体从飘落的雪花中汲取设计灵感,打造凹凸立体的造型;上海建工集团下属上海市机械施工集团有限公司为更好铸造这一项目,还与上海酷鹰科技有限公司联合研发出一体化打印装备,并将其充分应用于品牌墙的打印工作之中 ,彰显了3D打印将创意想象付诸实践的实力,为建筑行业注入了智能制造的新活力。
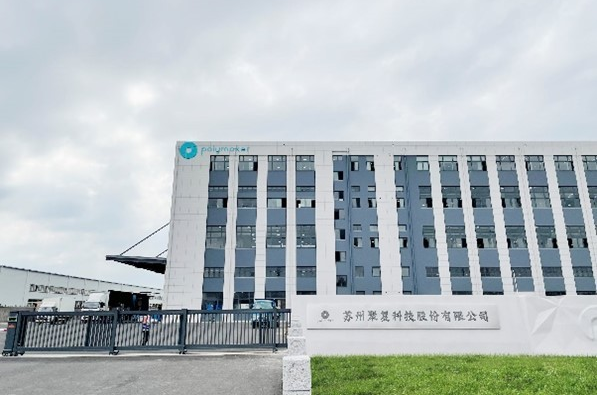
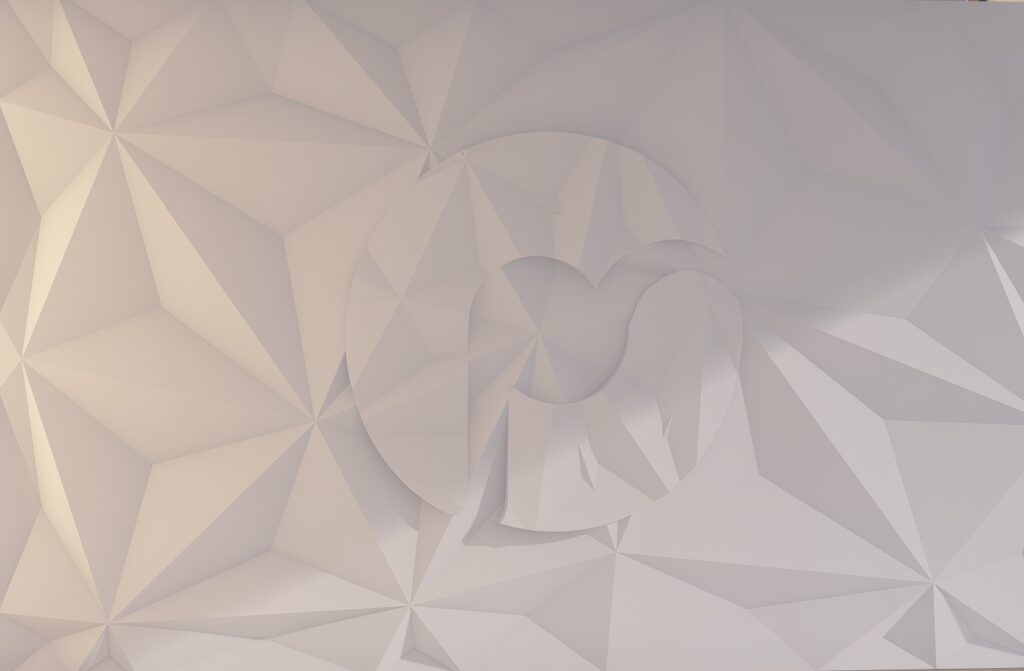
这一墙体的建成意义重大。上海市机械施工集团有限公司方面表示:“超大幅面异形混凝土模板3D打印技术的应用,依托“十三五”及“十四五”国家项目课题研究成果,将为市政及建筑工程中异形混凝土模板模具的快速、高精度制造带来革命性的变化。与传统模具相比,这一技术有效降低了制造成本与施工周期,推动了传统建筑向数字化、工业化、智能化、低碳化的转型。”正因如此,Polymaker才能在亚洲地区最具影响力的增材制造盛会TCT亚洲展上脱颖而出,赢得最佳应用奖之最佳工业案例奖项。关于此案例的更多详细信息,请点击“PolyCore™ 打印建筑模板应用案例,让建筑焕发智能制造之美”。
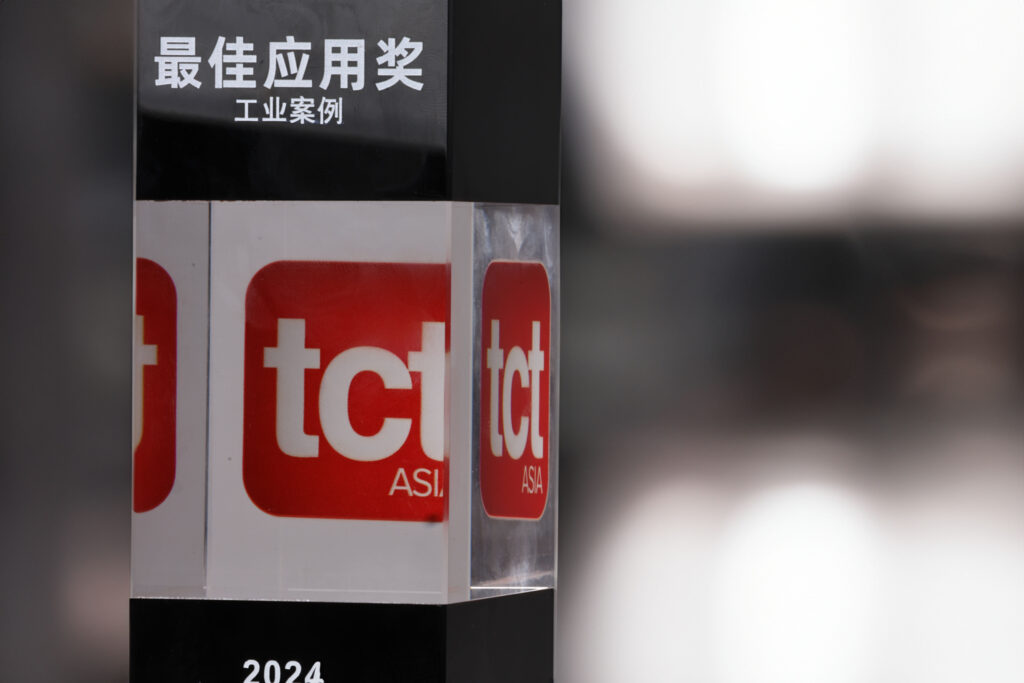
“我们对荣获TCT亚洲展最佳工业案例奖感到非常荣幸。这不仅是对我们团队不懈努力和持续创新的肯定,也为建筑行业的发展带来新启示。Polymaker一直是将3D打印应用于建筑领域的先行者,为包括室内设计和室外建筑在内的建筑行业提供多款粒料产品,并成功打造上海桃浦公园景观桥、成都流云桥、拉卡环岛雕塑等项目。未来,品牌还将继续致力于技术创新和产品优化,为建筑行业带来更多智能制造的可能性,让建筑焕发智能制造之美。”Polymaker CEO罗小帆博士如是说道。
除最佳工业案例奖外,Polymaker还在TCT亚洲展十周年之际获得了"十年老友"称号。这一荣誉代表了Polymaker与TCT亚洲展的长期合作和密切关系,以及品牌在3D打印行业中的持续贡献。
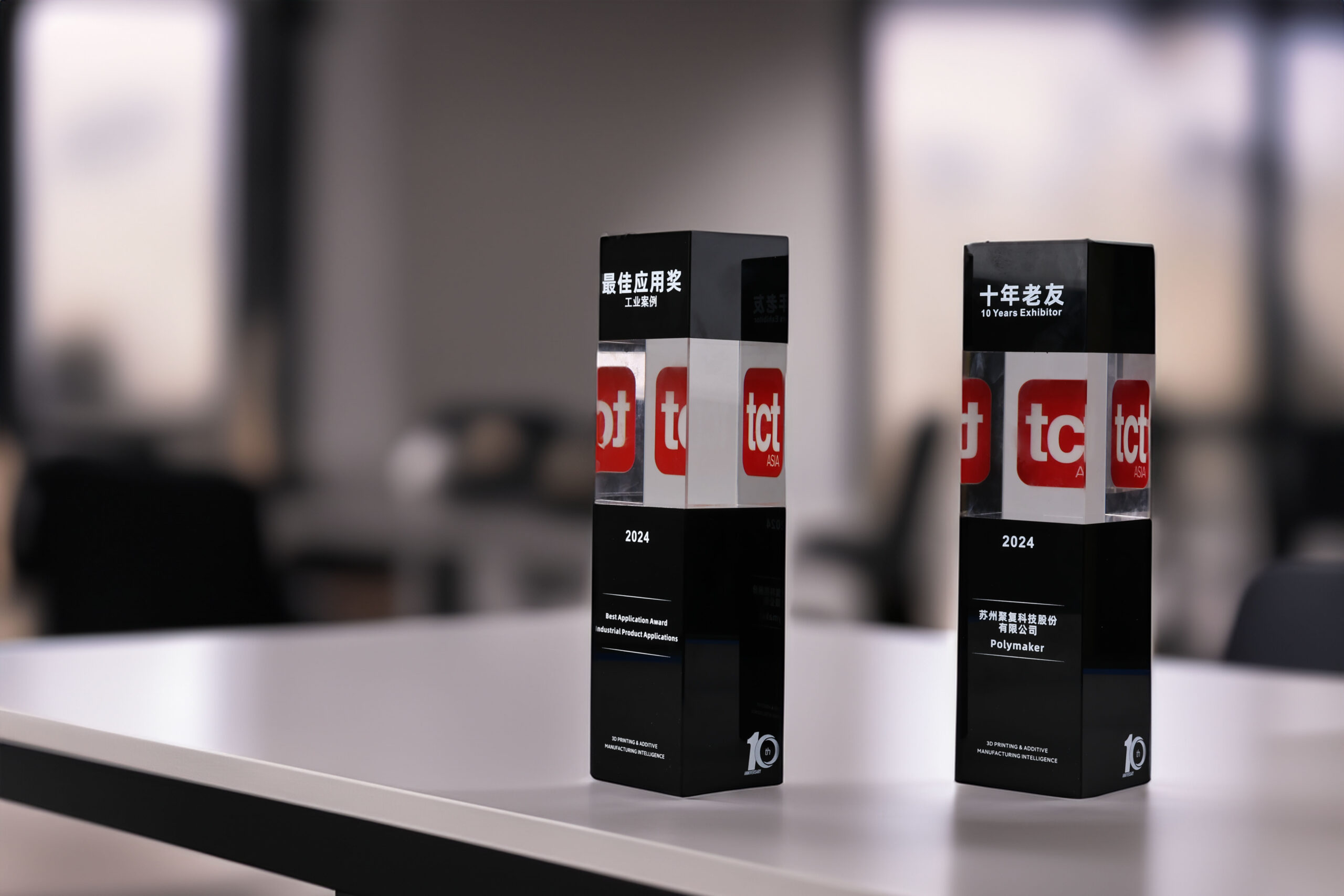
未来,Polymaker将继续秉承卓越品质和创新精神,不断拓展增材制造领域的边界,为客户和合作伙伴提供卓越的解决方案,最终推动增材制造技术的发展。
随着工业级3D打印技术开始逐步挑战机械加工、注塑成型和其他传统制造工艺,增材制造也从原型制作渐渐扩展到更重要的终端产品应用上。
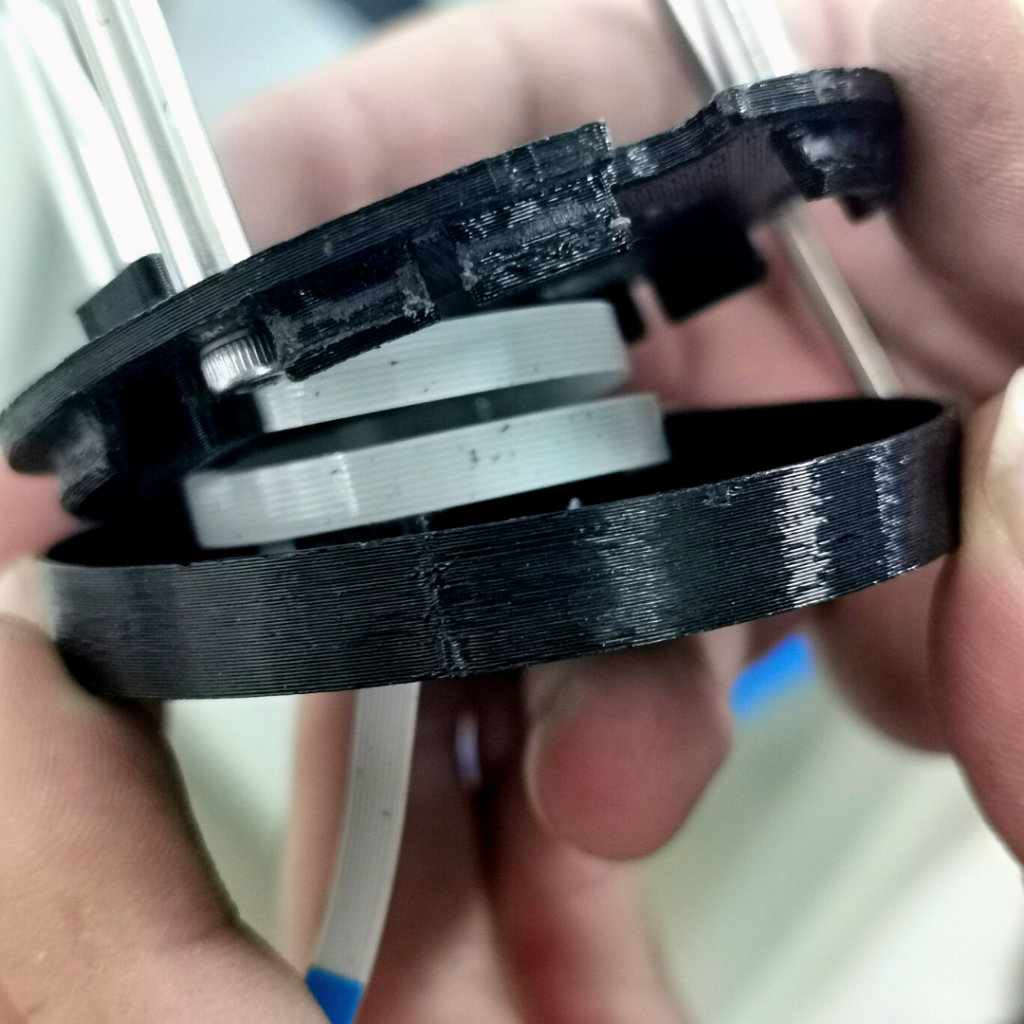
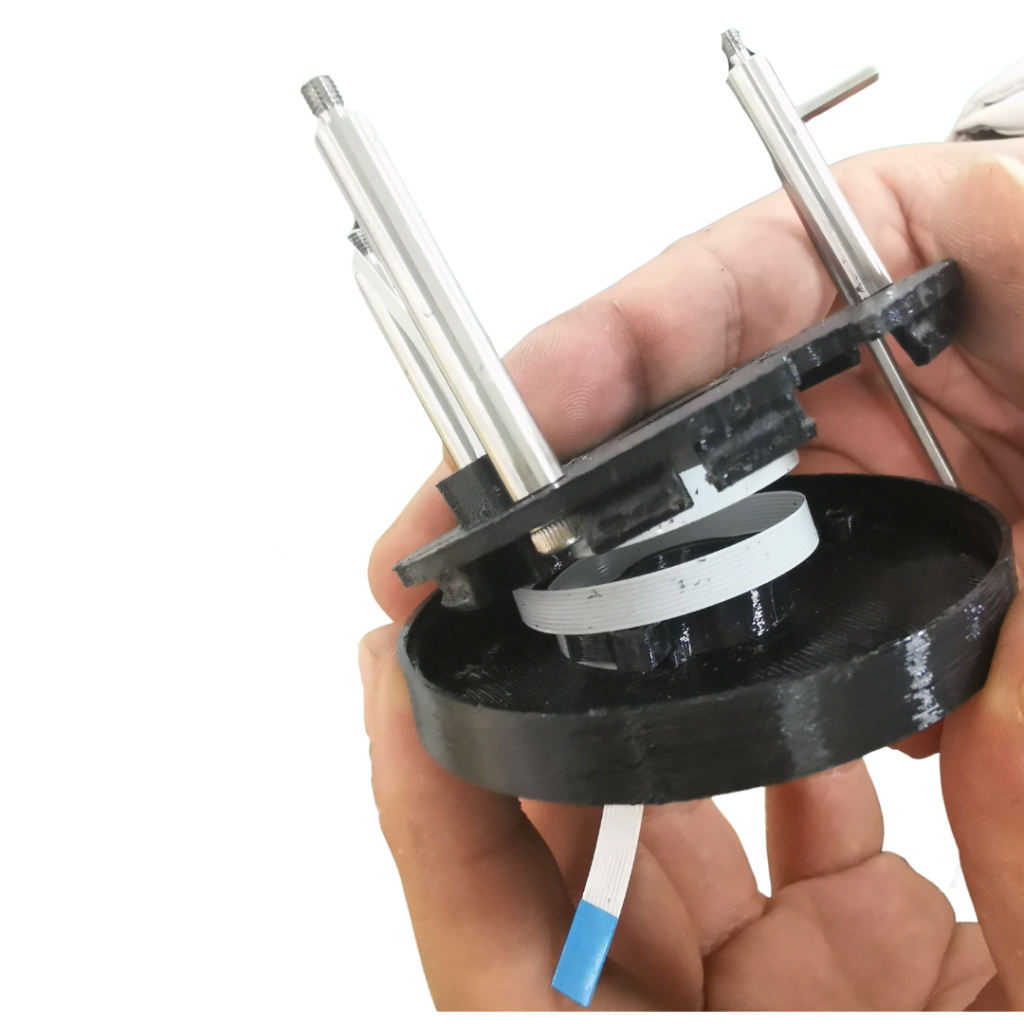
前段时间,一家提供高精度直驱电机的运动控制公司正为研发设备中的FFC(Flexible Flat Cable)软排线设计合适的连接器。FFC软排线是一种经常使用在电子装置中的连接线结构,该公司需要将FFC软排线放置在定制的连接器中,用以连接旋转电机以及光电开关装置。
设计初始,该公司向专门进行铝加工的供应商询价,答复却让他们不得不另寻他法:
- MOQ限制:单件最少起订量为50个
- 加工工艺限制:部分卡槽设计较为特殊,传统工艺无法加工
- 交期不稳定:两周交期,且不能确保运输时间
与铝加工相比,3D打印技术不仅生产速度更快,还可实现零件重量更轻。并且3D打印能在同一时间生产不同规格零件,更经济高效地实现定制化需求。最终,公司决定与Amesos mfg和Polymaker合作生产FFC软排线的连接器。
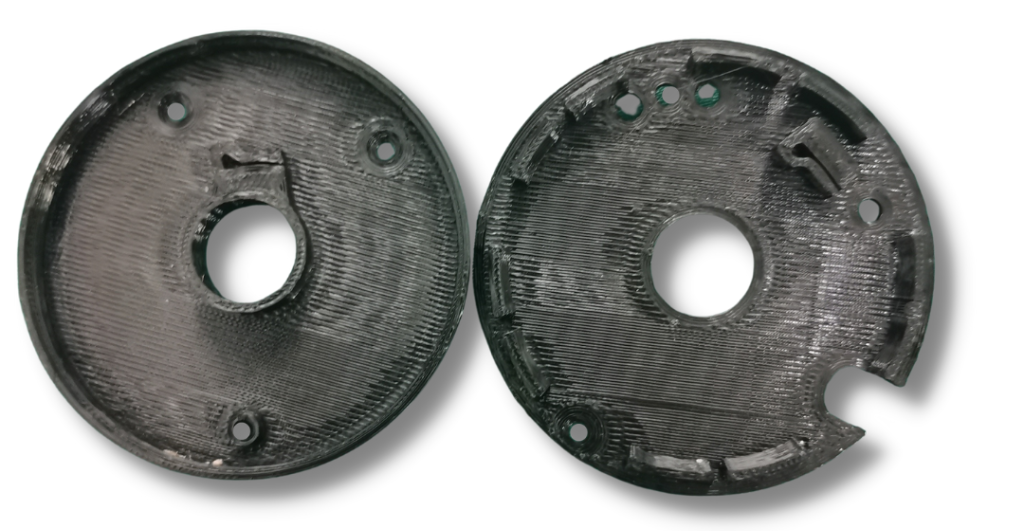
本次合作中,定制的连接器内部设计有多个孔位以及卡槽,用以后期组装以及限位的作用。该连接器设计上下两个部分,组装后的连接器可以将FFC软排线缠绕安置在部件内部,线的两端分别连接旋转电机与其他电气元器件。
旋转电机会带动FFC软排线不断转动,而连接器能够实现上下分离转动。并且设计了限位卡槽,防止FFC软排线缠绕以及断裂。零件在当天打印完成后,客户即可立刻进行试装。
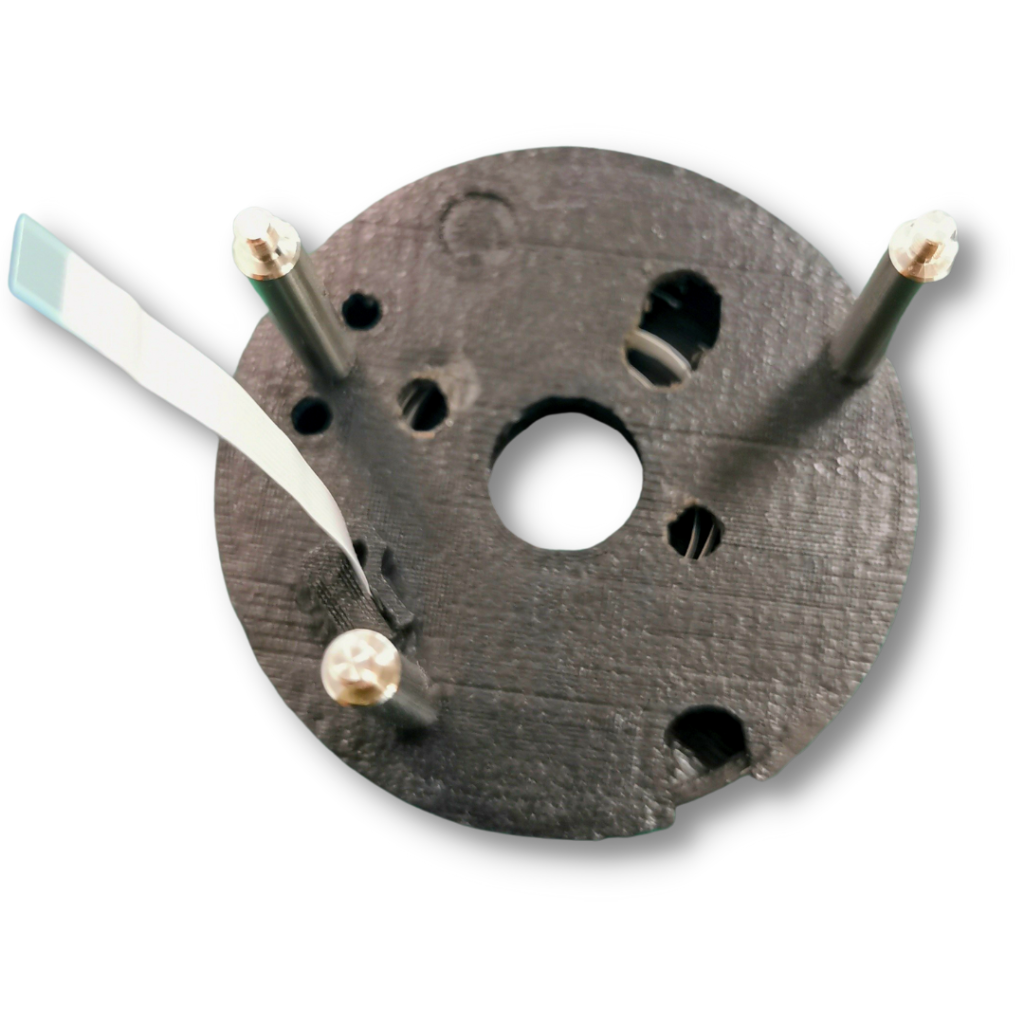
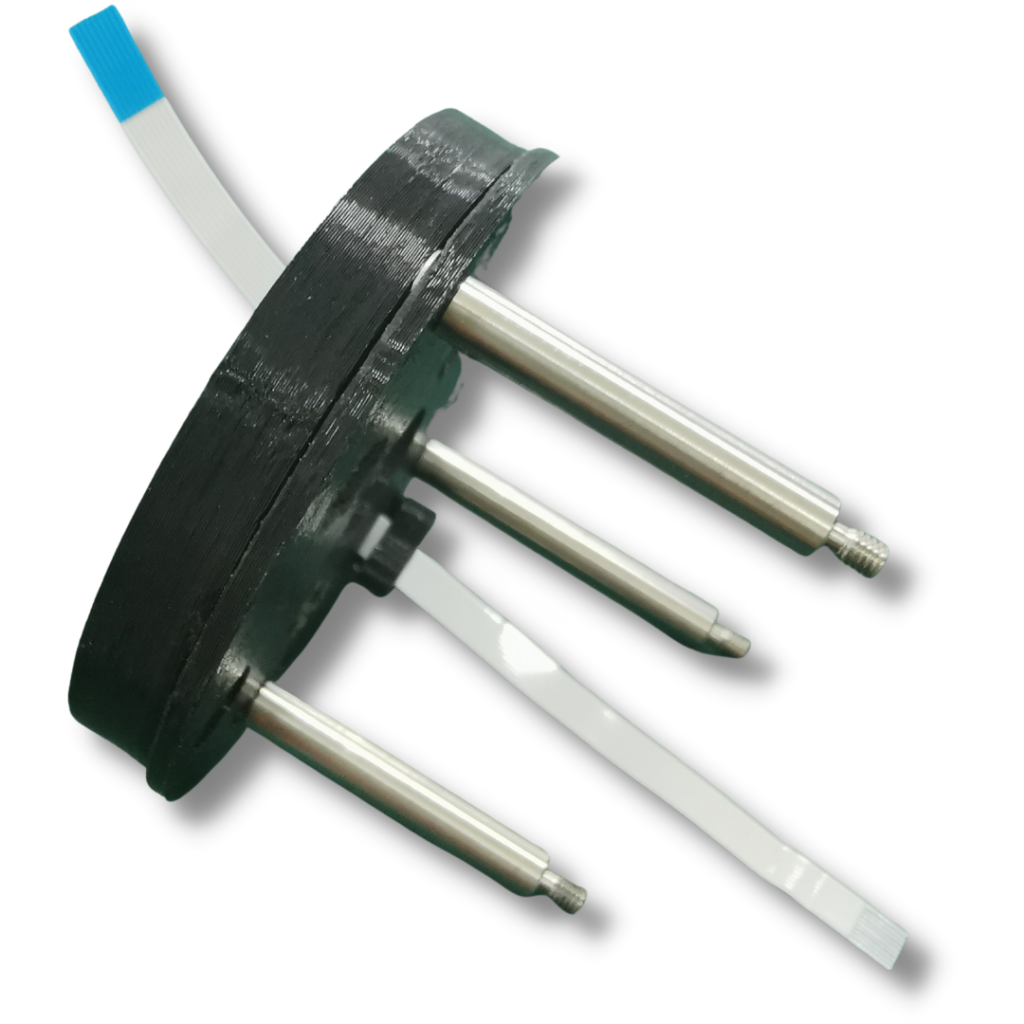
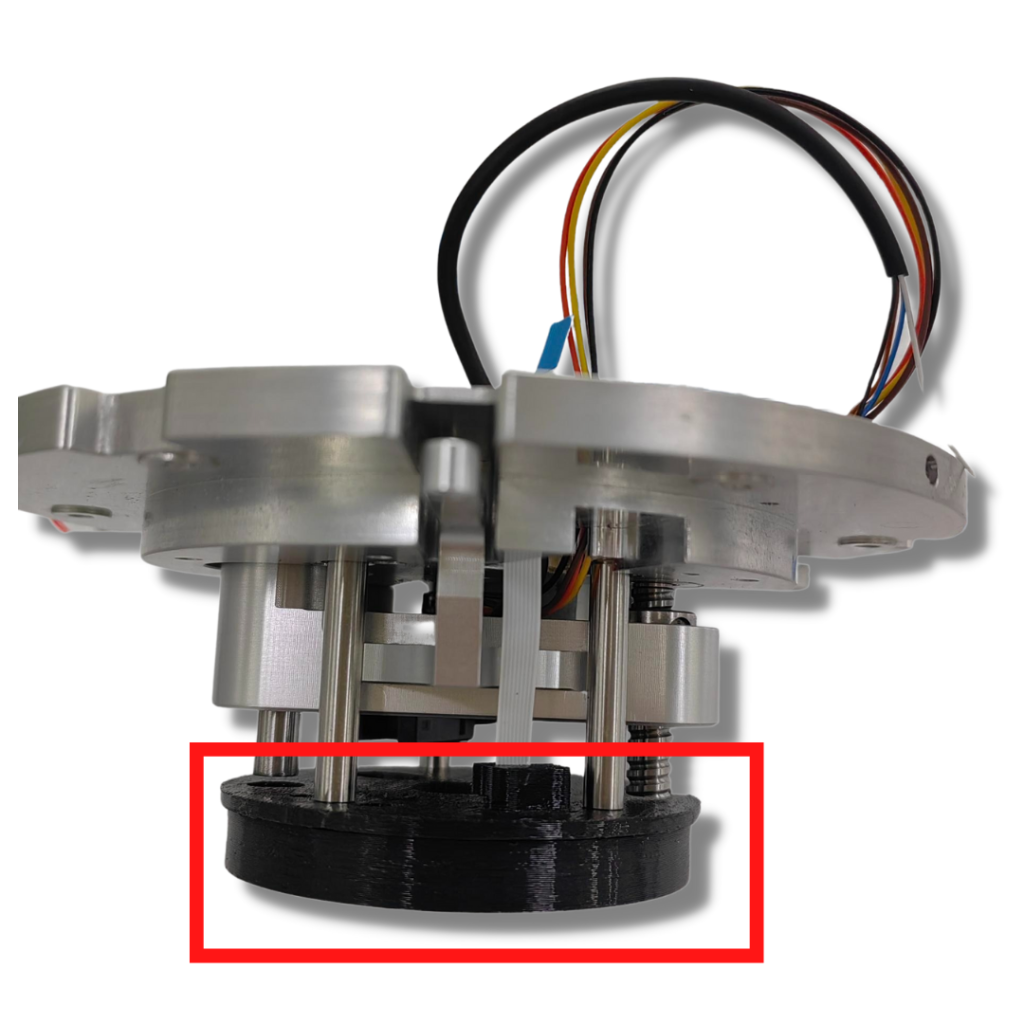
考虑到FFC软排线会随着旋转电机不断地在连接其中转动摩擦,所以连接器的材料选择必须要耐磨并兼顾保护作用。且电子元器件的工作环境需要具备ESD安全的特性,Polymaker旗下的PolyMax™ PETG ESD成为此次零件生产材料的不二之选。
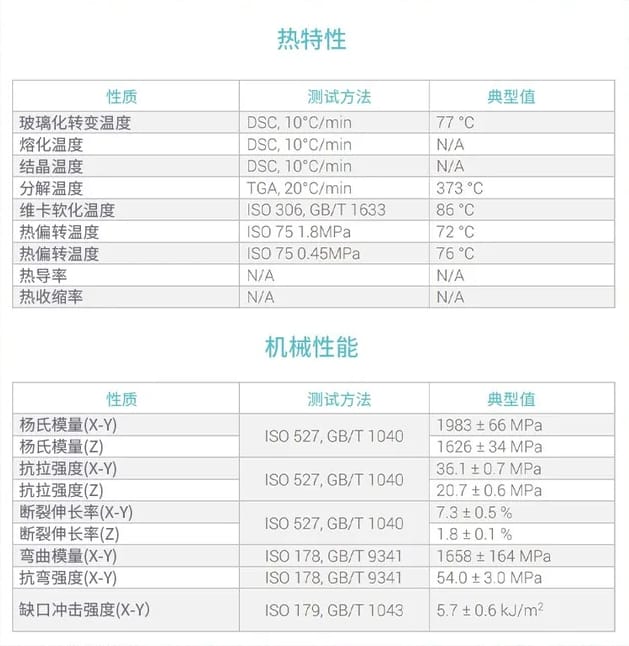
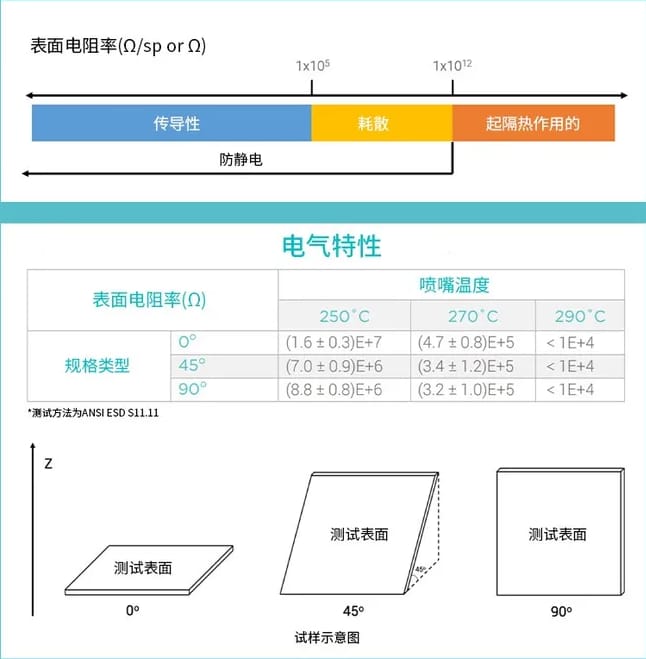
PolyMax™ PETG ESD不仅有着优于PLA的高强度、耐冲击性和耐温性,且易于打印。它ESD safe的特性也可广泛应用于电子行业的工装夹具、功能原型设计、电器外壳制造。
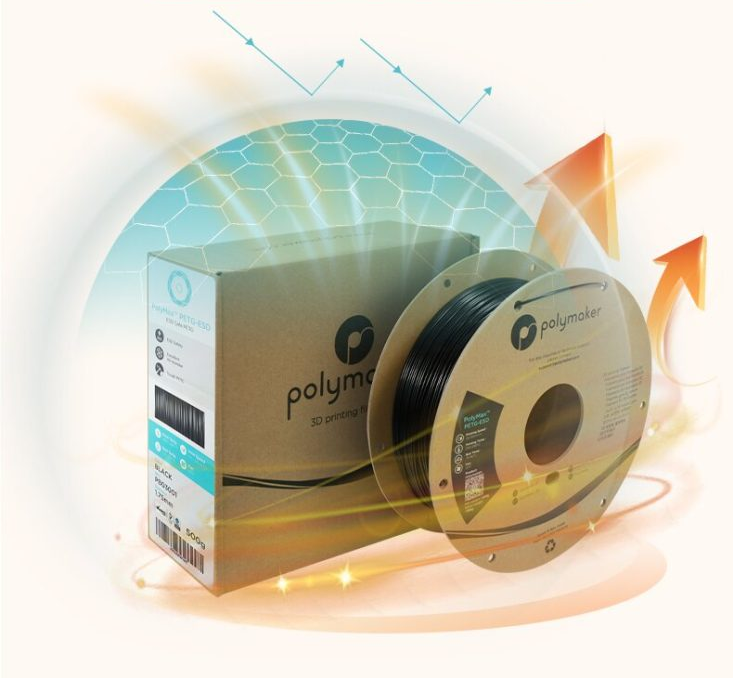
通过Polymaker和Amesos的合作,这一定制生产的FFC软排线连接器,将原本铝加工所需的成本降低了85%,且3天内就完成了打印件的交付与试装。这意味着增材制造:
- 可以进行小批量定制化生产,缩短数月的生产交期并大幅降低间接成本。
- 能够打破传统流程的设计限制,使得定制零件和复杂设计可以以更经济高效的方式生产。
- 帮助客户更快速的响应市场需求,而无需过多的设备成本与昂贵的工具变更投资,使运营多样化。
- 能够数字化生产,克服供应链中断,消除不必要的库存。
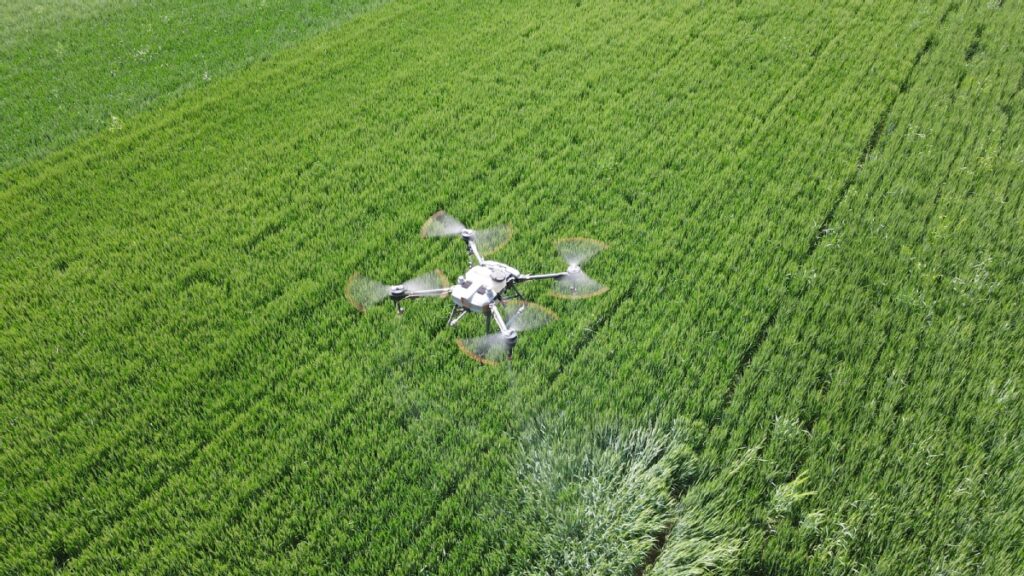
随着机械化程度越来越高,植保无人机已开始应用于农业作业,如用其进行大面积农作物喷药等。
市面上的植保无人机款式较多,主要分为四部分:一是飞控系统,二是动力系统,三是喷洒系统,四是机型机架。喷洒系统是3D打印技术在这一领域的主要应用模块,包括药箱、水泵、喷头和相关传感器。
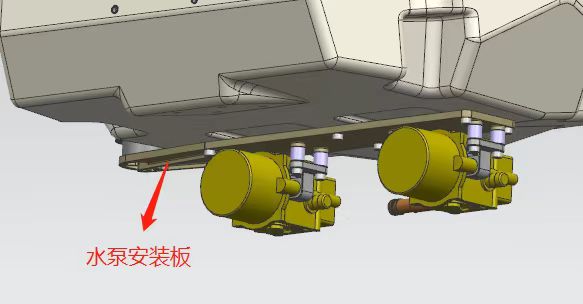
植保无人机安装有存储药液的药箱,作业时药液通过水泵抽排而出。然而抽排时,水泵的振动会影响飞行器的飞行控制系统。传统方式采用CNC铝板加工等办法以固定水泵。但缺点不可避免:工序复杂、耐腐蚀性较差、设计自由度低、无轻量化优势等。这些都或多或少会影响无人机的生产效率、搭载能力和续航能力。
而通过3D打印技术,就可以快速制作原型验证,有效解决以上问题,并进行小批量生产。斟酌之下,生产商决定与Amesos和Polymaker合作,共同打造增材制造解决方案。
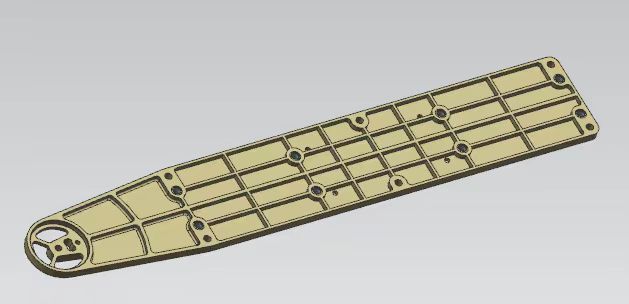
水泵安装板设有不同大小的定位安装孔,螺丝依次穿过这些安装孔及装配孔后,才能与螺母螺接固定水泵。
Amesos主要负责定制设计匹配植保无人机型号的水泵安装板以满足客户需求。3天内4个不同版本,最终遴选出合适方案提供给客户并成功通过安装测试。接下来就是打印交付了。安装板上的单个水泵重量在400g,客户需要安装2-3个水泵。所以这一打印件需要能避震、不易断裂的材料。
Polymaker则负责材料方面的挑选工作。作为一家专注于 3D 打印材料的高新技术企业,Polymaker从接到客户需求之始,就开始在旗下性能各异的产品中进行试验比对,最终遴选出PolyMide™ PA612-CF材料。
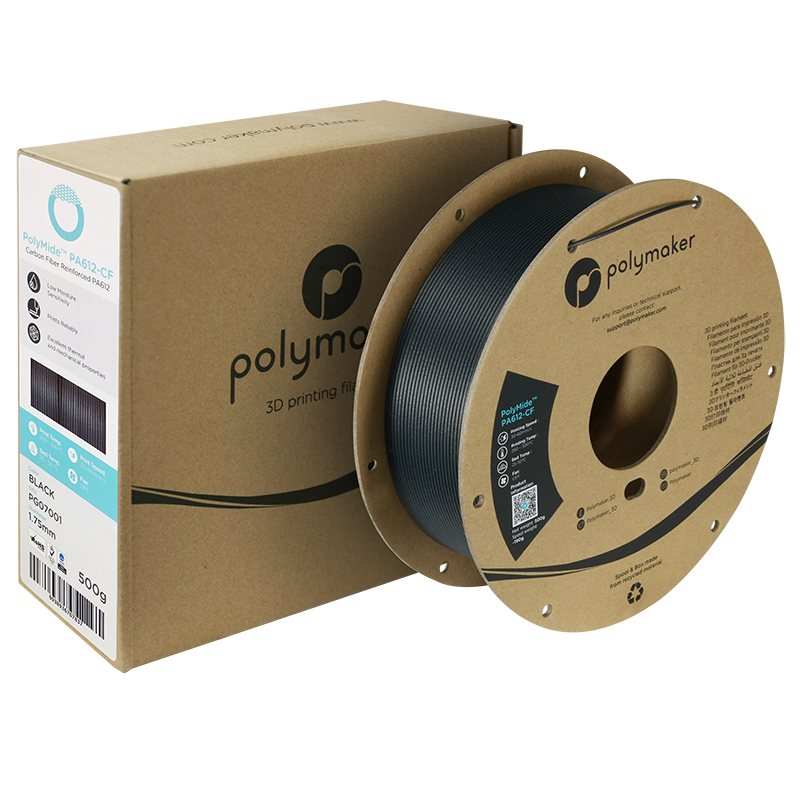
PolyMide™ PA612-CF 是一款碳纤增强的长链共聚尼龙材料,得益于其长链的化学结构,该材料对于水分的敏感性相比于尼龙6/66以及尼龙6基的材料有明显的减低,同时具有比一般的尼龙12类材料更高的力学性能。高刚度、高韧性和耐高温等优点,让由PolyMide™ PA612-CF打印的成品不易受到振动影响,可以保证水泵安装板具有足够的强度和稳定性。同时,材料较低的吸水性使其可以在潮湿环境中使用,符合这一需求的特定应用环境。此外,凭借碳纤增强和Warp-Free™技术,使用PolyMide™ PA612-CF 打印出来的产品具有极高的尺寸稳定性,有效延长了水泵安装板的使用寿命。
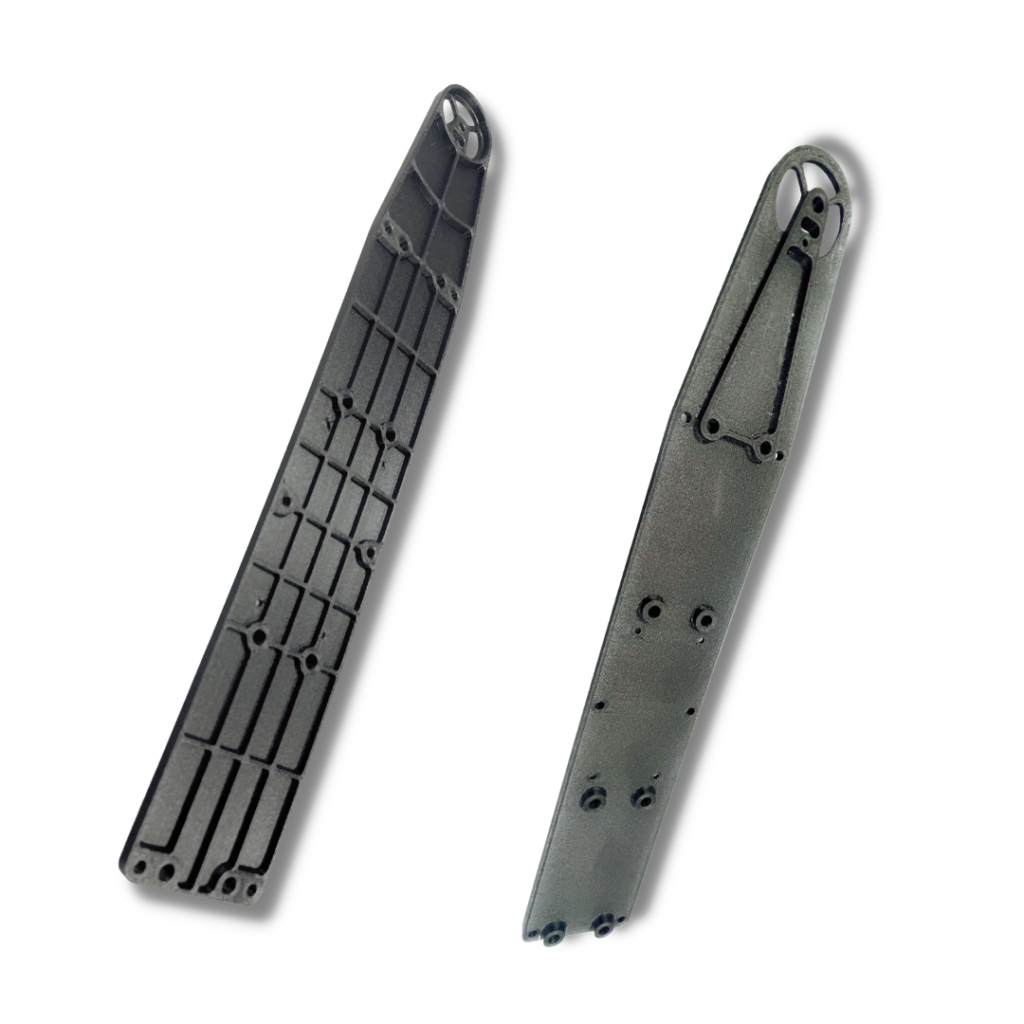
通过采用3D打印技术进行水泵安装板的设计和生产,充分展现了3D打印技术的快速、灵活和低成本等优势。制造商能够快速制作原型、进行验证和必要的改进、并立即进行批量生产和交付。这一过程有效地缩短产品研发周期,实现复杂的几何形状和内部结构的制造,按需打印高效率生产,极大提高了生产制造的经济效益。
增材制造技术是目前一项快速发展的制造技术,它以数字化的方式为产品的设计和制造带来了更多的灵活性和更高的效率,有效弥补了车削、磨削、锻造、冲压和铸造等传统加工工序里的不足。正因如此,市场对于3D打印技术的期待也在不断攀升。
在摩托艇制造行业,3D打印可以带来个性化、提高竞争力的优势显而易见。Polymaker也加紧了在这一领域的深入合作。美国某知名摩托艇制造公司刚好在优化调整生产模式,想借助Amesos和Polymaker的合力寻求定制化的增材制造解决方案。调研方案的工程师经过反复比对,最终认准了PolyLite™ PETG作为打印材料。
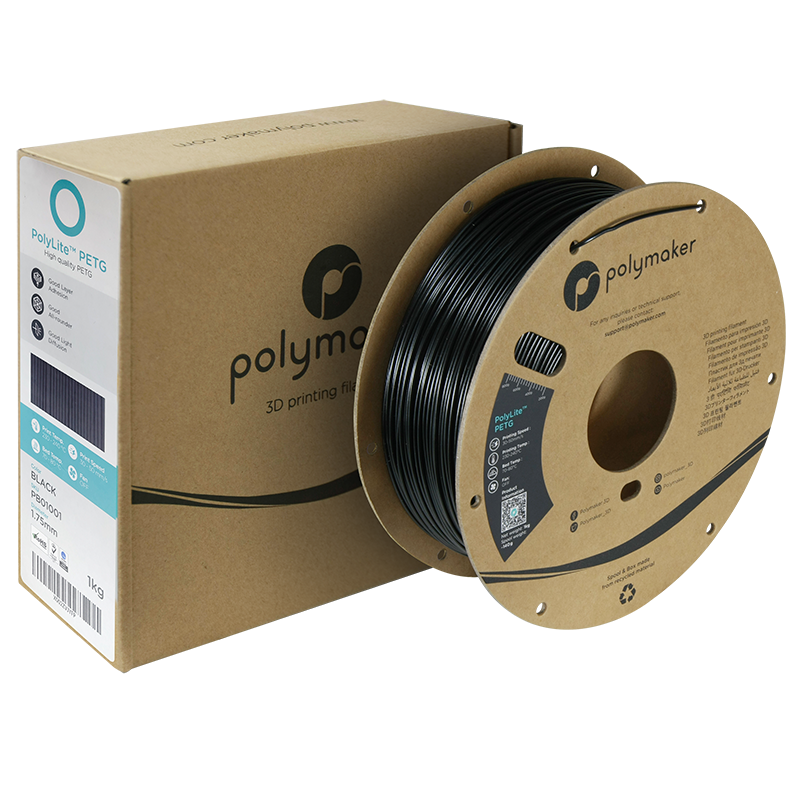
相对于PLA类的材料,PETG的热软化温度更高,综合力学性能更好;相对于ABS类的材料,PETG的尺寸稳定性更好。综合而言,PolyLite™ PETG更具成本效益且不易翘曲,优异的抗冲击强度和耐水、耐化学腐蚀的特质更让其成为打印摩托车覆盖件再好不过的材料。打印完成这样一套覆盖件的打印总重量约为15KG,包含了摩托艇的座舱盖以及前保险杠。
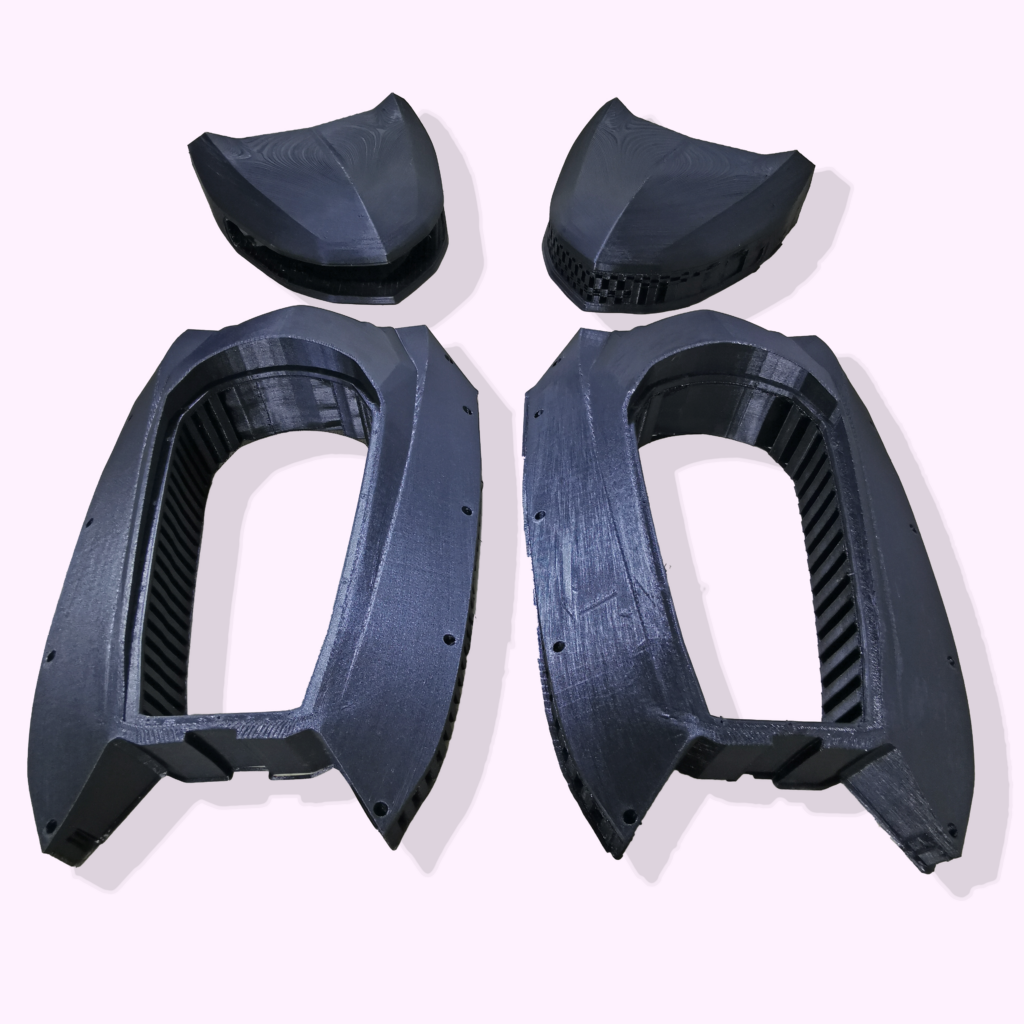
在使用PolyLite™ PETG打印的过程中,除了合适喷头温度、底板温度及回抽等设置,冷却风扇的控制技巧也是影响打印结果的关键因素。由于PETG的结晶特性,若冷却风扇开的过大,打印件的层间结合力则会急剧降低,使打印件在Z方向上易断裂,无法长久使用。若完全关闭冷却风扇,又会降低表面光滑度且支撑难以剥离。选择合适的风扇速度,成为这个应用的一大难点。经历数次工艺测试后,基于摩托艇部件的结构,工程师使用了20%的风扇速度,才最终达到了表面质量和层间结合力的良好平衡。
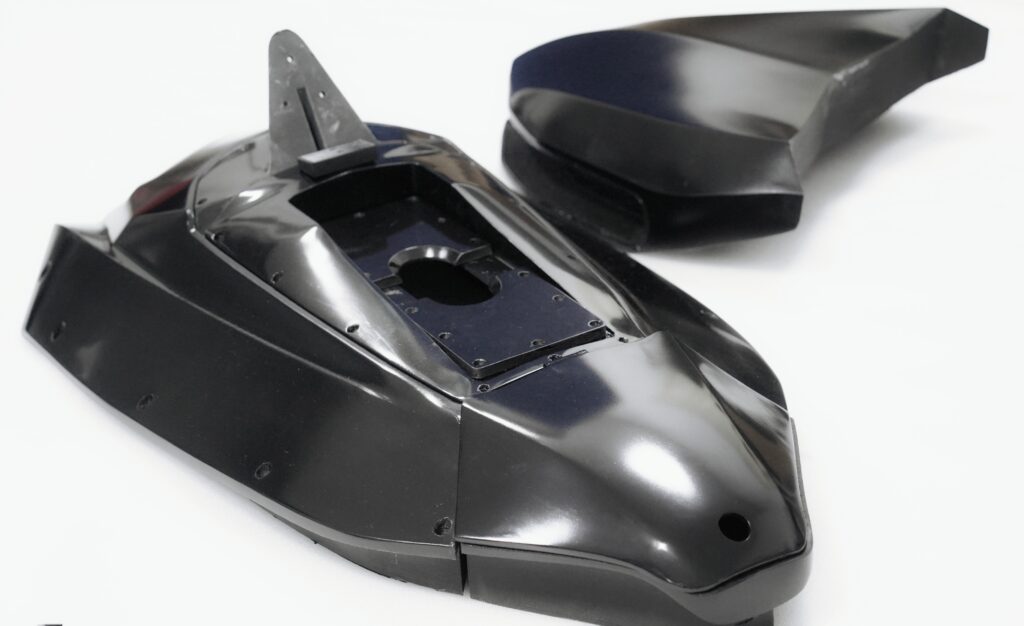
由于PolyLite™ PETG的优势性能,以及Amesos提供的稳定精准的打印机,最终完成了摩托艇的座舱盖以及前保险杠的的工程设计,并将其成功用于小批量的连续生产,打印效率更是超过了163cm3/hr (200g/hr)。这既是Polymaker在摩托艇制造行业的一大重要应用成果,更代表着3D打印技术在推动创新和实验方面带来的更多的可能性、更大的自由度和更高的灵活性。
导读:
金属铸造工艺,是工业文明建设的重要组成部分。铸造业发展,与汽车、石化、钢铁、电力、造船、装备制造等国民经济支柱型行业息息相关。
传统熔模铸造(失蜡浇铸法)工序繁琐,耗时较长。3D打印零件精密度、复杂结构成型度高,在金属铸造领域呈现新兴态势,渐渐成为制造业金属铸造的理想选择方案,应用广泛。
说起金属熔模铸造,这一名词似乎总与大规模工业生产相关。铸造炉高耸林立,赤红而滚烫的金属液缓缓灌入熔模中,铸造成品逐渐成型。事实上,金属铸造不仅仅局限于大型工厂制造生产,只要拥有合适的生产设备和生产条件,在家也可以亲身感受金属铸造的魅力。
本期,Polymaker 跟随Bilibili UP主共赴金属铸造家庭化体验之旅,探索铸造历程。这个夏天,与Polymaker一起点燃你的铸造梦想!
铸造材料选择 - Polymaker Specialty产品系列-PolyCast™
PolyCast™, 是Polymaker独家研制的一款熔模铸造材料,以代替传统蜡模使用。PolyCast™ 问世以来,以其独特低灰分(Ash-Free™)技术受到工业级市场认可,该材料采用层纹消除技术(Layer-Free™),打印品可抛光处理,模型表面光洁度高,可实现理想的金属铸件表面效果。
作为一款工业级材料,PolyCast™ 将 3D打印产品快速设计迭代的优势与金属铸造相结合,适用于各类金属原型制作、一次性浇铸等金属模型,器具制造应用。
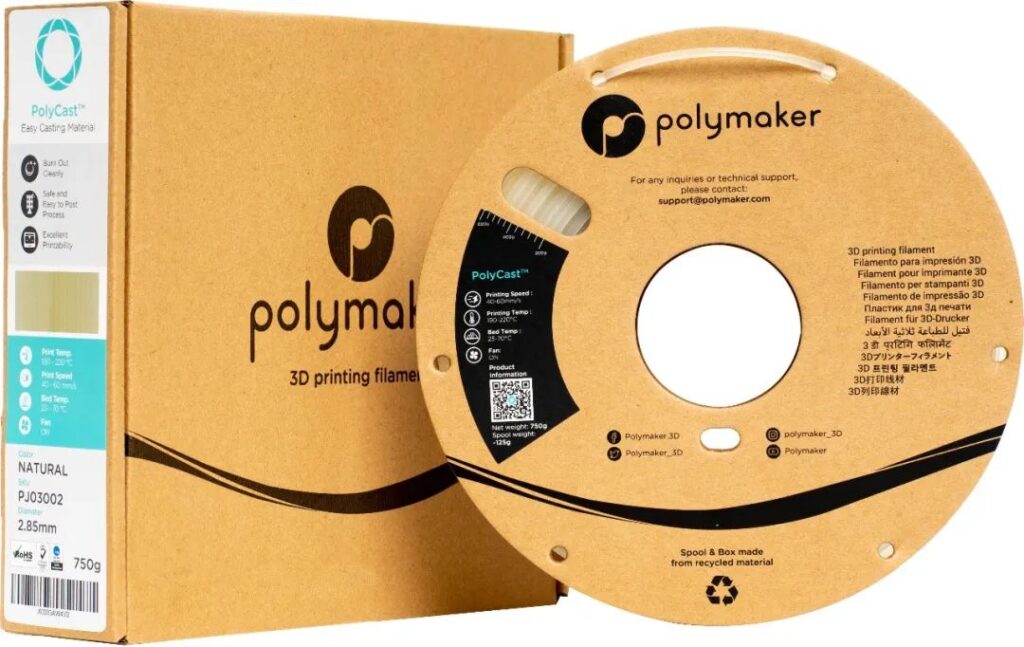
铸造讲师 - 桑旭
桑旭,Bilibili Up主-未匠,包装开发工程师。业余爱好3D打印设计,拥有个人独立工作室,常使用青铜、黄铜铸造喜爱的工艺作品,作品种类多元丰富,质感独特。不定期在Bilibili上进行3D打印和铸造视频分享。

他表示:“相较于传统意义上的生产方式,PolyCast™带给我全新的创作视角。它简化了普通失蜡铸造工艺的设计修模工序,方便使用者将自身创意与设计紧密结合。3D打印产品成型精度高,可合理缩短制造时间,运用3D打印及铸造的形式可创造出更具质感的金属作品,应用于青铜、黄铜、贵金属模具制造中。这也证实了3D打印工艺与金属铸造结合的无限潜能。
PolyCast™ 打印便利,打印件无翘边收缩等缺陷,易于脱蜡烧制,焙烧后几乎无灰烬残留。从外观来看,铜虎模型表面光洁度极佳,节约后处理时间,这实属不可多得地铸造用3D线材。我期待未来将其运用在结构更加复杂的设计模型中。”
3D打印&金属铸造体验之旅
2022,农历壬寅虎年。桑旭决定以“虎”为主题创造一款金属铸件吉祥物,以增添新年喜庆元素。他以黄铜为基础铸造材料,运用雕刻绘画软件Zbrush 3D建模绘制吉祥物形态,桌面级3D打印机、PolySher™ 抛光机、脱蜡焙烧炉等相关装备制造铸品。
第一步:模型设计——“虎虎生威”3D设计图,神态庄重威严
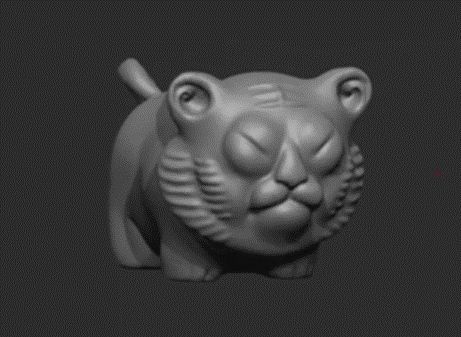
第二步:PolyCast™ 打印参数设定。参数设定中,打印温度、速度十分重要 。桑旭设定190°C打印温度,适当调快打印速度,满足高灵敏全金属喷头打印机温度要求,打印流畅高效。
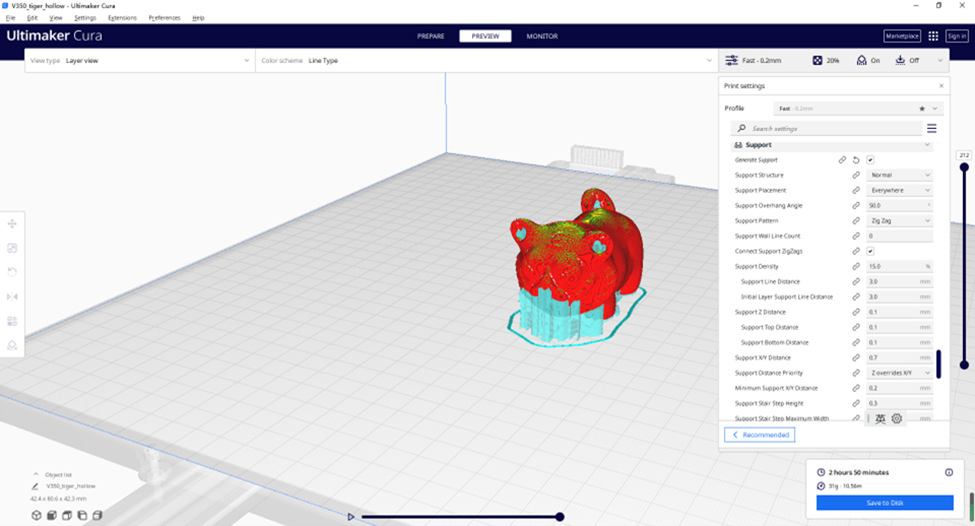
第三步:砂纸抛平去除支撑。
第四步:使用Polymaker后处理设备PolySher™抛光。PolySher™专为PolySmooth™ 、PolyCast™ 3D打印件后处理工艺研制,采用层纹消除技术,酒精雾化后均匀喷洒覆盖打印模型,消除打印层纹,模型表面平滑光洁。
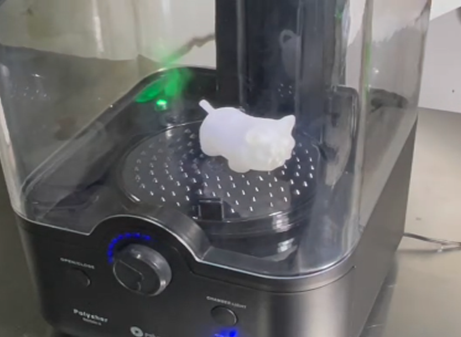
第五步:种蜡树。依一定顺序,用焊蜡器将制好蜡模沿圆周方向依次分层地焊接在一根蜡棒上。(提示:需选好注道进入口位置,方便铸造成品去除多余流道。注意排气分支通道分布合理,避免缺料或砂眼等缺陷。)
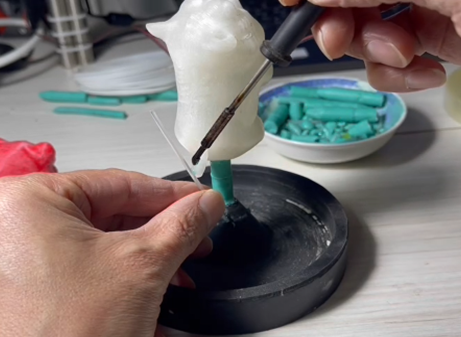
第六步:制石膏模,抽真空。石膏粉加水混合,搅拌均匀,抽真空,脱气泡,缓倒入蜡树钢盅内。钢盅加满石膏后再次抽真空脱气泡。静置直至石膏完全固化。
第七步:脱蜡处理,PolyCast™ 打印模型焙烧。脱蜡炉预热,钢盅杯缘多余型壳材料除净,放入脱蜡炉。推荐焙烧温度为500℃,焙烧2h。脱蜡焙烧中,石膏内PolyCast™打印模型经高温(焙烧温度> 600°C)影响彻底蒸发,残留灰分量仅为 0.003%,焙烧后模壳内部表面基本无残留物,可保证浇注金属液体在流道内通畅流动。
第八步:加热熔化黄铜。
第九步:将金属液浇注入与零件形状适应铸型中,直至冷却凝固。
第十步:焙烧钢盅入水,高温石膏遇冷炸裂,溶解为泥浆状液体,取出铸造半成品。
第十一步:后处理。除去多余部件,打磨抛光。
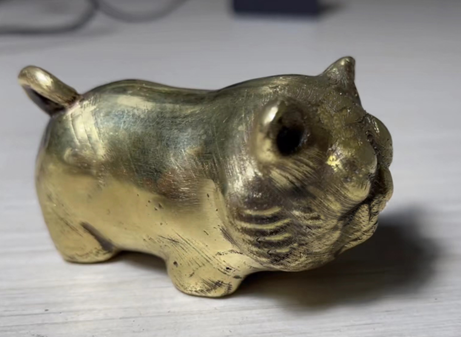
桑旭提示,与大型工业模式下的金属铸造方式不同,家庭式工作室受场地及生产器械限制,需注意事项如下:
- 线材密封:避免线材吸湿生潮,彻底干燥线材,防止打印拉丝。
- 用电安全:脱蜡炉和熔金炉设备功率较大,且铸造时同时使用,使用期间应反复检查线路情况,确保电路正常运转,消除火灾隐患。可常备2只灭火器应对紧急状况。
- 人身安全防护:铸造时规范佩戴安全眼镜,3M防尘口罩,使用耐高温手套,穿着防护安全鞋。
- 空气流通:3D打印及PolySher™抛光使用,金属铸造阶段全程开放通风,避免铸造者吸入散逸尘雾。
金属铸造的家庭化发展,是铸造业发展的未来方向。桑旭期盼更多3D打印实践者关注选择这一创意性的铸造模式,为实际生活应用服务。他认为,3D打印技术发展将与金属铸造工艺结合,广泛应用于工业级、家用级、个体化定制等各项领域,适应国计民生社会应用需要。
TCT Awards,是一年一度的TCT 3Sixty展会奖项颁奖典礼,用于表彰参与增材制造行业的杰出设计师、工程师以及技术提供商。2022年TCT Awards已于6月8日晚在伯明翰成功举办,200多名行业人士齐聚一堂,见证今年增材制造领域的杰出贡献者和团队的诞生。
Polymaker荣获2022年度TCT Award创新应用奖
Polymaker荣获2022年度TCT Award创新应用奖。创意应用奖决赛评选十分激烈,其中Stratasys、BMW、Shapeways、Ricoh 3D 和 Gravity Industries 等行业领先公司参与角逐,许多优秀的项目入围评选。
这辆卡丁车的美学设计灵感来自于1985年发布的乐高积木,车身所有的部件都是桌面3D打印设备和Polymaker的材料制作而成,额外装配了电机,刹车和电子装置后,这辆3D打印卡丁车就可以开上卡丁车赛道了!
Part.1 回顾
Polymaker与海外3D打印爱好者、电子软件工程师马特·丹顿合力打造了3D乐高卡丁车。卡丁车在评奖前已引起参展人群广泛关注,巨型卡丁车色彩鲜艳,极富科技感与创意性,颇受评委团好评,载誉而归。
Part.2 卡丁车
3D乐高卡丁车,是基于3D打印技术的全新创意项目,其灵感来源于乐高科技#1972套件系列。新版卡丁车采用电气化设计方案, 赋予组件模型以生命力,将玩具模型改造为纯电动式可乘骑的巨型乐高卡丁车,设计感与实用性兼备,极具观赏价值,也可满足玩家群体个体化定制要求。
因卡丁车不同模块间功能性质各异,设计者采用Polymaker全线产品参与打印设计。PolyMax™ 系列材料配方经纳米增强技术优化改善后,机械性能优越,适用于多类零部件打印应用所需。PolyMax™PLA韧性优异,机械强度高,用于底盘部件承重,稳定性高;PolyMax™ PETG综合性能强,耐热耐用,可适应齿轮运行时摩擦生热环境要求,是工程应用的理想之选;PolyMax™ PC具备出色的强度与韧性,用于车轴架构;柔性材料PolyFlex™ TPU95弹性优异,可随模型设计变化产生不同弹性效果,打印轮胎耐磨易用;PolyLite™ PLA 色彩品类丰富,在大量装饰部件上得以广泛应用,色调变化柔和,创意十足。
多种材料组合,展现了Polymaker 不同线材间独特的性能优势,马特独到的设计理念与良材相得益彰,为卡丁车顺利诞生奠定基础。
“这是一个优秀的实践项目。我通过3D打印的形式将乐高卡丁车模块设计优化重组,使其成为真正可驾驶运行的代步工具。这款卡丁车融合了我的童年梦想,也给很多人带来欢乐,是一次不错的3D创意体验。”
----马特·丹顿
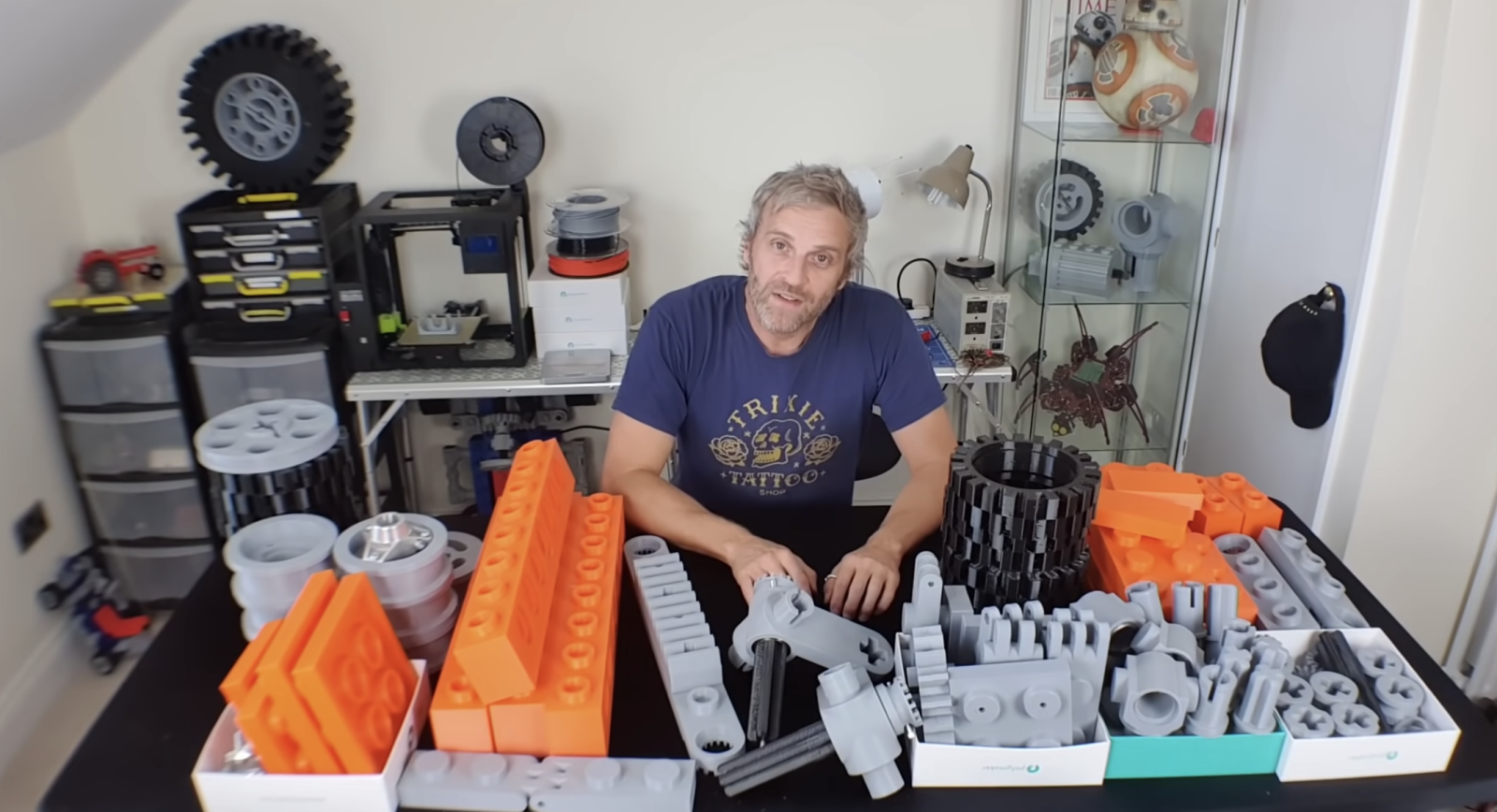
2021年11月,一年一度的Formnext展会上,马特将这款卡丁车带到 Polymaker的展台,正式登台亮相。
卡丁车的魅力吸引了无数参展观众的目光,他们纷纷停下来驻足拍照,跃跃欲试。而马特的YouTube 频道中,与卡丁车项目相关的视频已获得180 多万次的观看次数,深受观众喜爱。
产业结构不断更新调整的当今时期,制造业低碳排放的概念屡被提及,电动汽车的推广使用是一种必然。马特卡丁车3D打印项目唤醒了大众的创造力,依托家庭环境下的3D打印,用户可以设计定制属于自己的代步工具。一方面,这相对减少了大工业模式下污染的大量排放;另一方面,产品生产运输的方式不再单一限定于全球地域间的运输模式,用户需求的改变相对减少了产品运输过程中的碳排放量,低碳生活模式,正在为大众所践行。
3D打印赋予了用户本地制造的实力,家庭环境下卡丁车3D打印项目的成功,验证了这一制造技术的无限可能。人们将重新开始思考3D打印技术的应用范围,这一应用前景,已不再遥远。
3D打印,打印可能无限,Polymaker将继续投身于国内外增材制造行业相关的各类顶级展会,促进行业内外交流与合作,提高品牌知名度,发掘更多富有特色的创意应用案例,为3D打印行业的未来性发展提供支持。
超能机甲,军事对战,热血动漫的画面。
宏大广阔的游戏背景中,总有一些特定的象征物,唤醒人们对少年时光的追忆。
也许,我们需要一种方法,打破次元间隔阂,将记忆中的形象转换为现实实体,重温旧时印象。
魔法启动 - 3D打印梦想具象
Polymaker专业用户澄羽创制所,为象征物具象化提供助力,澄羽创制所采用增材制造工艺打印钢铁重甲师系列模型,再现凛凛战甲,追梦少年时。
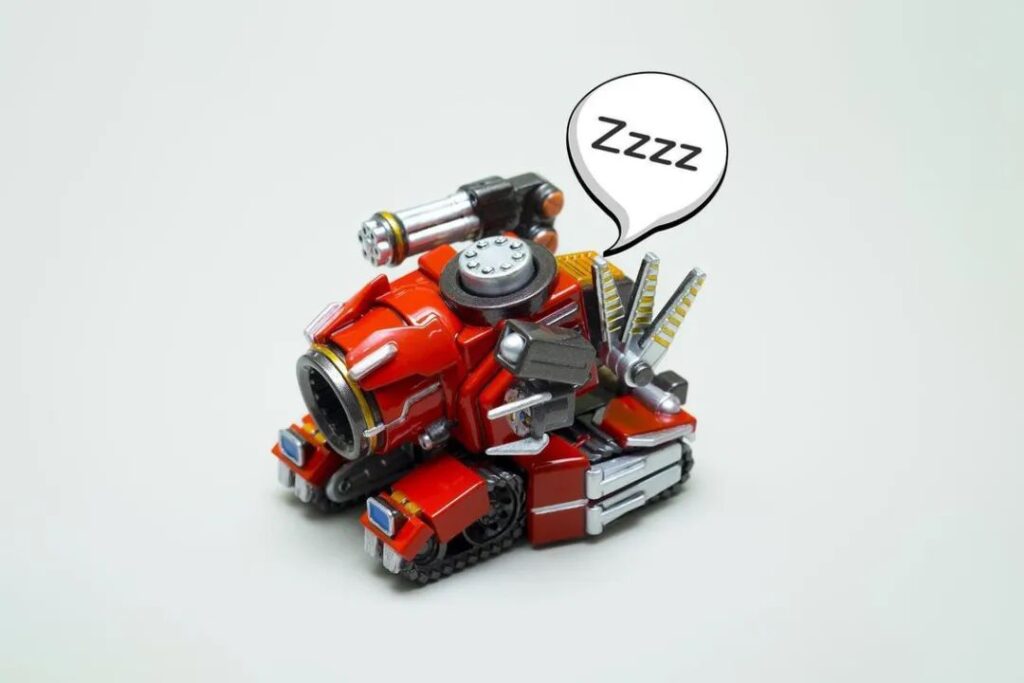
绯雨朱雀坦克模型
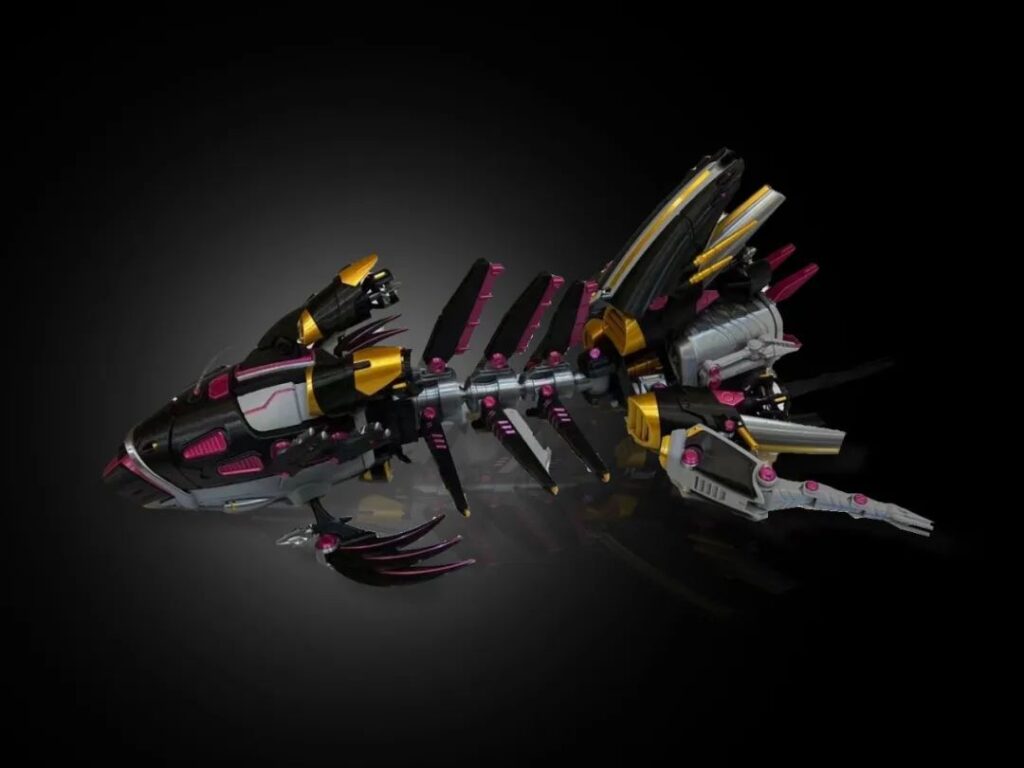
碧澜玄武潜水舰模型
钢铁重甲师系列作品,取材自海陆空三方兵种各类军事器械。原本威严富有力量感的军备器械在设计师笔下,以Q版模型的形式进行精细地再造还原。这一系列中,力量感与童趣并具,动画画风十足,线条勾画灵动,模型活力毕现。
海外社媒平台Facebook上,澄羽创制所打造的绯雨朱雀坦克与碧澜玄武潜水舰3D打印模型,为广大青年玩家群体所喜爱,在这些模型中极为亮眼。
烈焰正燃 - 绯雨朱雀坦克模型
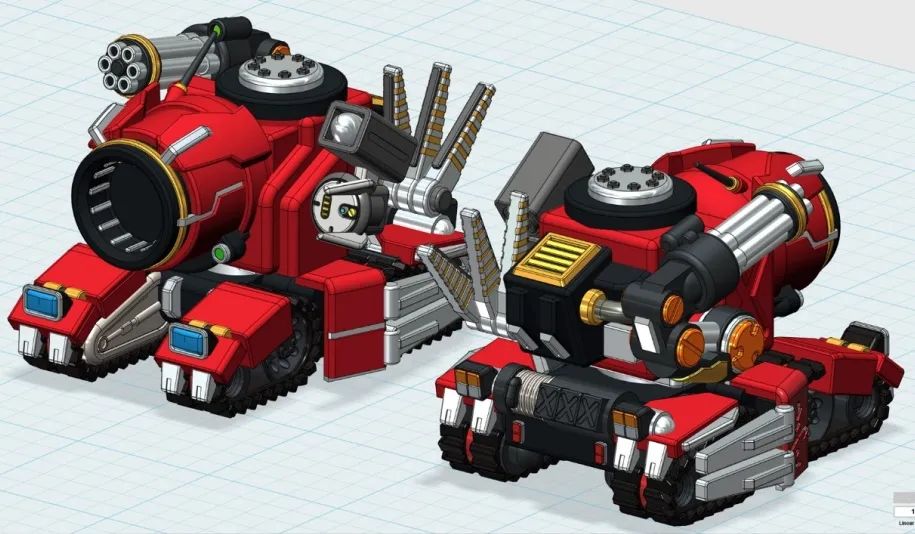
Hyper Q系列 绯雨朱雀-真红夜莺设计图
本款坦克模型以日本横版射击游戏《合金弹头》系列中SV-001型坦克为灵感来源,澄羽团队基于原版坦克设计风格进行新一轮的设计创新,相较于旧版设计,新版坦克增添更先进、现代化的铠甲与武器元素,科技感十足。
随后,澄羽团队采用建模软件123D Design 3D建模绘制坦克模型,FDM工艺打印成型,初期服务于创客群体3D设计教学使用,而后也可兼顾玩具手办爱好者收藏赏玩所需。
本款模型采用模块化生产方式,Polymaker PolyLite™ PETG 作为打印材料,该材料具有均衡的机械性能,颜色选择多元丰富,易于打印。
“以往3D打印件脆弱的概念因而改观,使用Polymaker PolyLite™ PETG 制成的打印品十分坚固耐用,适用于多类设计应用,这正与我们可动性玩具设计理念不谋而合。模块化生产方式的可拆卸性和多样性特质与3D材料结合,优势尽显。”
静水平波 - 碧澜玄武潜水舰模型
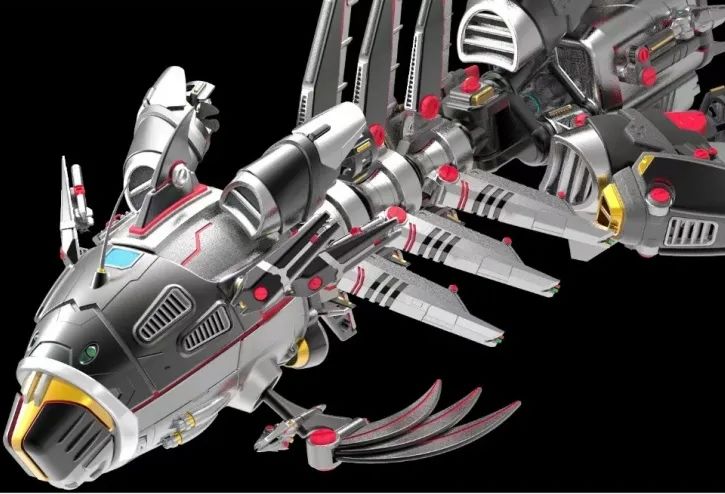
Hyper Q系列 碧澜玄武潜水舰模型设计图
潜水舰模型设计中,设计稿采用机械设计风格。舰身模拟游鱼形态,整体线条呈流线型,轻盈自由。鱼鳍在水中舒展张合,鱼体升降沉落,与潜水舰在水中平分水流,自主沉浮,系出同源。
舰艇模型使用PolyLite™ PLA 系列和PolyFlex™ TPU95 材料进行打印。PolyLite™ PLA 材料可靠性与打印易用性兼具,强度高,是产品设计,装饰品,玩具道具打印的理想选择。PolyLite™ PLA 丝绸色系列材料应用中,打印件色调饱满明亮,富有金属光泽感,舰体质感得以进一步跃升。PolyFlex™ TPU95,作为柔性材料,其邵氏硬度为95A, 可依托舰体模型设计,增减填充实现不同的弹性效果,为舰体模型可动性设计提供助力。
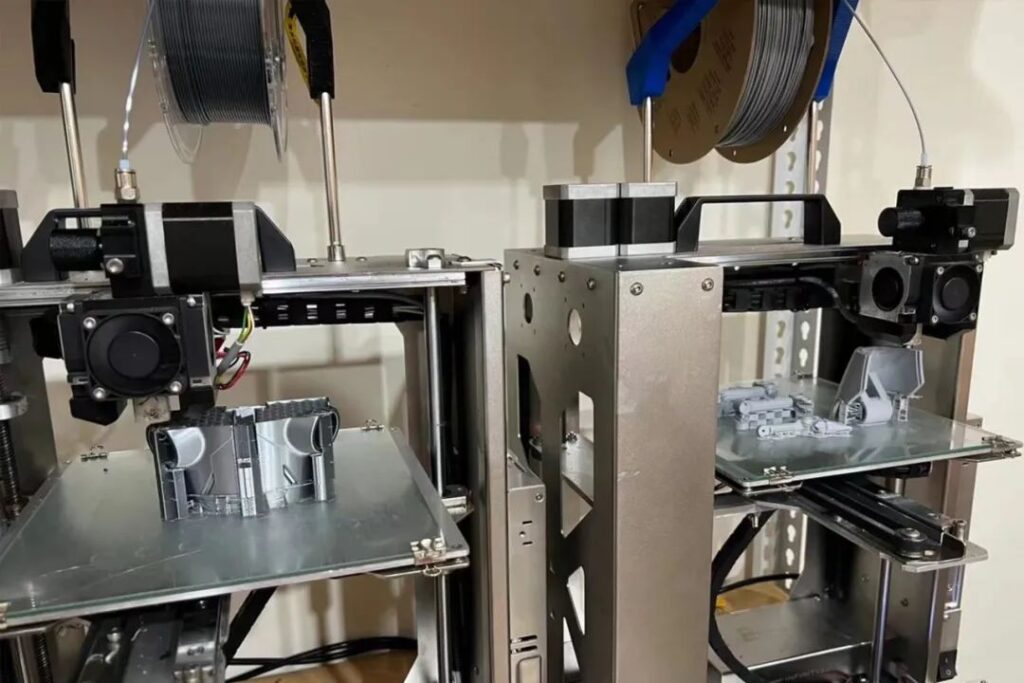
模型分装中,打印组件达300多件,零部件精细程度要求极高,设计、打印、拼装耗时较长。澄羽团队精益求精,精密规划每一处零部件使用,确保舰体模型可根据不同战略模式切换具体形态,满足手办模型使用多功能应用要求。
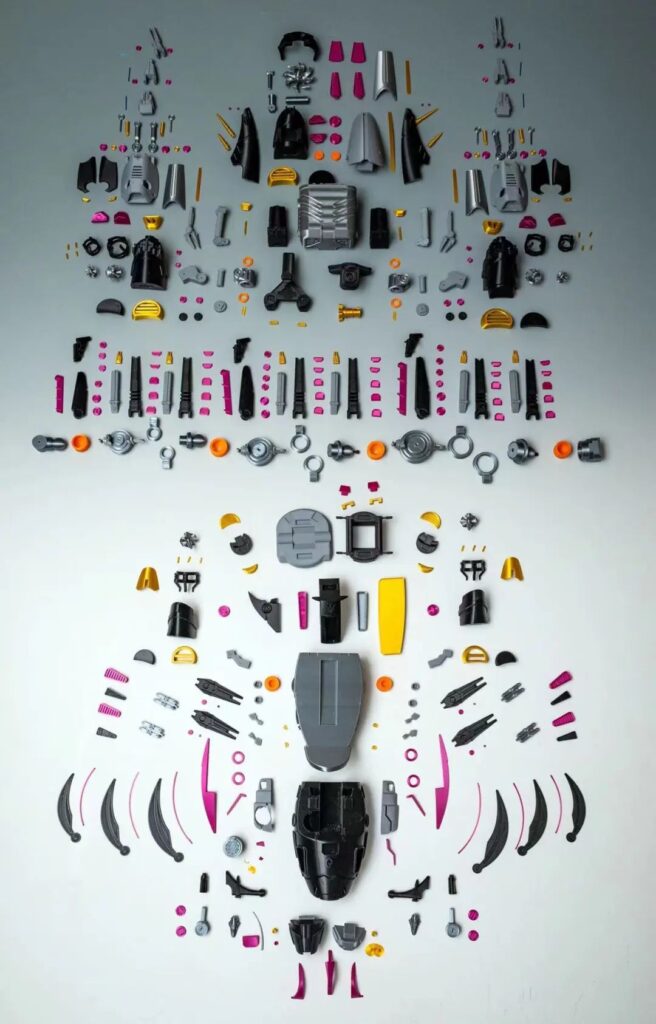
零部件顺次排开,井然有序,色彩斑斓,结构整合,框架分明。
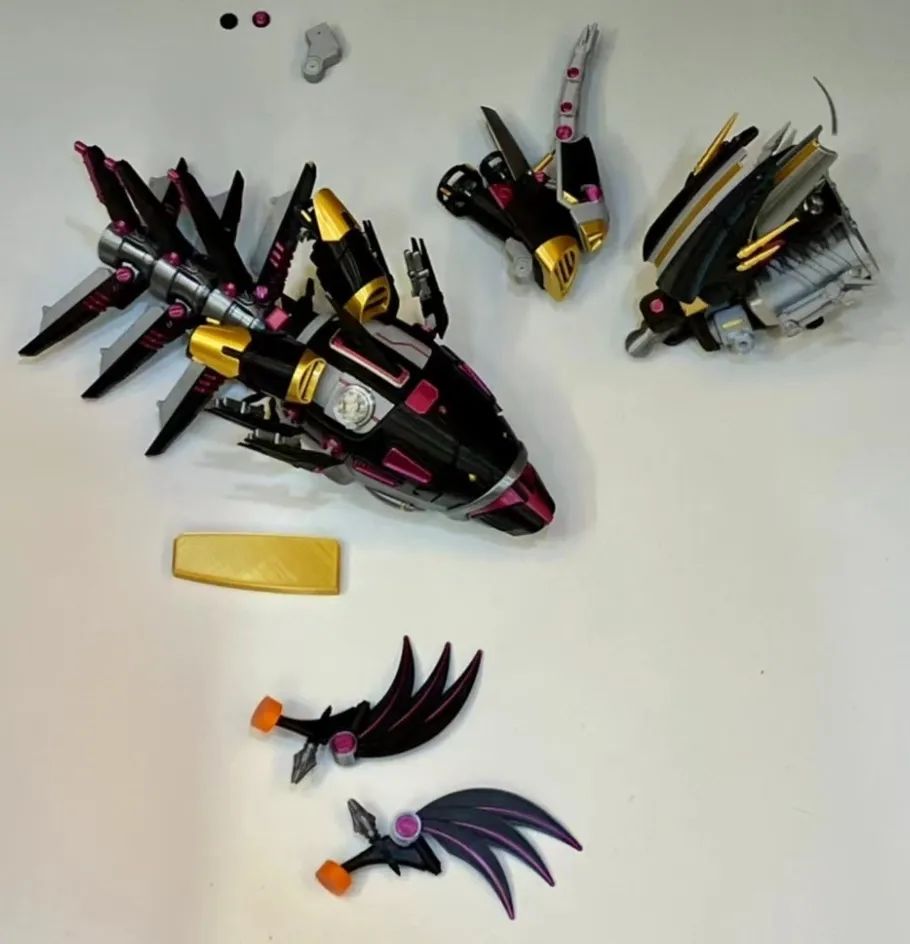
拼装中期,鱼体形态,呼之欲出。
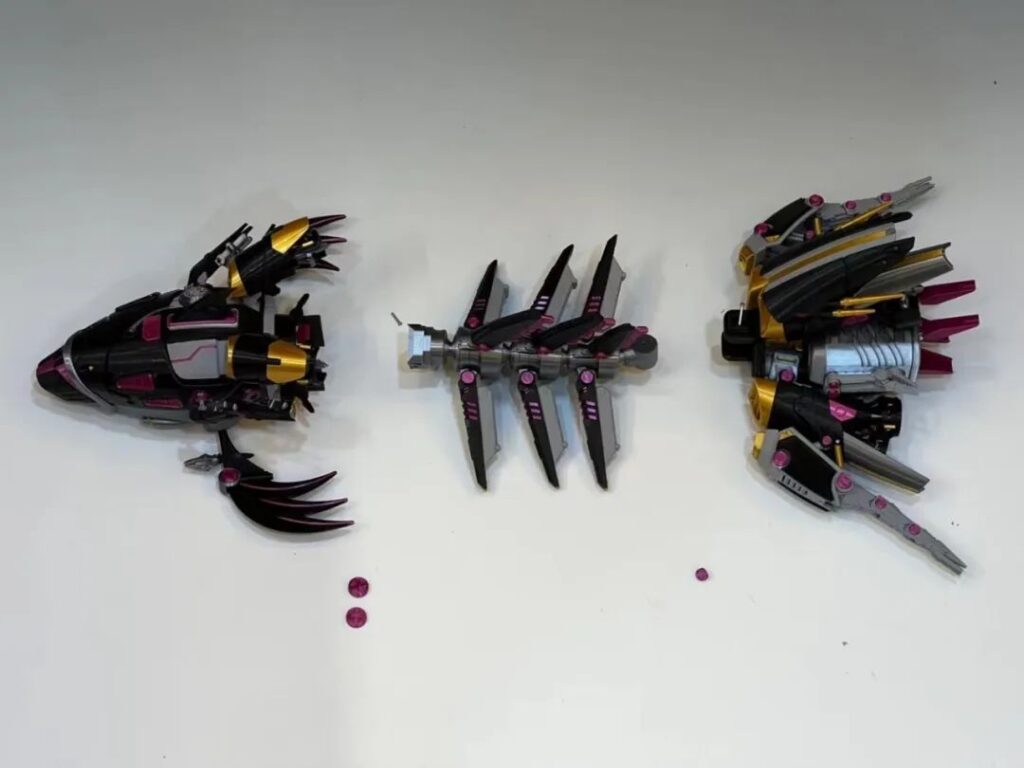
舰体头部为控制室,鱼骨中端形态链接整体结构,尾端助推,乘浪扬波。
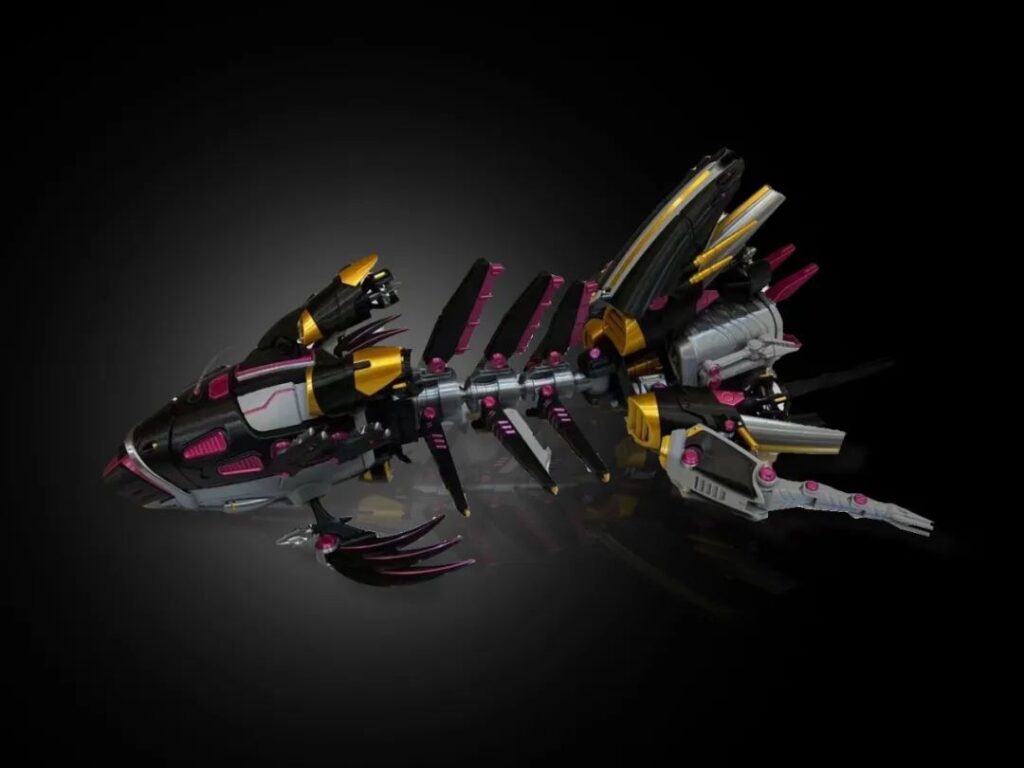
终于与大家见面啦!谁想做第一个潜行者?
3D建模精准绘制,设计创意优化更新。澄羽团队将探索发掘的目光投向3D打印领域,依托增材制造工艺留存无数玩家的少年梦想。3D打印打破现实世界与虚拟空间中的次元壁垒,将玩家记忆中的象征物转换为实体模型,为青年玩家群体圆梦。
绯雨朱雀坦克,碧澜玄武潜水舰两款模型,正是3D打印创意爱好者对打印美学应用的一次成功尝试。伴随着FDM工艺的日益改善提升,3D打印技术将更广泛服务于大众级消费市场,满足使用人群定制化应用需求。未来,无限可能。
特别感谢起点设计协助收集整理资料,澄羽创制所提供完整精彩案例。
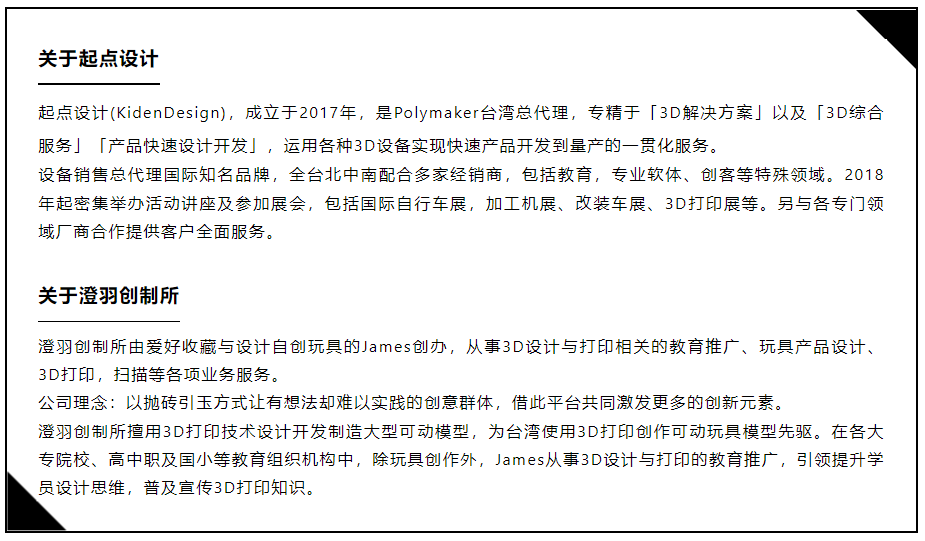
3D打印技术是当今时代的风潮制造工艺之一。其高精度,高复杂度的工艺特性,适用于制造结构复杂的机械零部件。在3D模型打印中,3D打印技术赋予制造工艺无限可能,将三维设计精确转化为实物模型,简化生产制造过程,满足使用者个性化定制需求。使用3D打印技术“自体复制”3D打印机,已成为许多打印玩家的创意选择。
本期,Polymaker专访3D打印玩家曹子杰,聆听自主拼装Voron 3D打印机玩家心声。
概念初生
使用打印机来打印另一台出色的打印机,这一概念本身就令人着迷。受国外网站开源Voron 打印机项目影响,曹子杰决定自主打印拼装Voron 2.4 3D打印机。Voron外观颜值高,结构稳定,性能优异,是玩家DIY打印机的首选。
对于长期浸染3D打印圈的玩家来说,选择一台打印精度高、结实耐用、适应打印者个人需要的3D打印机,颇为重要。
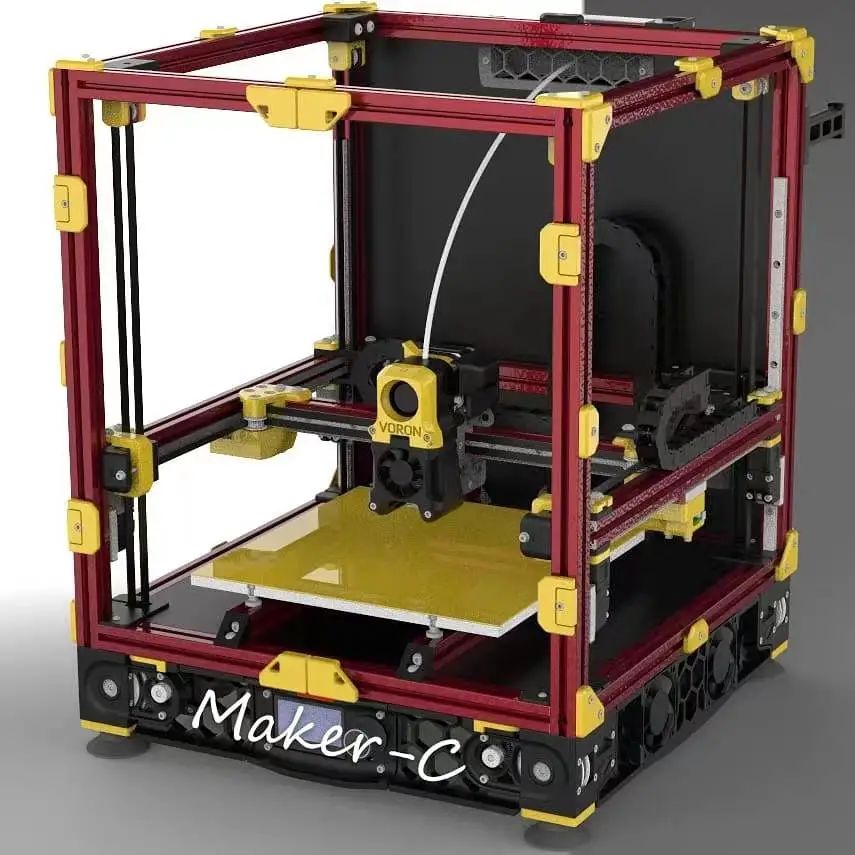
曹子杰自主拼装Voron 2.4 打印机
材料推荐
VORON 2.4是全封闭式设计,CoreXY架构的高精度打印机,采用直线导轨运动, Z轴四根皮带调平。
在打印件的材料选择中,曹子杰推荐耐高温的尼龙材料打印喷嘴挤出装置等结构件,尼龙材料强度高,可在打印中适量减少填充,减轻结构件重量。ABS材料颜色选择面广,美观度高,亦适用于各类连接件应用。
组装打印机
1. 打印Voron打印机所需结构件
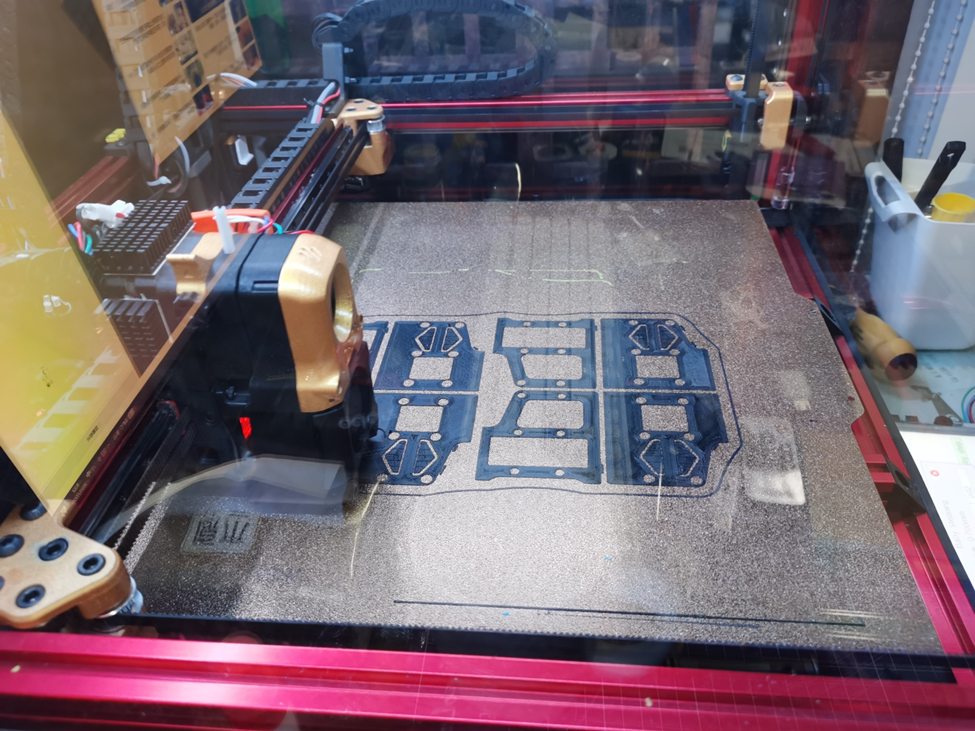
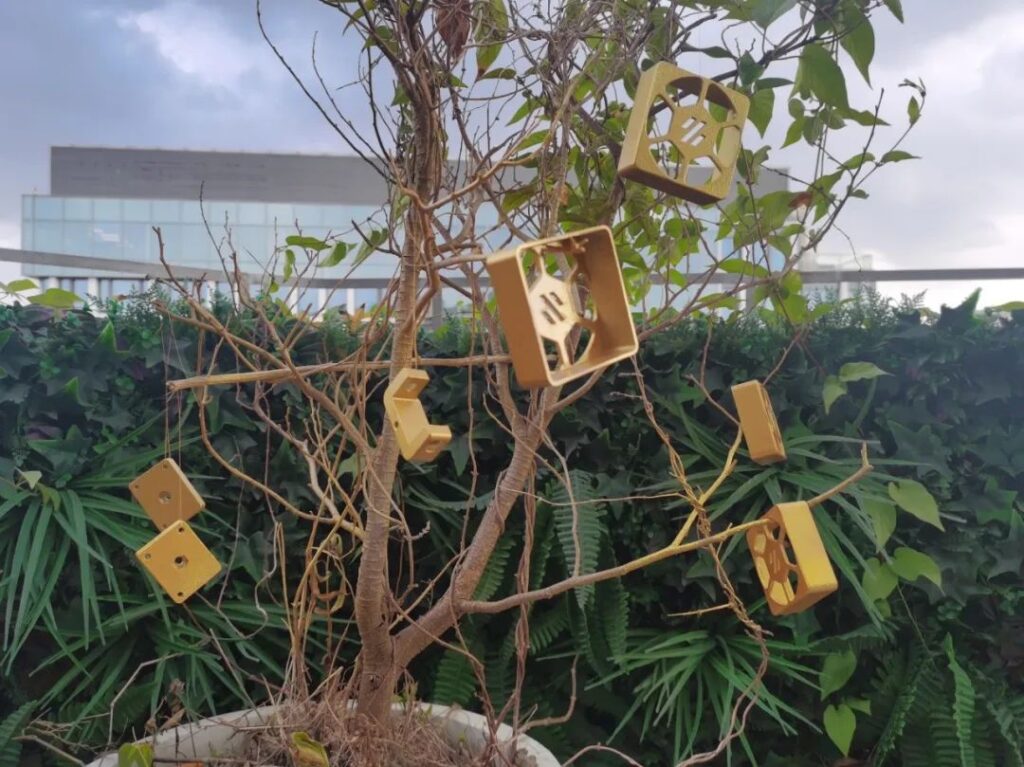
2. 采购通用零件,框架搭建,结构组装

3. 接线通电
4. 固件导入,打印机系统运行
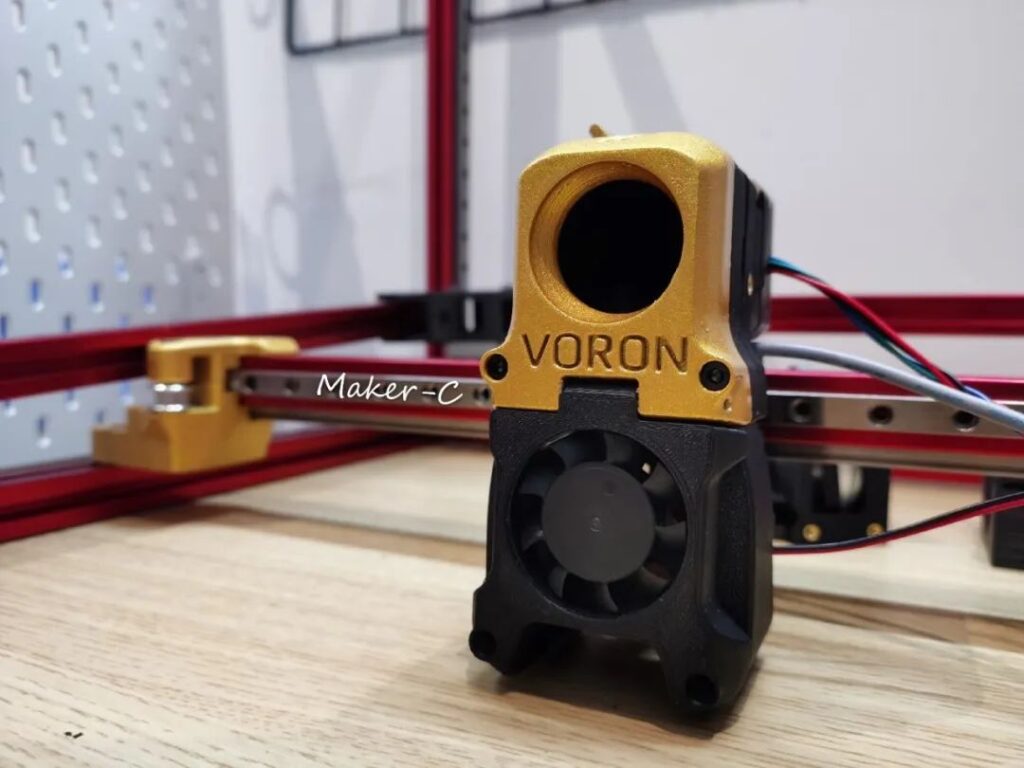
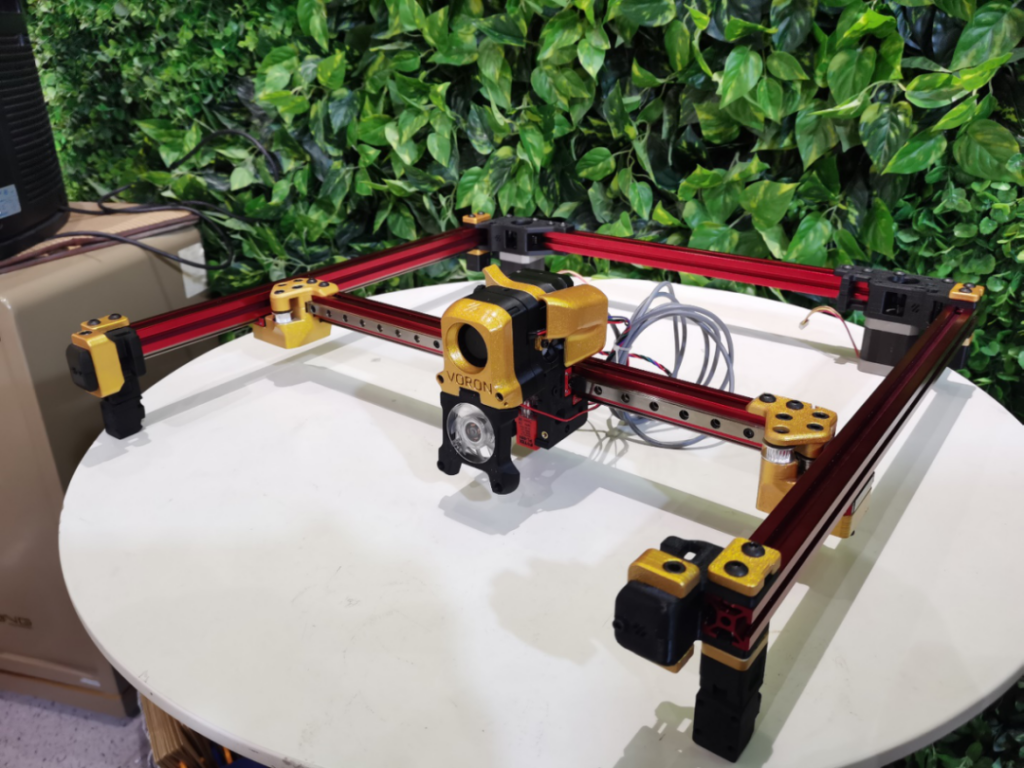
5. 微调(注意电机转动方向,调平喷嘴与底板间距离,检查加热功能)
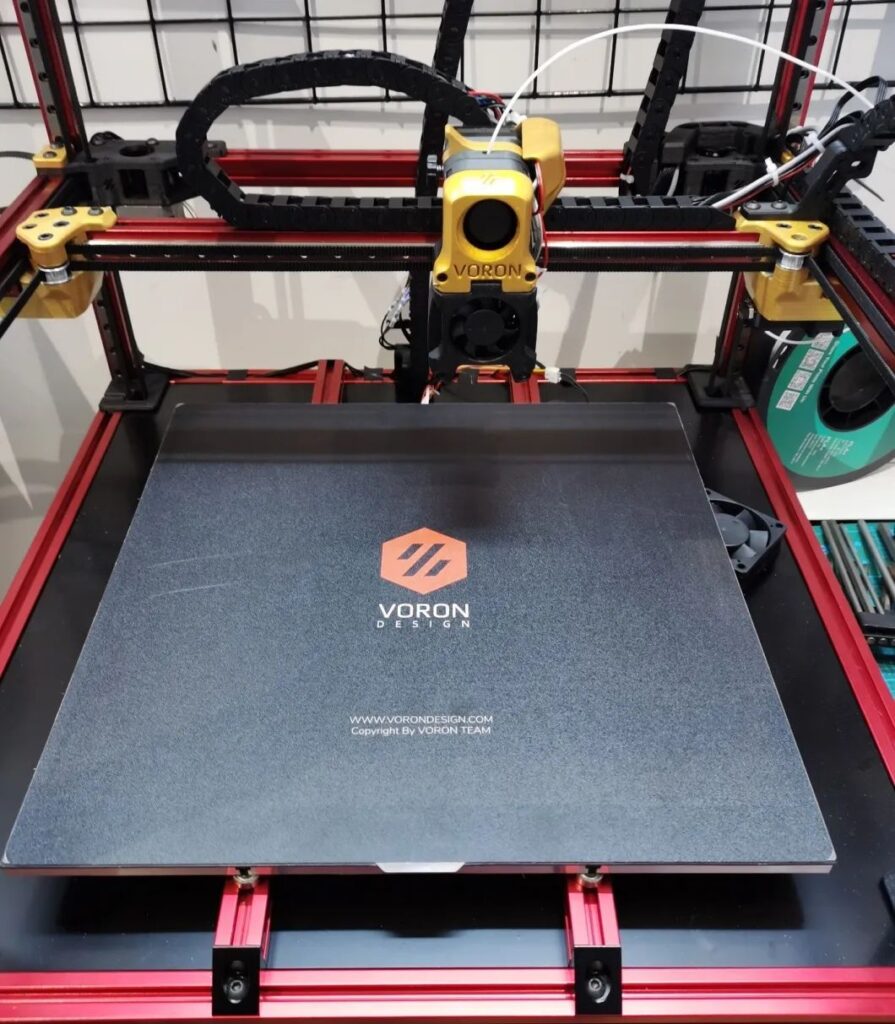
6. 打印测试件
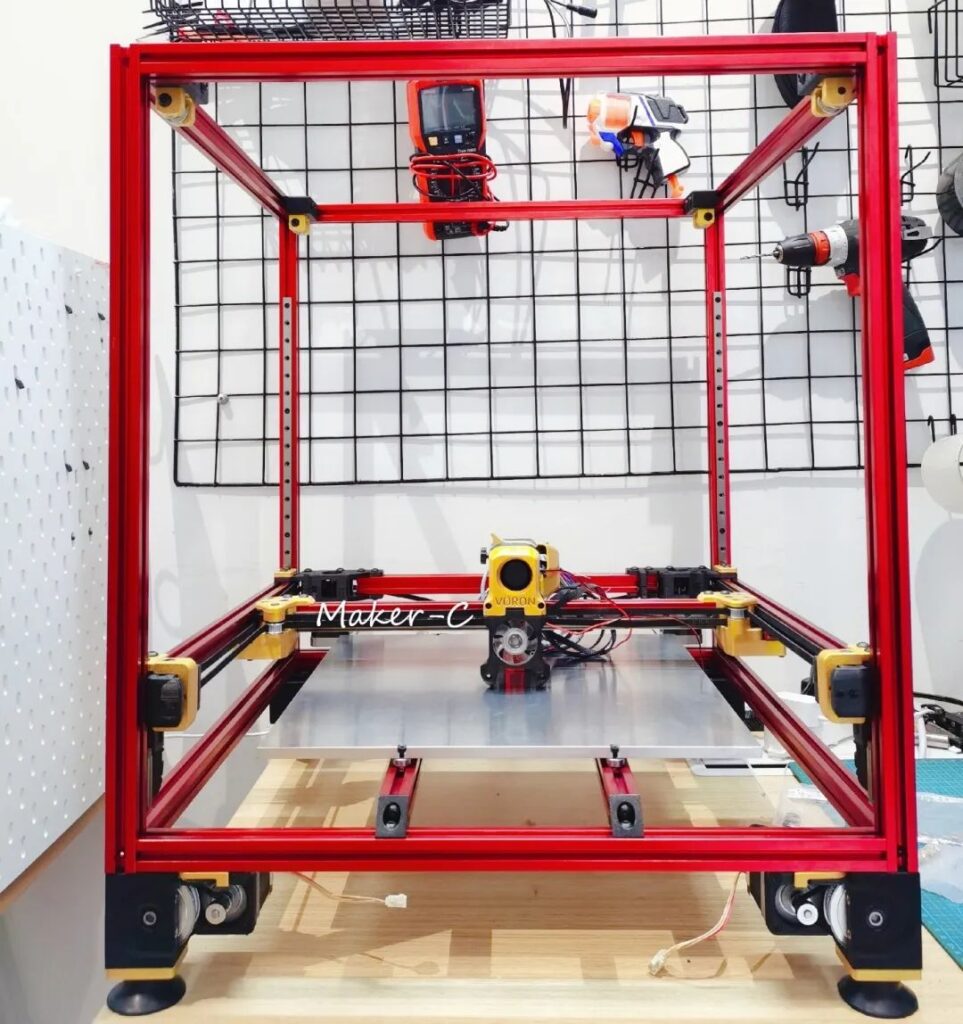
曹子杰表示:“从不同打印材料间甄选区别,打印机结构运行逻辑理解,到电路走线,五金标准件采购,在这些复杂而漫长的准备时光中,我深刻了解打印机的使用原理。3D打印圈子中,大家因共同的志趣而相聚,我期待更多新人接触3D打印机组装项目,将创新性的设想融入3D打印机优化调整,为玩家日常使用打印带来便利。”他也提醒,打印中应保持通风环境,组装零部件时需理清逻辑顺序,打印机后续使用过程中适宜多次检查皮带松紧度情况,及时上油维护线轨使用。
Voron打印机的开发,是一款优秀的开源项目,玩家可通过项目学习改进打印机设计,实现打印机性能进一步优化升级。在打印机迭代完善中,设计者的应用理念可反复具象化打印后投入应用,推陈出新。曹子杰考虑在后续优化中,加强打印机轻量化结构构建,模型结构散热设计调整,并重新合理规划整体接线布局,为打印机注入新的生命力量。
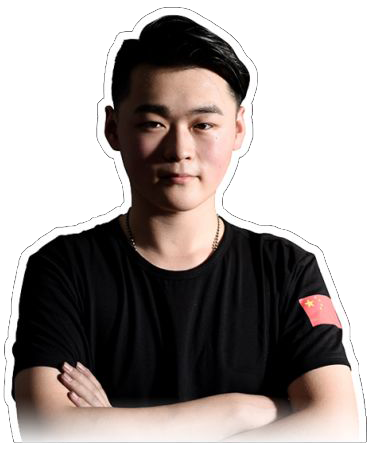
曹子杰:毕业于上海外国语大学贤达学院,本着对机械设计的热爱,2015年开始玩3D打印机至今,从事格斗机器人的设计与制造,运用3D打印验证设计可行性,致力于将3D打印带入生活中的实际应用。
这是Polymaker台湾独家代理商起点设计与雷神艺术工作室合力打造3D打印“喷火龙”模型。
造 l 梦 l 伊 l 始
精灵宝可梦(神奇宝贝)是陪伴孩子们成长的日本动漫。红白相间的精灵球,本领各异的神奇宝贝奇幻而热血的成长历程,培养了孩子们对于勇气和友谊的认知。他们渴望有朝一日,能亲手触碰这些儿时的朋友,和他们在现实中相遇。
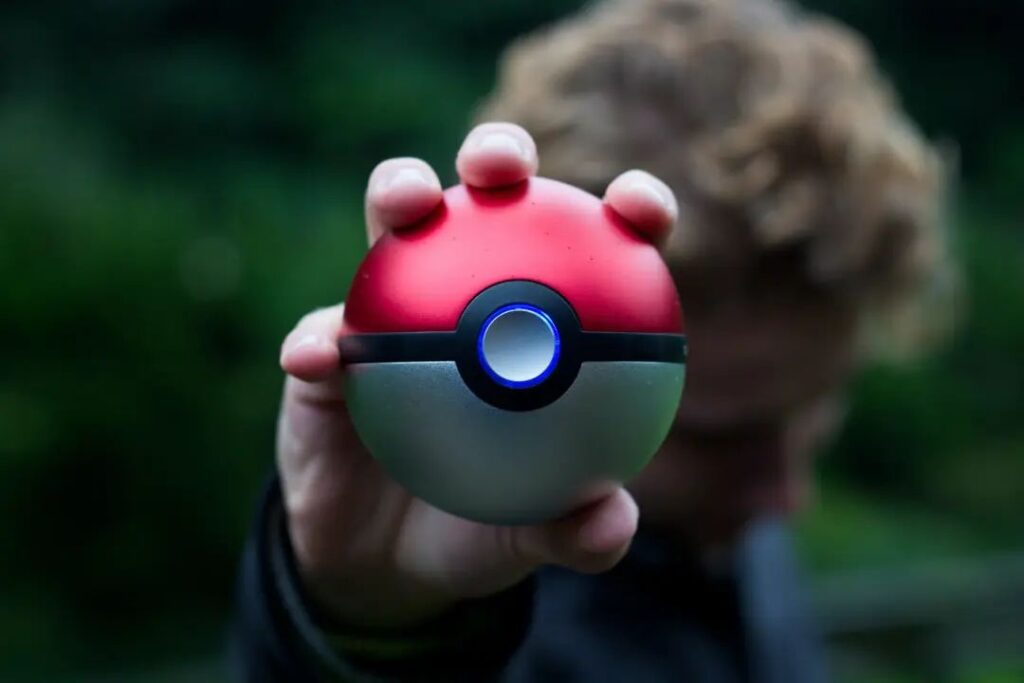
诞 l 生
3D打印助力圆梦喷火龙(粉丝艺术创作模型)诞生
Polymaker台湾代理商-起点设计, 与雷神艺术工作室合作,依托于增材制造工艺及基础将虚拟人物变换为实体模型,雷神艺术选用宝可梦粉丝荒神Kojin 3D Studio的二次创作喷火龙3D设计稿,实现打印创新。
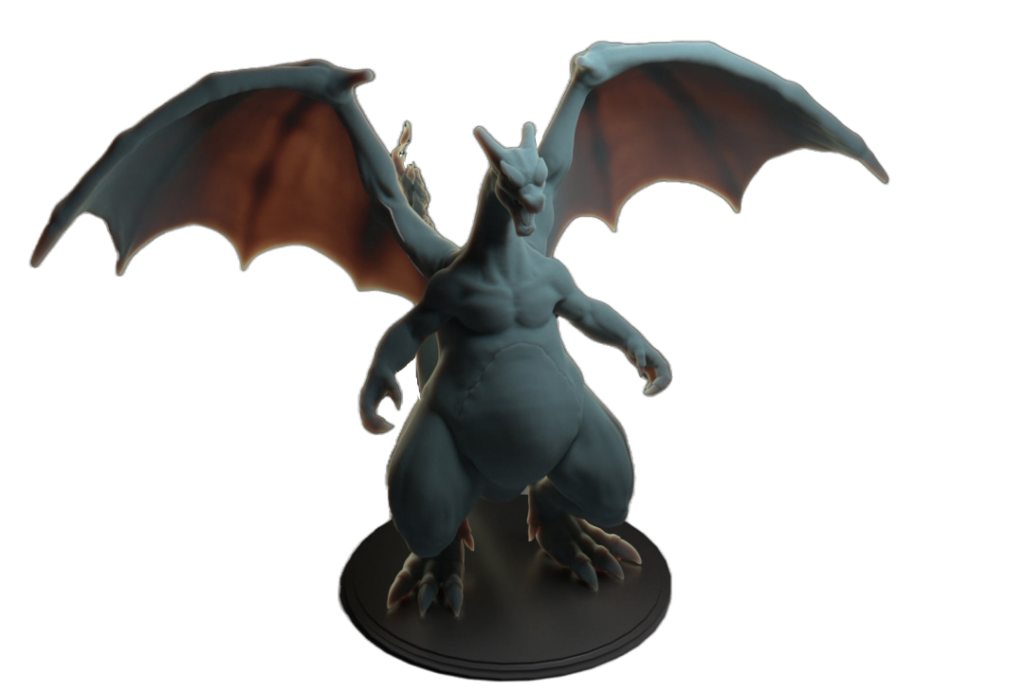
闪光巨龙——荒神Kojin 3D Studio设计图
造 l 梦 l 初 l 始
喷火龙(粉丝艺术)3D模型雏形
荒神的设计兼具美式风格和力量感,在与雷神团队合作中,第一版3D打印模型顺利诞生。
该模型高约60厘米,选用玻璃纤维及发泡打印材料打印,大块组装部件通过FDM打印工艺完成,细节处与透明部件由光固化工艺打印完成。
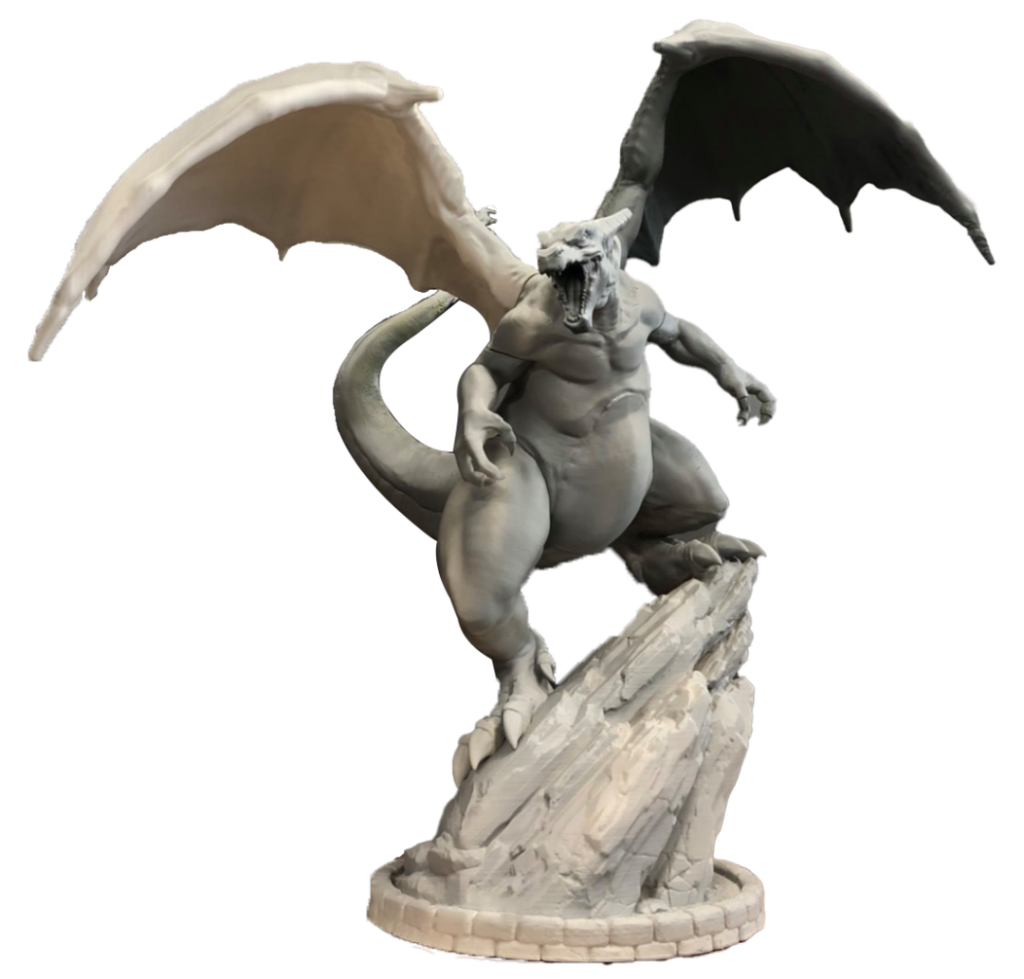
未上色版本里,嶙峋斑驳的岩石上,巨龙怒吼。向内靠拢的双翼,似乎鼓满了风,双翼柔韧而有力。
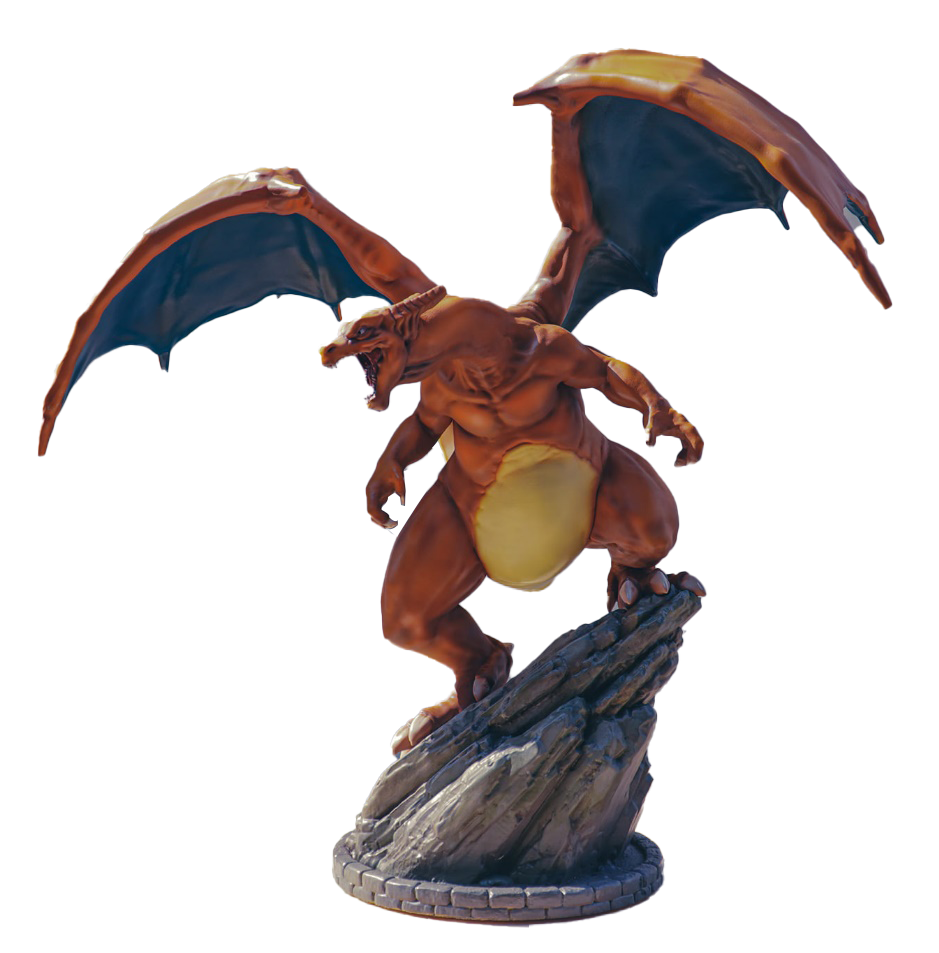
手工打磨细修,喷涂上色。
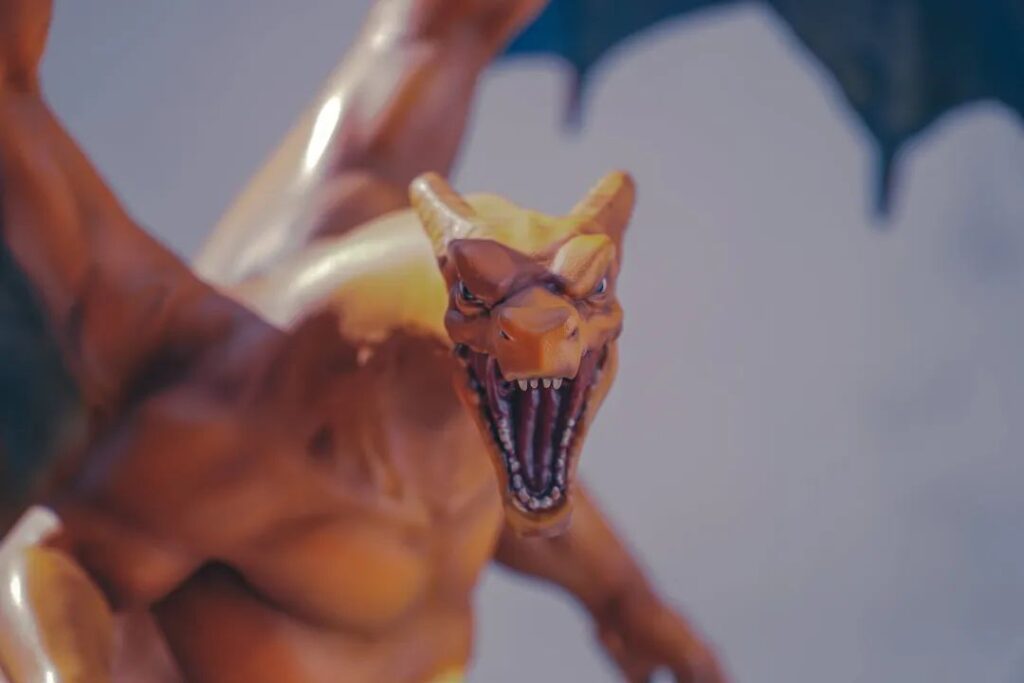
浅橙色与阳光交织,呈现出一种和谐的力量美感。
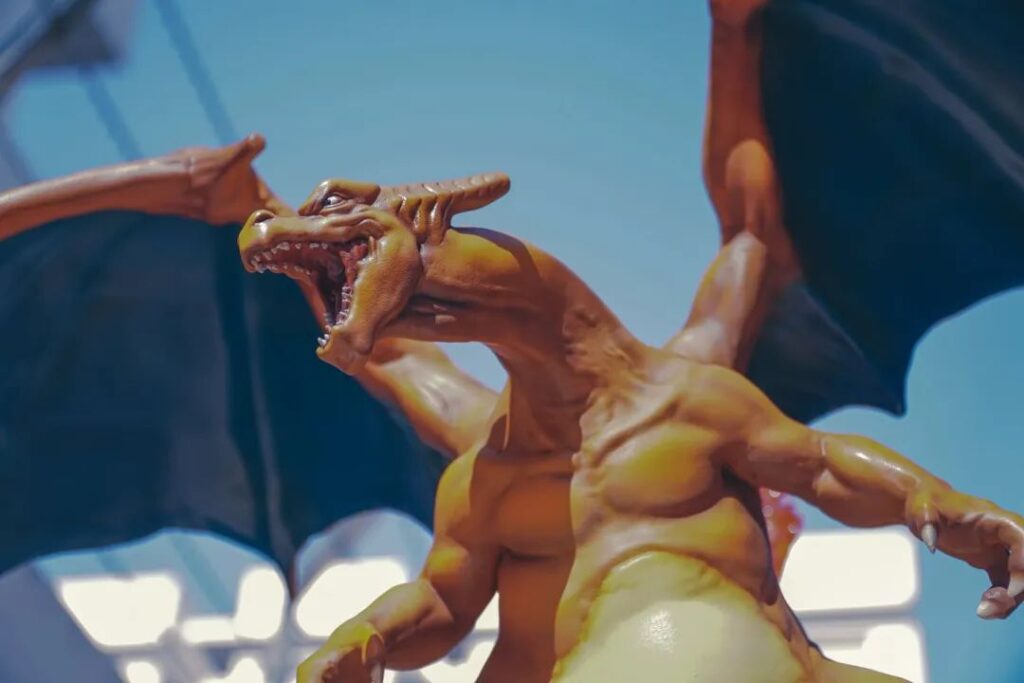
龙颈处青筋毕现,强健的肌肉刻画,3D打印所保留的细节美感在模型着色后展现得淋漓尽致。
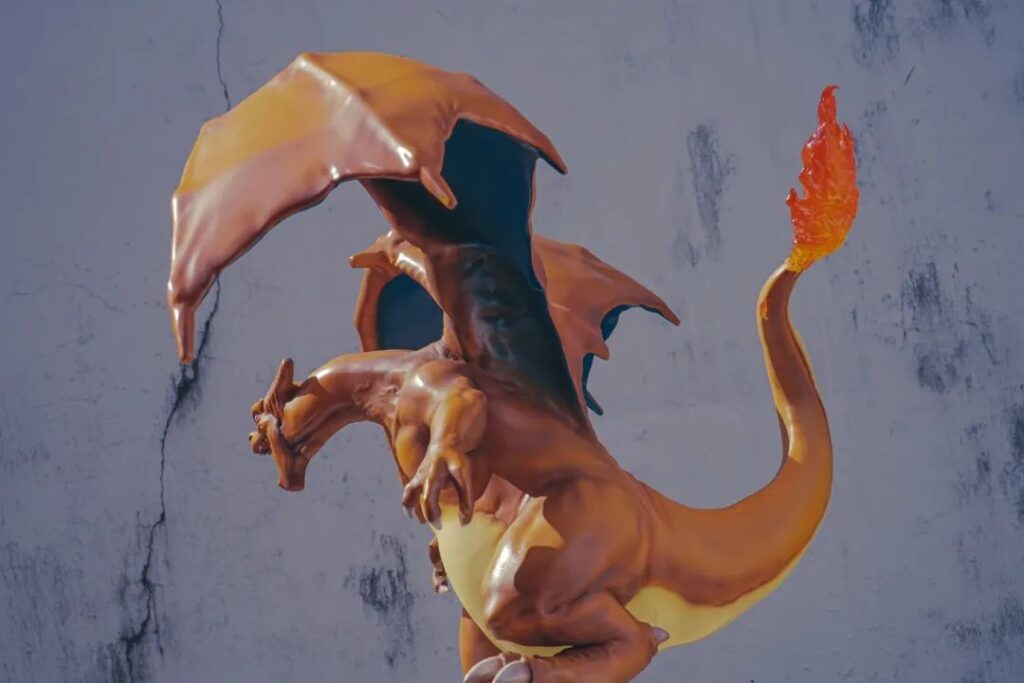
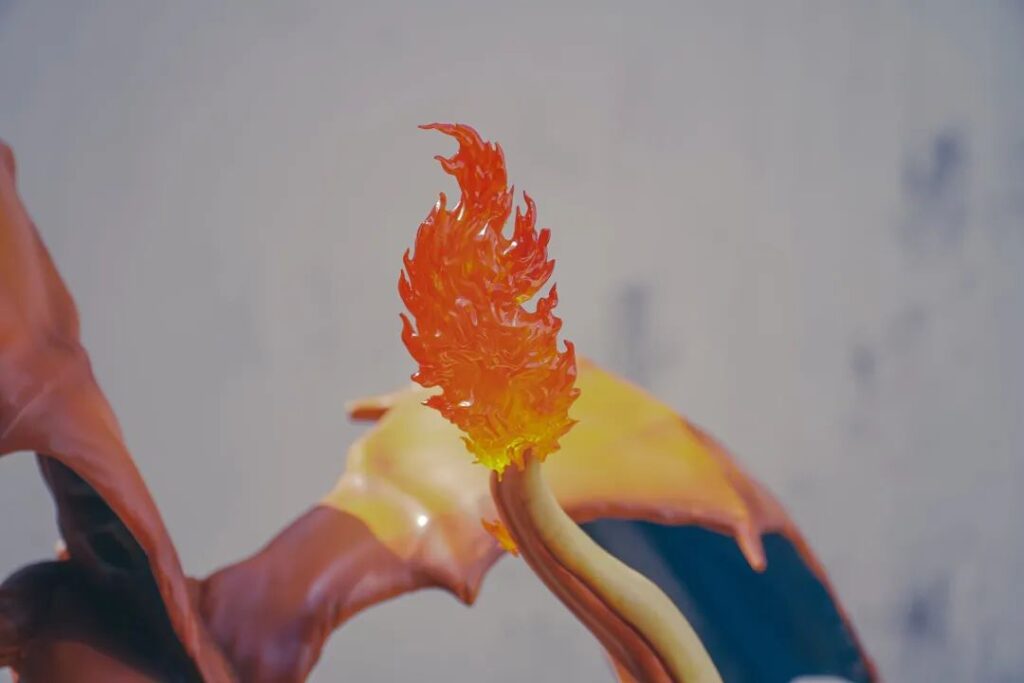
龙尾尖处燃烧的火焰,橙红的烈焰深处转为金黄,透明部件在阳光映衬下,火焰安然燃烧,栩栩如生。
造 l 梦 l 再 l 燃
黑龙模型
雷神团队很快开始了新一轮的打印尝试,宽阔的展览场地赋予他们充足发挥空间,荒神版巨型闪光喷火龙模型闪耀登场。
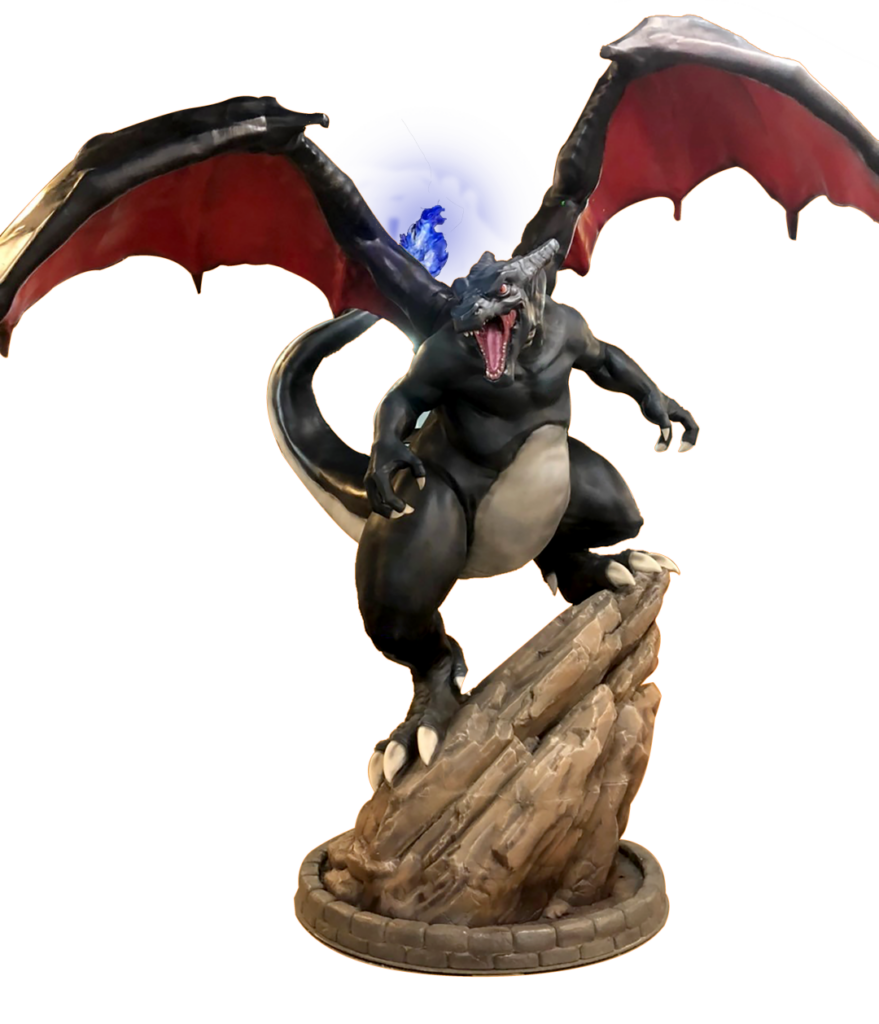
相较初版模型的力量美,新版黑龙模型体积上更具优势。模型高约3.5米,雷神团队选用PLA进行全套FDM打印,历经两个月打印,一个月时间拼接,打磨,补强,处理接缝,焊接骨架,一天喷涂烤漆最终完成。
由于黑龙模型体积较大,需要钢架结构支撑,组装搭架工作艰巨,雷神团队在每片交界处反复校正,保证模型组装贴合精准,严丝合缝, 使模型整体表现优异,富有细节美感。
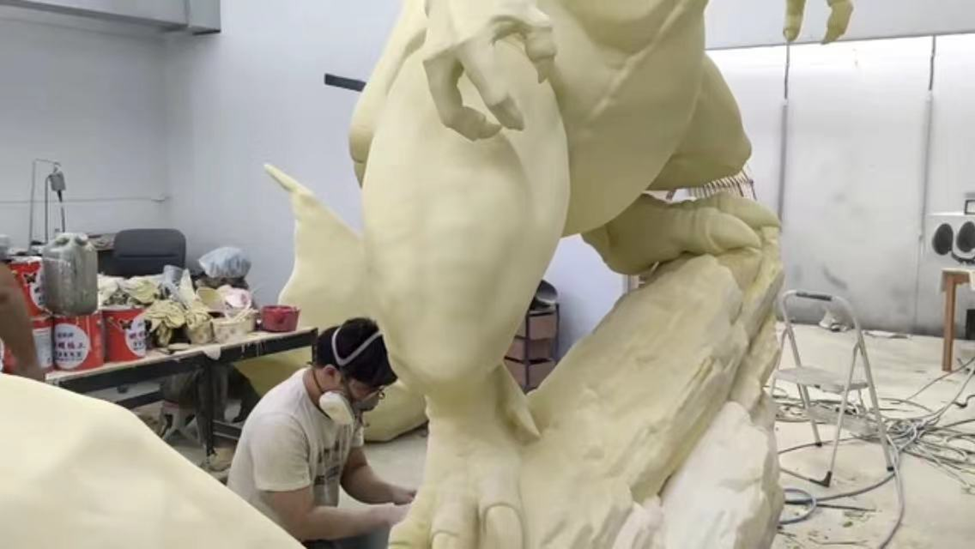
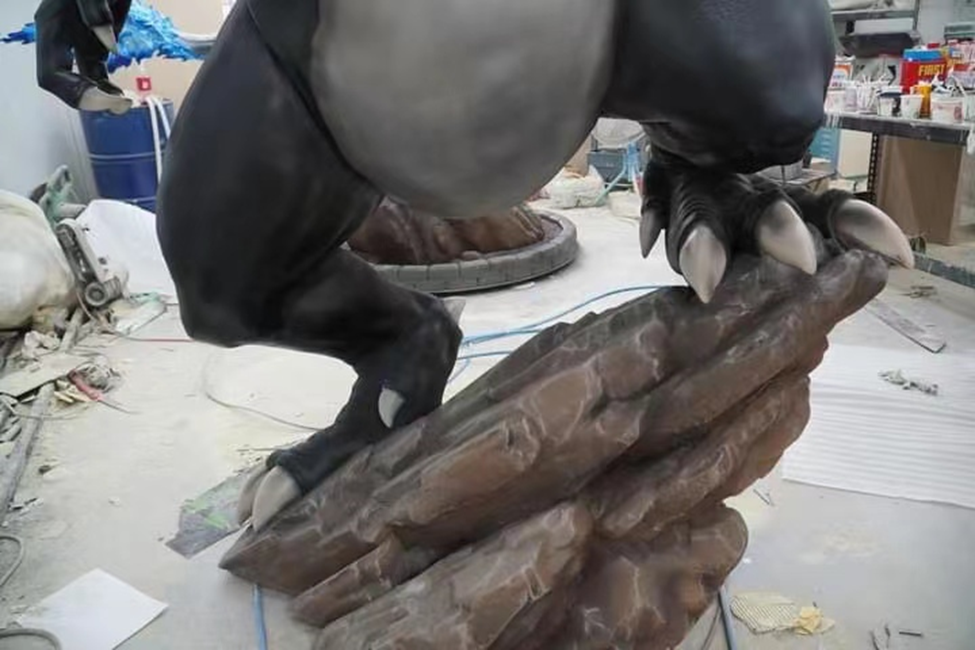
大型黑龙模型的诞生,离不开团队的守护。十五人的团队中,实际五人参与制作,一人拆图,一人负责打印,组装,打磨打印件并涂装。
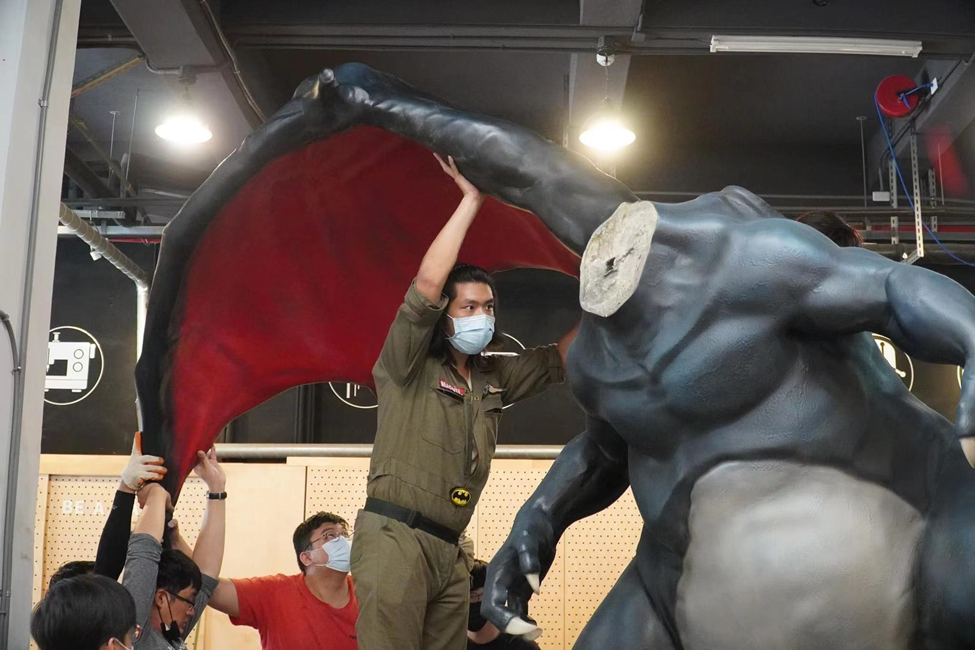
准备拼装,感受下模型的肌肉线条与夸张体态。

龙尾尖处线条逶迤,冰蓝色的火焰静静燃着,似火如冰,具有一种奇异美感。
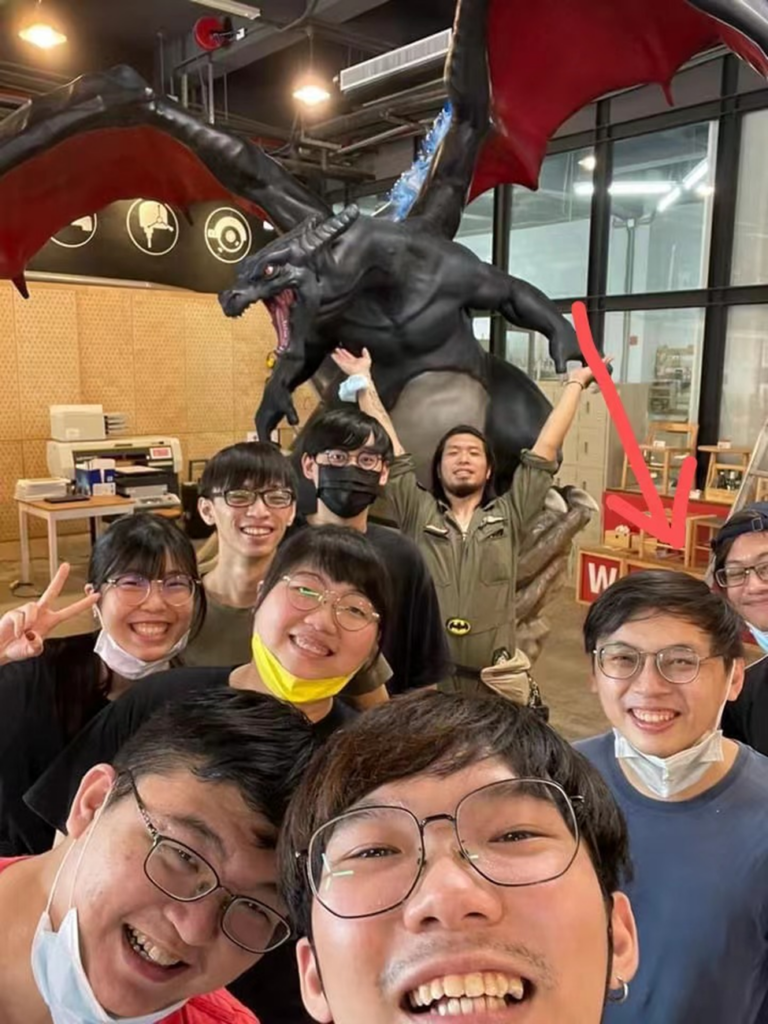
两次打印,创造梦成。精确的3D建模实体复制,设计的无限可能,多种材料组合,3D打印使宝可梦玩家童年的梦具象化,为怀揣童年梦想的孩子圆梦。3D打印技术可满足使用人群定制化需求,根据切实需求客制打印品,方便玩家收藏所需。
梦想与现实,并非遥不可及的两条鸿沟,理想串联中路,尖端科技沟通循环。孩童的热血与希望,科技的安静与力量,彼此交融,3D打印工艺正在飞速成长,将不断将行业参与者的创造梦想落地化为现实,而这未来性的视角,也将这一工艺推向更远。
特别提醒:本文涉及的所有宝可梦相关打印文件及打印件,均为粉丝自发的二次创作,不涉及任何商业用途。
关于起点设计
起点设计(KidenDesign),成立于2017年,专精于「3D解决方案」以及「3D综合服务」「产品快速设计开发」,运用各种3D设备实现快速产品开发到量产的一贯化服务。
设备销售总代理国际知名品牌,全台北中南配合多家经销商,包括教育,专业软体、创客等特殊领域。2018年起密集举办活动讲座及参加展会,包括国际自行车展,加工机展、改装车展、3D打印展等。另与各专门领域厂商合作提供客户全面服务。
关于雷神艺术工作室
雷神艺术工作室主要从事产品打样及后端生产,我们主要承接海内外的知名IP商品或电影公司道具或商品的打样制作,透过数位加工技术呈现出作品最精致还原的一面。
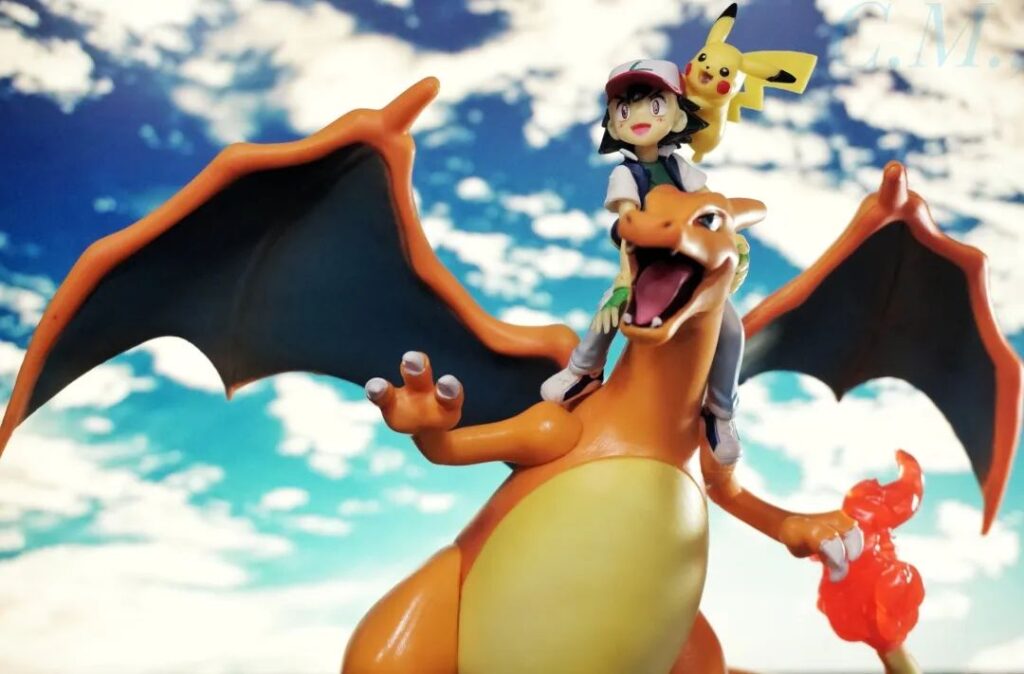
提起3D打印,高精尖,工业级等词汇常常从人们的大脑中浮现出来,长期以来,3D打印在工业领域的广泛应用使得这一名词似乎已经与科技化,严谨性密不可分。事实上,3D打印技术也已经参与到其他领域的应用之中,在以灵动自由为主旋律的人文艺术领域中,3D打印也展现出了它独特的优势。
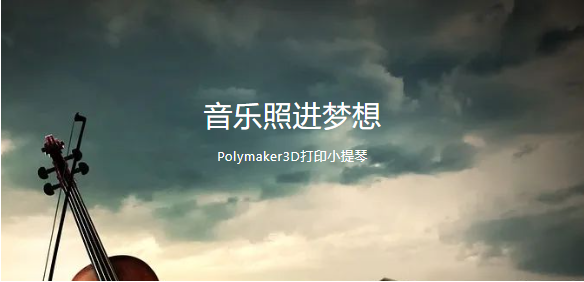
3D打印小提琴源始
让自由的艺术和音乐本身美的规律冲破技术的樊篱,给思想和心灵以自由。
--海顿
传统认知中,技术常常与自由灵感相背而立。灵感触动创作者的心弦,但如何让技术与灵感两条平行线交汇,却是一个值得探索的话题。资深3D打印玩家曹子杰独具慧眼,选择以西洋古典乐器小提琴为载体,实现3D打印模型与艺术统一。
3D小提琴的创作,融3D打印技术与艺术美感于泠泠琴弦之间,是一场科技与艺术的完美邂逅。小提琴的图纸设计者,大卫·佩里,来自美国俄勒冈州波特兰,是一名机械设计师,具有康奈尔大学的工程硕士学位。他在2013年设计了世界上第一款开源3D打印电动小提琴,并于2018年开始模块化小提琴项目。大卫将他一生对小提琴的热爱与先进的工程工具和技术相结合,制作出令人惊艳的3D打印小提琴。他的创作也受到中国打印玩家曹子杰的肯定,远隔重洋,大卫与曹子杰在科技与艺术的殿堂中惺惺相惜,引为知音。
择良材以制琴
古有斫木为琴,挑选合适的材料制作小提琴是3D打印的必然要求, 大卫所设计的小提琴兼具精巧的构架美感与富有科技感的外形特征,需要性能优良且适于多功能用途的材料参与3D打印。
大卫所设计的小提琴兼具精巧的构架美感与富有科技感的外形特征,需要性能优良且适于多功能用途的材料参与3D打印。曹子杰选用Polymaker三款线材PolyTerra™ PLA, PolyLite™ PLA Pro以及PolyMax™ PLA作为小提琴的打印材料,这三款材料性能各异,各有所长,为小提琴分模块打印拼装打下了基础。
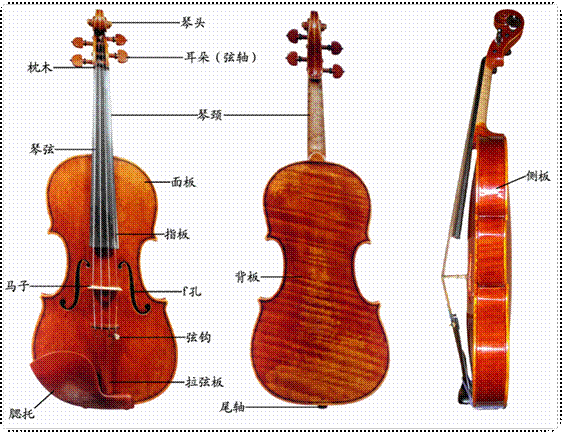
在3D打印小提琴中,曹子杰简化了传统小提琴相对复杂的结构分区,涉及3D打印部分主要包含琴头,面板,指板,琴码,拉弦板四区域。基于琴体结构各部分受力要求差异,材料选用也各有不同。
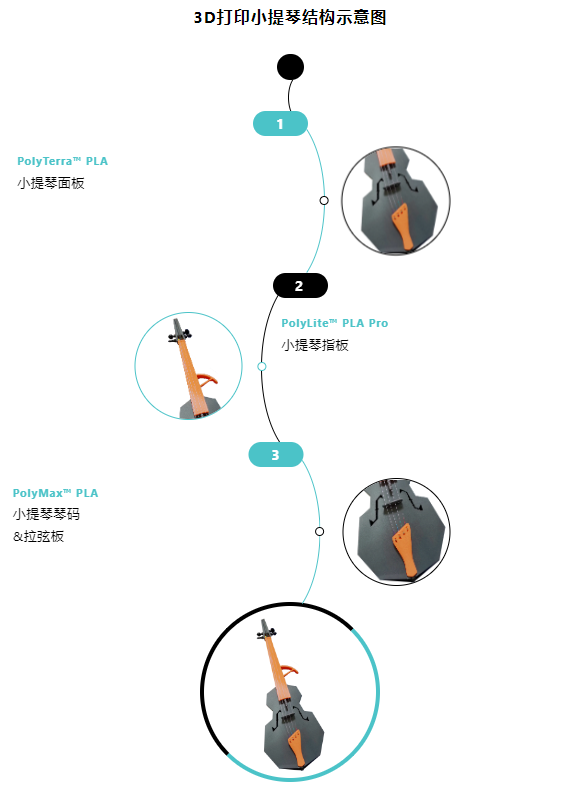
PolyTerra™ PLA - 小提琴面板
面板是小提琴最为重要的结构,它将琴码传来的琴弦振动发挥出来,而其本身的振动也相应地增强着琴声,使琴声富有力量感,优美动听。
曹子杰选用 PolyTerra™ PLA 打印琴体面板。PolyTerra™ PLA 色彩品类丰富,颜色区间选择颇广,可满足不同颜色爱好者的打印需求,同时,该材料也具有增韧优化的特性,将琴弦振动频率较好的展现出来,符合琴体结构的力学要求。PolyTerra™ PLA 所制成的琴身外观呈现哑光质感,巧妙地将打印层纹隐藏在哑光质感下,与小提琴本身低调典雅的风格相吻合,无疑是琴体制造的上佳之选。
抛开琴身需求来看,这种材料本身亦可圈可点。对于曹子杰来说,PolyTerra™ PLA 所展现的出色打印适应性,易于打印的特质使得材料挤出均匀,适用于高速打印。琴体打印完成后,支撑结构可轻松移除,既缩短了打印后处理时间,也提高了打印效率。作为一款高性价比的材料,PolyTerra™ PLA 具有生物降解性,不易污染环境。
不仅如此,基于Polymaker “种植一棵树”计划,每一卷 PolyTerra™ PLA 的售出,即意味着与 Polymaker 合作的公益植树协会在购买地国家或附近种下一棵树苗,为我们的身边增添一抹绿意。传统小提琴取自树木,PolyTerra™ PLA 源于绿植,归于树木自然,此番视之,也不失为一种默契,颇有几分异曲同工之处。
PolyLite™ PLA Pro - 小提琴指板
小提琴指板是演奏者运指飞舞的部分,传统木质小提琴指板常用坚硬细密的乌木制成,防止弯曲变形。指板的另一重要功能在于增加琴颈的强度,使琴颈可牢固地抵抗住琴弦的张力。
因而,在3D打印材料选择中,高刚性十分重要。从琴身结构来看,指板是全琴体最纤细的部分,在调弦和使用中受力较大,为避免指板折断,打印材质需具有一定韧性。曹子杰选用PolyLite™ PLA Pro 打印指板,本款材料是Polymaker首款集合了高刚性和高韧性特点的高性能PLA,配方升级使材料韧性大幅提升。根据样条测试结果,PolyLite™ PLA Pro 的弯曲模量和简支梁冲击强度均大幅度高于市面上的增韧PLA。刚韧兼具,颇为符合指板结构要求。
PolyMax™ PLA - 小提琴琴码&拉弦板
琴码的作用是将琴弦的振动传递到琴体,使其产生谐振,发出声音,它的微小变动都可能会引发声音的明显变化,是一个置于琴弦和琴身中间富有弹性的联结器。
通常意义下,理想的琴码一定要偏硬且有韧性。相较于其他琴身结构,琴码厚度偏薄,受力易断。基于力学考虑,曹子杰选取PolyMax™ PLA进行打印,本款材料极为便于打印,在抗冲击力度测试,抗弯曲力度测试,抗拉伸力度测试中具有良好的表现,材料韧性优异,甚至超过ABS韧性,适宜打印琴码,避免折断。
传统小提琴拉弦板常由枣木、乌木、红木等硬木材加工制作而成,具备栓弦功能。在3D打印制作中,材料受琴弦力极大,约为40公斤左右,因而同样需选取韧性优异的 PolyMax™ PLA 制成。
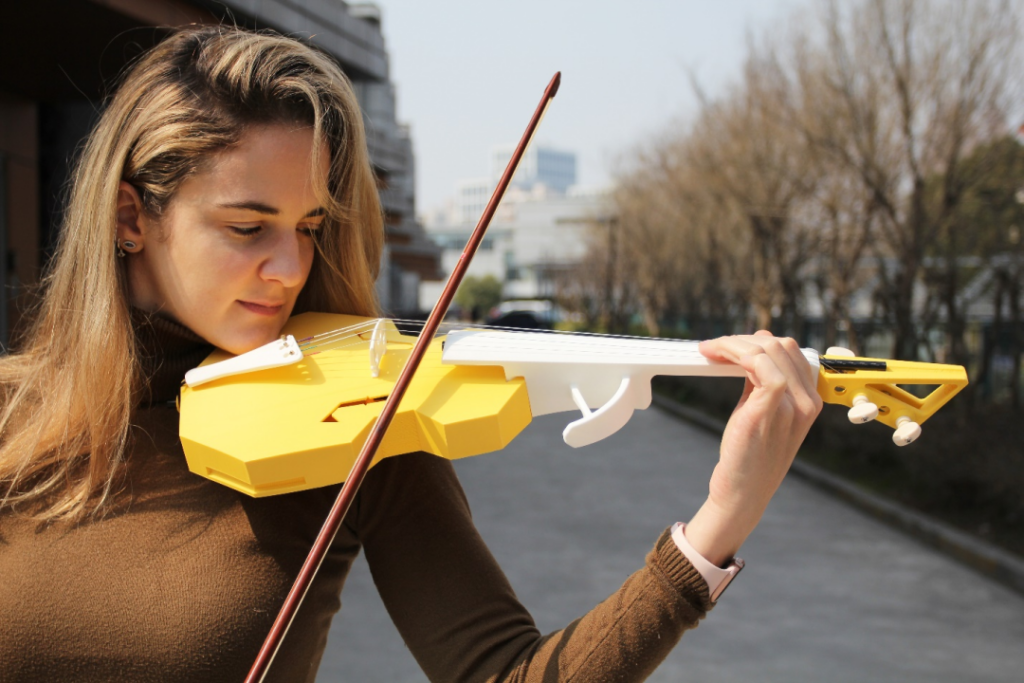
琴音中的未来
琴声悠扬,如幻如梦。
3D打印小提琴的出现,为多元化的乐器设计制作提供了可能。
作为传统木质小提琴的创新性选择,既可服务于专业小提琴演奏者演奏创新,也可用作儿童小提琴玩具陪伴孩童成长,在探索中一步步发现音乐的奥妙,而这新一代的成长,也将Polymaker所期待的实现多元化3D创意梦想进一步地落地为现实。乐器是富有生命力的,正如它的制作材料一样,3D小提琴将增材制造工艺创造的高分子材料与传统小提琴弦相结合,将会产生一种新的音质,为乐器演奏者探索更多的可能性。这种进化并不会停止,独特的设计理念,个性化的定制需求,将与3D打印的高效便捷结合,将这一先端工艺带向更远的未来。
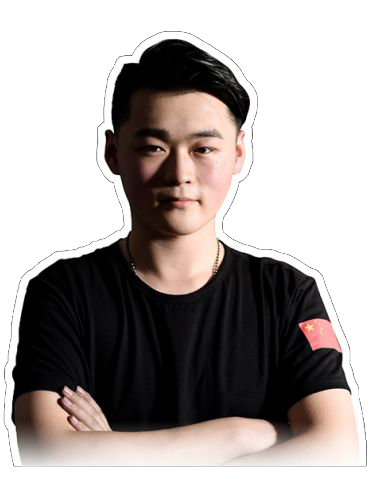
曹子杰
毕业于上海外国语大学贤达学院,本着对机械设计的热爱,2015年开始玩3D打印机至今,从事格斗机器人的设计与制造,运用3D打印验证设计可行性,致力于将3D打印带入生活中的实际应用。
2021年10月12日,同济大学翼驰车队2021赛季新车发布会在嘉定校区济人楼101报告厅顺利举办。
Polymaker作为赞助商之一,出席了发布会。中国顶尖职业车手、亚洲保时捷卡雷拉杯专业组车手崔岳作为特聘教练驾驶了TR21。
图1 | Polymaker 出席同济大学翼驰车队2021赛季新车发布会
图2 | TR21发布会组图
强大的核心动力
强大的凯旋675三缸发动机是TR21的动力核心。赛车搭载干式润滑系统、双路冷却系统和更稳定的供油系统,纯钛排气管消音器和钛合金空心半轴有助于实现更好的轻量化目标,再配合新开发的可变进气系统,可以进一步扩大这套动力总成的优势。
全新的车身结构
TR21采用全单体壳的车身结构代替以往的单体壳-副车架结构。车身的碳纤维铺层、铝蜂窝夹芯以及首次加入的PMI泡沫材料,使车身具有更高的强度和扭转刚度,并在轻量化方面做出巨大贡献且保证理想的重量分布。车身关键部位:单体壳预埋件和空气动力学套件翼肋使用了Polymaker的PolyMide™ CoPA作为3D打印结构件的材料,以提供良好的结构刚度。
图3 | 使用 PolyMide™ CoPA 打印的前翼翼肋
PolyMide™系列产品是基于尼龙材料开发的线材。采用了Polymaker专利的Warp-Free™防翘曲技术,因此PolyMide™ 系列产品不仅有尼龙材料本具的工程应用性能,还很易于打印。PolyMide™ CoPA材料的研发制造基于尼龙6和尼龙6.6共聚物。这款线材具有优异的机械强度与韧性,耐高温能力高达180˚C除了易于打印外,尺寸稳定性佳。PolyMide™ CoPA适用于在苛刻环境中使用的零件,例如齿轮,发动机支架,管道连接器或高速气流管。
图4 | PolyMide™ CoPA主要特性和材料性能
创新的空套设计
车身与空套升级是TR21的最大亮点之一。空气动力学一直是我们的至高追求并主导赛车设计,在系统化设计流程和多工况仿真指导下,全新的空气动力学套件能够在20m/s速度下达到1075N的下压力,整车外流场及气动敏感性进一步改善,显著提升赛车的弯道速度。其中,空气动力学套件导流片是通过3D技术,使用 Polymaker PolyMax™ PC 材料,制作完成的。除了材料本身的性能能够帮助改善空气动力学的性能外,相比常用的碳纤维制件,在有限牺牲结构重量的前提下,3D打印件的使用,大幅缩减了导流片制作的成本和工时。
图5 | Polymaker PolyMax™ PC 打印的尾翼导流片
PolyMax™系列产品均是采用了Polymaker专利纳米增强技术生产的高级3D打印线材,该系列产品都有优异的机械性能和打印质量。PolyMax™ PC是一款高性能聚碳酸酯线材,同时具备出色的强度、韧性、耐热性和打印质量,是工程应用的理想之选。它适用于对抗冲击性和高振动性有更高要求的应用,例如夹具和固定装置,家具,小型电动机支架,无人机,3D打印机零件等。
图6 | PolyMax™ PC 主要特性和材料性能
此外,Polymaker的PolySmooth™被选作了打印前翼襟翼变截面翼片和悬架吊耳覆盖件的线材,再通过酒精抛光的后处理技术,从而优化了整车流场。
图7 | 使用 Polymaker Polysmooth™ 打印的前翼襟翼翼片
PolySmooth™是一款独特的并且便于打印的线材,它专为后处理过程 “解放双手” 而设计。 打印完成后,可以使用Polysher™获得光洁的表面。PolySmooth™提供了可以轻松对模型进行后处理以获得光滑表面的可能性,专为难以打磨和后期处理的模型而研发,例如小雕像和角色扮演道具等。PolySmooth™还是产品设计和原型制作的理想选择,可呈现出与注塑成型相类似的光洁表面。
图8 | Polysmooth ™ 主要特性和材料性能
崭新的底盘系统
经过对轮胎特性的详细分析,我们更换使用了Hoosier 16寸高性能赛车热熔胎。基于这一轮胎为TR21匹配设计了全新的底盘系统,并搭配新增的线控横稳系统以提升车辆的动态表现。
升级的电控系统
TR21赛车继续提升了电控系统的开发,使用专业的MoTeC ECU实现电子节气门、气动换挡和可变进气歧管的精确控制,并支持无线数据采集。此外,在集成了无线电通信、线控离合、线控横稳、弹射起步控制、牵引力控制以及多种策略的调整功能的全新方向盘控制器上,让车手可以发挥出无限潜能。
图9 | TR21发布会组图
在本次发布会上,翼驰车队首次公布了无人车计划,相信在下一代赛车上,翼驰赛车可以搭载无人技术继续征战大学生方程式大赛。
Polymaker一直在积极参与推广3D打印技术在汽车及赛车行业的应用,该技术一定程度上具有降低成本、缩短周期、个性化定制、轻量化等优势。Polymaker全线材料的多样性也为3D打印赛车零部件提供了更多的选择性与可行性,其中工业级线材的应用更为普遍。Polymaker工业级产品包括基于尼龙添加碳纤维和玻璃纤维的增强材料,可以提高材料的热学性能和刚度,且具有出色的层间结合力。此外,含有PC的高阻燃材料和高分子合金材料,均具有良好的耐热性和韧性。
希望在不久的将来,3D打印技术能被更广泛地应用到汽车及赛车的制造生产中。
位于成都龙泉驿区驿马河公园的高分子3D打印桥“流云桥”亮相成都。桥梁的材料细腻轻盈,整体优美灵动,桥梁设计的灵感来源于驿马河自由奔腾的形态,以及舞动的丝绸。
“流云桥”由上海建工承建,Polymaker和上海酷鹰科技有限公司共同打造完成,在第三次的合作中,新技术和新材料在景观设计中又完成了一次大胆的创新,桥的尺寸更大、造型更优美、工艺更完善。桥身全长66.58米,宽7.25米,高2.7米其中3D打印部分桥长22.5米、宽2.6米、最高处2.7米。
“流云桥”的打印过程
桥梁打印采用了酷鹰五轴增减材一体机(BGAM),进行全天候7x24小时不间断3D打印。在系统中输入指令后,机器就可以24小时不间断打印,而且无需人工值守。为了确保打印质量,打印材料仍旧使用了Polymaker的抗老化与耐候性极佳的高分子颗粒料PolyCore™ ASA-3012。打印全程进行温度数据的记录以及参照经验的参数比对,确保打印构件较小的形变以及最佳的打印质量,从而实现闭环打印,这也是成都3D打印桥与酷鹰之前完成的两座桥相比,引入的一大新技术。整个3D打印桥耗费了数吨材料,桥梁采用了分段打印、现场拼装的施工方式,三维激光点云扫射检测技术也被应用于过程当中,因此仅用了35天便完成了全部桥体的3D打印工作。
“流云桥”的使用材料
PolyCore™ ASA-3012因其综合力学性能优异,适合于户外应用,被再次选为3D打印桥的使用材料。PolyCore™ ASA-3012专为超大尺寸3D打印定制的配方,增强了打印件在制造和使用过程中的尺寸稳定性及层间结合力。在打印工艺上,通过近百次打印试验和不断优化,采用预热及后保温装置,提高打印作业空间的温度,保证了3D打印材料层层粘结力。目前大多数增材制造技术采用熔融沉积成型工艺时都会产生残余应力和翘曲问题,因此我们在成都3D打印桥的整体制作中采用了多因素分析法,即通过控制环境温度、材料三段熔融温度、玻璃化温度、单层打印时间等打印工艺参数来解决打印构件由于迅速降温导致的翘曲及形变过大的问题。再通过酷鹰五轴增减材一体机(BGAM)的高精五轴CNC加工系统,将预留给打印变形量的余量去除,确保了分段打印构件的精度,完美展现了成都3D打印桥的整体设计效果。
实用性与美观度两者兼得的“流云桥”
为了提高通行的舒适度和桥梁的稳定性,3D打印“流云桥”的下方还增设了钢梁作为叠合支撑受力。两端的部分则采用轻质航空材料,通过数字化数控雕刻成型,表面进行特种涂层处理,以满足使用要求。这一超大型3D打印景观桥,是科技与艺术的完美结晶。
3D打印技术并不是第一次被用于桥梁的建造,下面就让我们一起回顾一下国内外一些著名的3D打印桥梁。
Polymaker 参与的3D打印桥回顾
上海桃浦中央公园3D打印景观桥
2019年,我国的第一座高分子3D打印景观桥诞生了,坐落于上海桃浦中央公园。由上海建工、Polymaker和酷鹰科技合力打造完成,全长15.25米、宽3.68米、高1.1米。
作为国内第一座运用3D打印技术完成的一次成型、最大跨度、多维曲面的高分子材料景观桥, 突破了传统桥梁设计的束缚,景观桥更加灵活、更为自由、更具多元空间变幻。设计团队运用三维数字技术成功实现了桥梁设计与施工建造技术的完美融合 。通过3D打印机,可以“一次成型“出S型、流线型的桥梁外形,营造出自由变幻、富于动态的桥体形态。
本次3D打印景观桥的打印工艺经过了近百次打印试验,不断地进行优化。通过上海建工与酷鹰科技联合研发的超大型龙门3D打印机,使3D打印精度更高、尺寸更大,可满足的空间结构更多样。
Polymaker的PolyCore™ASA-3012因具备高耐候性、高弹性模量、高屈服强度和高抗冲击强度等特点被选为本次3D打印景观桥的打印材料,并且,该款打印材料还能承受长期的日晒雨淋,这也是3D打印建筑材料的必备要求。
泉州3D打印景观桥
我国第二座采用高分子材料3D打印建造完成的桥梁于2019年6月下旬在福建泉州百崎湖生态连绵带完成安装。这是Polymaker、上海建工和酷鹰科技的第二次合作,桥长17.5米,高3.2米,宽3.2米,重量12吨,桥身整体依旧全部由高分子材料PolyCore™ ASA-3012配合3D打印技术制造完成。整个的制造周期为五周,比起传统混凝土灌浆制造法缩短了将近一半以上的时间。
3D打印的泉州桥,比传统的混凝土灌浆制造法省时,在强度上也一点不比钢筋混凝土逊色。每平方米可以承受2千牛顿的压强,也就是说就算桥上就算占满人也不用担心桥身的坚固程度。
该桥采用了分段式的设计,因此分段进行3D打印,之后通过独特的链接机构将每一段连接起来,从而达到桥梁的力学要求。
使用Polymaker的高分子颗粒材料PolyCore™ ASA-3012,配合上海建工与酷鹰科技共同自主研发的超大尺寸的五轴增减材一体机(BGAM),可以直接进行桥梁的分段3D打印。之后通过拼装、拼装缝隙处理、涂装和铺设步道,这座3D打印桥梁就完成了。
3D打印桥梁的未来
3D打印景观桥诞生的全过程,涵盖了对模型、建造的构想和数据设计,同时有别于传统的外观模式,正所谓“以科技之力链接艺术灵感”,通过3D打印技术的在桥梁建造中的应用,极大地拓展了景观设计的技术创新与探索实践。3D打印技术正在成熟,并正在成为更快、更可持续和更便宜地建造人行桥或大尺寸产品的一个重要选择。
目前各类大尺寸打印的解决方案已完善成熟,Polymaker已在积极研发生产满足不同大尺寸打印需求的材料,相信在不久的将来,3D打印技术能被应用到更多广泛的领域。
关于上海建工:
上海建工集团股份有限公司是中国建设行业的龙头企业,位列世界500强企业。六十余年来,上海建工多次刷新中国乃至世界工程建设史上的纪录,在全国100多座城市以及全球30多个国家和地区,奉献了众多工程精品。近年来,上海建工全力推进全国化发展,加强全产业链协同联动,在城市更新、水利水务、环境治理、数字化工业化建造、建筑服务业等新业务领域不断形成新的制高点,现正在加快建设成为广受赞誉的建筑全生命周期服务商。
上海酷鹰科技有限公司是专业从事超大型3D打印解决方案研发的高新技术企业,公司秉承“探索未来制造方式”的理念,基于“增减材一体化+新材料研发+智能控制”的创新模式,助力制造企业降低成本、提高效率。公司现有智能装备产品包括五轴增减材一体机(BGAM)、高速粒料打印机(SGAM)、机器人增材制造系统(BRAM),主要产品被广泛应用于建筑景观、航空航天、船舶制造、轨道交通、能源、汽车、医疗等众多行业领域。
Laboratory Technologies Inc. (LTI) 是一家领先的实验室辐射仪器制造商,自1983年以来,它一直为美国及海外实验室提供辐射仪器。LTI主要服务于全球包括核实验室在内的专业化小型实验室。
高成本的金属加工,限制了产品设计
在以往的生产过程中,LTI的产品采用的是机械加工模式,由于制作技术的原因,产品在进行设计时遇到一些限制,导致一些较为复杂的线条设计难以实现。
计数器外壳的制作相对简单,只需将一整块冷轧钢切割成设计的形状和尺寸即可。但探测器的制作却较为复杂。为了保护探测器中心晶体参数不被损毁,需要在外围设置一层保护装置。制作保护装置首先需要对实心钢管进行打孔,制作出完全贴合中心晶体尺寸与轮廓的中空结构。其次,为了保障密封性,在钢管的另一端还需要再焊接一块钢板。从机械加工工艺来说,制作这种结构复杂的零件难度较大,需要用到的工具较多,因此加工成本也较高。
3D打印技术扩宽了设计的自由度
为了控制生产成本,不再单纯依靠昂贵的机械加工工艺,在综合考虑之后,LTI决定尝试采用3D打印技术,代替高成本的机械制造。经过对比与测试不同3D打印品牌产品后,LTI最终选购了Raise3D Pro2 Plus大尺寸3D打印机。
Pro2 Plus的电动升降双喷头挤出系统,支持打印复杂的机械部件。大尺寸打印仓,可以实现大尺寸零件的一次性打印。同时,Pro2 Plus最高温度可达300℃的加热能力,可以兼容多种打印材料。在对不同材料以及品牌进行试验后,LTI最终发现Polymaker PolyMax™ PC材料是最合适用作其产品的3D打印材料。
图 | 旧版计数器外形设计(左)vs 新版外形设计(右)
由于3D打印几乎能够实现任何形状的打印,且无需更换额外的制作工具,这使得LTI的产品开发过程变得更加顺畅。无论是产品的外壳还是组装槽,抑或是通风口等带有功能性的特征,都可以使用CAD软件精确制作出数字模型,然后再使用3D打印机制作完成。
图 | 3D打印机制作的备件成品
在这个零件开发高速更新换代的年代,能实现定制化制作的Raise3D打印机不仅可以完成各种复杂设计的生产,同时还具有良好的用户体验。Raise3D Pro2 Plus虽然可以实现大尺寸打印,但机器整体的尺寸却并不庞大,无需占用过大的空间,可以置放在任何空间。正如LTI将其置放在生产线旁边,以方便工程师在打印过程中更好的观察生产过程,及时检查生产中或许会出现的问题。
图 | 办公室中正在运行的Raise3D打印机
选择合适打印材料的重要性
在测试了不同的3D打印材料后,LTI发现聚碳酸酯(PC)是制作其产品的最佳选择。但在测试不同品牌的PC材料时,LTI发现并不是所有的PC线材的表现性能都相同。在经过反复测试之后,LTI最终选择了Polymaker PolyMax™ PC作为自己产品的3D打印线材。
PolyMax™ PC是采用Polymaker的纳米增强技术生产的高性能3D打印工程用材料,具有出色的强度,韧性,耐热性和打印质量。
在现有的工业级3D打印线材中,PC因其优异的抗冲击性能和高刚度成为具有良好力学性能材料的首选。PC打印件可以吸收冲击,防止产品变形或开裂。除了PC本身的这些特性外,作为Raise3D开放式耗材项目(OFP)之一的Polymaker PolyMax™ PC能更好的适应Raise3D打印设备,易于挤出,表现性稳定,不易发生翘曲。LTI发现,3D打印的PC部件不仅和原来的冷轧钢具有同样的高抗冲击性,PC的密度还远远低于冷轧钢。
除此之外,对于伽马计数器和Wiper的擦拭测试计数器来说,UL防火等级很重要。Polymaker PolyMax™ PC还具有良好的阻燃性。
3D打印有助于提高产品质量,降低生产成本
经过几个月的开发,LTI通过3D打印技术实现了产品优化。通过重新设计结构,使用Polymaker PolyMax™ PC打印制作的新外部加强板与原本的冷轧钢一样坚固,但重量却轻了9.5公斤。原因是PC的密度只有1.2克/cm3,而冷轧钢的重量是7.8克/cm3。PC材料足足轻了6倍之多。在生产成本方面,使用3D打印后,LTI将成本减少到了原有的1/4,其中,材料成本更是缩小到原本的6%。
图 | 由Polymaker PolyMax™ PC打印的功能汽车千斤顶
致谢
感谢我们的3D打印机合作伙伴、国际一线品牌Raise3D为我们带来3D打印技术应用在实验室仪器市场的案例分享。Polymaker也在积极地和合作伙伴们探索3D打印技术在各行各业的使用和应用,争取能在各自的领域为整个3D打印行业创造更多实际的成果。
2021年的设计上海@新天地设计节,再次回归。呼应着新天地的20周年生日,「新·生·活」场景试图在诠释未来理想生活图景的命题下,回归日常的优美、生活的本质。
数字艺术家、匠铸三维创始人赵子晗的「数字环亭」,作为20件艺术装置之一,伫立在街区内老石库门建筑之前。柔润舒展的线条在底座成向上生长的姿态,看似无序不规则的外观,在随机中构造出一种诗意的巧合。
或隐或现的枝干,在平地上冒出一片遮蔽天日的小型乔木丛,让行者、路人不期然地“撞见”跳脱日常城市风貌的神奇景观。
数字环亭由Polymaker提供的Polylite™ PLA Pro打印而成。Polymaker作为世界一流的挤出式3D打印材料的创新者和供应者,曾多次参与3D打印技术在各类建筑、景观、设计领域的创新项目。继3D打印墙,3D打印桥后再次助力3D打印环亭。
本次Polymaker提供的Polylite™ PLA Pro不仅机械性能优秀,在原先高刚性的基础上增强了材料的韧性,大大提高了抗冲击强度,保证了游客在亭中可以随意嬉戏玩闹;材料打印效果优秀,使环亭本身细腻美观,色泽纯净;并且Polylite™ PLA Pro易于打印,兼容几乎所有FDM打印机,保障了环亭的顺利完成。
远距离的审视,纯白的外观与深灰的建筑外立面,形成亮眼的对比。来到此地,很难不被它的姿态所吸引。而亲近它、穿梭其中,又是另一番光景。在设计时,赵子晗带着一个问题:在城市当中,用什么样的方式可以把毫无关系的人联系起来?
可以确定的是,人一定是流动的,且是无序、无法精确预估的。如何在街区内探索?藉由这些探索,如何实现自我需求满足?而社交性又在其中占到怎样的比重?林林总总,都是难以量化估算的,便也就对空间的规划、景观的布置、装置的设计提出了极大的挑战。
而这种确定的不确定性,意味着一个可使用的公共装置,需要被赋予多重的功能。立体结构间相对通透地分隔而非完全隔离,人们得以在「数字环亭」中,驻足、穿行、观望、探视、憩息、倚靠、玩耍、交谈。
环形成为一个天然的内外分界,外环是开放的、来者可享受独立休憩,内环是半闭合的、钻入其中便可开启相对私密的交谈。从而,整体构造被赋予了现代都市人们之间关联的象征、无穷与循环的联系。
实体是抽象意象的容器,而艺术装置则是美的容器。这种实体,将审美的虚信息转录出来,并进行显示和表达,而形成一个可观看、可接触、可体悟的对象。「数字环亭」,是城市中的“艺术飞地”、是审美体验的停留地,也是都市里的互动场所、繁忙生活的“放飞站”。
实际上,对于这件作品,赵子晗更倾向于称之为“艺术景观产品”。形态的艺术性表现远超于功能性、能被穏定生产但因生产工艺相对复雑而难以实现大批量出货、年产量约在10件,这些特性让他的「数字环亭」目前仍处于一种相对小众的境地。
他所采用的的3D数字技术已经过一段较长时间的发展,其工艺、材料及成品质量等都得到了市场的验证。材料选用了Polymaker的Polylite™ PLA Pro。Polymaker作为世界一流的挤出式3D打印材料的创新者和供应者,曾多次参与3D打印技术在各类建筑、景观、设计领域的创新项目。继3D打印墙,3D打印桥后再次助力3D打印环亭。
本次Polymaker提供的Polylite™ PLA Pro不仅机械性能优秀,在原先高刚性的基础上增强了材料的韧性,大大提高了抗冲击强度,保证了游客在亭中可以随意嬉戏玩闹;材料打印效果好,亭子本身细腻美观,色泽纯净;易于打印,兼容几乎所有FDM打印机,保障了环亭的顺利完成。
而这件近似小型单体独立建筑的产品,可以算是国内首座FDM设备模块化方式制作的整体3D打印建筑。通过100台大型3D打印机联合作业,利用一个月时间将各模块分别打印,再拼装成5个大模块组、运至现场通过铝合金构件完成最终的组装固定。而在展览结束,也可拆卸回收。
这座建筑物的生产制造,是在已有模式和流程的基础上进行优化迭代。但并不意味着迭代过程是一以贯之的水到渠成,从草图到参数化模型,赵子晗和他的团队对单模块的物理受力、整体承重、结构曲率等因素都进行了细致深入的分析,对生产的打印效率、拼装工艺、成本控制等方面也完成了充分推演实验,甚至预生产了超过三平方米的墙面来进行研究。波折重重,才最终实现「数字环亭」的理想效果。
赵子晗在「数字环亭」中植入了自己的期许:创造一个未来,一个装置或建筑能被数字技术再建构的未来。“也许只是一个起点,当有一天它普通到无法成为未来、不被稀奇时,说明它已经普及甚广。”而到那时,赵子晗也将开启新一个起点的探索,而验证建筑与人类关系互相影响的实验、永不落幕。
2020年7月8日,在上海举办的TCT亚洲展首日,Polymaker与科思创联合发布最新业务产品 - 3D打印面料。
科思创和Polymaker多年来保持良好合作关系,共同开发高性能3D打印材料以及新的3D打印应用。此次,科思创和Polymaker联合业界顶级3D打印机制造商远铸智能INTAMSYS和Raise3D(上海复志)开发了新的打印工艺,以提高3D打印面料的批量生产能力和效率。远铸智能INTAMSYS FLEX 510打印机和Raise3D E2打印机非常适合打印3D打印面料所需的柔性材料。
随着3D打印技术已被广泛应用在工业、体育休闲、医疗等领域,3D打印也为纺织行业带来了新的动力!3D打印面料不仅为解决纺织行业引起的环境危机提供了解决方案,而且还为纺织业打开了全新大门,提供一种全新的设计和生产方式。
由科思创和Polymaker联合开发的3D打印面料是利用3D打印的方式来制造面料。除了减少浪费之外,它还具有更多实用价值,并且可以使用计算机算法来设计面料的肌理与花纹。3D打印面料的用途等同于传统面料或织物,可用于批量或定制化生产衣、帽、鞋、包、围巾、手套等服装及配饰等日常使用的产品。
不过相比于传统面料或织物,3D打印面料具有诸多优势,如:
一、兼具批量生产和定制化生产的柔性生产工艺
以生产3D打印鞋面为例,30分钟就可以打印出一个完整的鞋面。一台3D打印设备一天24小时的时间就可以生产出48个鞋面。并且由于3D打印技术的特性,理论上生产的每个鞋面的设计都可以是完全不同的。那么,30台设备,1个星期可以生产出超过1万个各不相同的鞋面。3D打印面料的定制化和批量化生产,第一次能够同时实现。
二、独特的肌理与花纹
依靠3D打印技术,可以做出传统生产方法难以做出的肌理与花纹,例如摩尔纹,形状变化和密度渐变等效果。对于这一独特优势,Polymaker已经开发出一套针对3D打印面料的设计与切片的程序。
三、数字化设计与自动化生产
3D打印面料的设计可以实现完全的数字化。使用Polymaker开发出的程序,通过算法即可实现形状变化,密度渐变,随机线条等设计样式。在设计自由度大为提升的同时,3D打印技术还可以将这些复杂的样式生产出来。3D打印面料的生产过程可以全部交与3D打印设备,实现24小时自动化生产,打印生产过程无需人为干预。
四、具有可编程的特性
为了满足不同的弹性,强度和硬度要求,除了材料本身的性能之外,3D打印面料的纹理设计和打印方法也具有关键的影响。Polymaker和科思创在此方面已经探索并开发了极具价值的方法和经验。比如在受力较大的区域加大打印线条密度从而增强面料强度,在受力较小的区域降低打印线条密度实现更好的透气性。设计师能够以最有效的方式设计出面料并实现轻量化。在需要受力强度的应用中(例如跑鞋),这种特性优势显而易见。在对强度要求不高的应用中,可以利用3D打印技术设计出具有特殊美感的样式。
在选择用于开发3D打印面料的材料时,Polymaker与科思创合作,首先从适用于3D打印技术的TPU材料中进行选择。TPU(热塑性聚氨酯)是一种热塑性聚氨酯弹性体,具有多样的硬度,耐磨性,耐油性,透明度和良好的弹性。它硬度范围宽,具有耐磨、耐油,透明,弹性好等特质,在日用品、体育用品、玩具、装饰材料等领域得到广泛应用。
科思创TPU材料种类丰富,性能各异。针对不同的弹性、强度和软硬需求,Polymaker选择出相应的TPU原材料,针对3D打印技术调制配方,开发出3D打印材料。本轮发布的面料样式里包括了90A和95A,两种硬度的材料。
五、一体化设计与生产,减少生产环节的废料
面对环保这个全球性重要议题,3D打印更加能够体现优势。3D打印一体化的设计可以减少生产环节的废料,大大降低生产过程中的浪费,乃至趋近于零浪费。另外,在3D打印的生产过程中,不使用水,不浪费水,更不会污染水,对比传统生产方式,环保方面优点突出。
Polymaker与科思创联手,并与硬件厂商远铸智能INTAMSYS以及Raise3D(上海复志)配合提升3D打印面料生产效率,大力推动3D打印在纺织业中的应用开拓,助力3D打印面料从艺术品到产业化的转变升级。
科思创亚太区业务拓展经理王伊芳(左)与Polymaker副总经理屈航(右),在2020 TCT亚洲展,Polymaker 展位3D打印面料展板前合影
远铸智能INTAMSYS CEO韩成超(中)与Polymaker副总经理屈航(右)和Polymaker战略发展部门高级经理黄宇立(左),在2020 TCT亚洲展,Polymaker展位3D打印面料展板前合影
Raise3D(上海复志)创始人兼CEO封华(左)与Polymaker副总经理屈航(右),在2020 TCT亚洲展,Polymaker展位3D打印面料展板前合影
关于Polymaker
Polymaker是一家专注于3D打印材料的高科技企业,致力于用领先的技术、高质量的产品和细致深入的服务,推动3D打印技术在各行业深入应用。产品被世界各地的客户广泛应用在汽车、航空航天、工业制造、医疗、消费等多个领域中。
关于科思创
科思创是全球最大的聚合物公司之一,业务范围主要包括高科技聚合物材料的制造以及为与人们生活息息相关的众多应用领域提供创新的解决方案。科思创的主要服务领域是汽车、建筑、木材加工和家具以及电气和电子行业。其他服务领域包括体育和娱乐、化妆品、医疗和化学工业等。科思创在全球拥有 30 个生产基地。
早在 2013 年 11 月,Polymaker 就拥有了第一条专用生产线,并开发出了柔性 3D 打印线材产品。由于当时市面上的柔性线材与不同 3D 打印机的兼容性很差,Polymaker 决定对这款材料的可塑性进行微调,打造出既易于打印,又能保证打印件柔软灵活的线材产品。PolyFlex™ TPU95 是 Polymaker 旗下的第三款产品。
PolyFlex™ TPU95 是一种基于热塑性聚氨酯(TPU)的线材,主要用于桌面级3D打印机。它的邵氏硬度为 95A,拉伸长度能够达到原来的 3 倍以上。
最近,各种应用领域对柔性3D打印材料的需求迅速增加。为满足市场需求,Polymaker 决定为PolyFlex™ TPU95系列增加新颜色——蓝色和红色。
这两种颜色的产品现已在 www.polymaker.com.cn 和亚马逊上有售,直径分别为 1.75 毫米和 2.85 毫米。
你大概曾听说过比利时摩托车制造商——Sarolea,这家摩托车公司虽然在上世纪六十年代停产,但最近已正式复出。复出后公司的核心与1850年初创时一样——保持对摩托车的热情,并不断将新技术如电能驱动融合进摩托车制造中。
Sarolea凭借他们曾为赛车摩托车开发的独家技术,从零开始研发电动摩托车。当其赛车大受欢迎后,品牌决定以其第一款赛车摩托车Manx 7为基础,设计一款适用于公路的摩托车。整个生产过程中,每个阶段都使用到3D打印技术,也因此与Polymaker建立起了紧密的技术合作关系。
3D打印技术能够全方位为汽车行业提供巨大势能。Sarolea已将3D打印技术整合到他们生产周期的各个阶段中去,利用不同的材料及其特性进行设计、生产,并最终用于制造摩托车零件。
阶段1:设计与研发
应用:原型制作,概念设计,设计迭代
优势:成本低,交货时间短,轻量化,设计自由度高,外观与功能可快速验证。
描述: PolyMax™ PLA和PolyMax™ PETG都适用于原型制作。以Manx 7电动超级摩托车为例,综合考虑打印性能、可靠性和韧性,可使用PolyMax™ PLA进行整个车身的原型制作。而N60系列车型中,则使用PolyMax™ PETG进行车身原型制作,因为与PolyMax™ PLA相比,PolyMax™ PETG更易打磨和抛光,比PLA的耐热温度高20°C。这使得Sarolea的外观打印更美观且测试车身部件更专业。
阶段2:生产
应用:模具制作,生产夹具,制造夹具
优势:快速制造定制零件的特定工具,通过内部打印可有效减少生产周期,降低成本。打印负模具时可以直接利用材料进行碳纤维叠层。
描述:这部分Sarolea选择PolyMide™ CoPA进行模具打印,利用其碳纤维成分制造最终零件。由于Manx 7和N60系列都采用碳纤维单壳车架,需要许多复杂的模具来促成碳纤维叠层。PolyMide™ CoPA能够承受真空固化过程中的高温和压力,是这部分组件材料的不二选择。组装摩托车时,还可以使用PolyMax™ PETG来制作生产工具、夹具和固定装置。
阶段3:售后市场
应用:生产就绪零件,定制和备件
优势:使用先进材料打印成品零件,为现有零件提供全定制服务,保持备件的数据库完整。
描述:Sarolea在最终生产中使用了许多Polymaker提供的先进材料来进行零件的定制与3D打印,包括在高速气流中广泛使用的PolyMide™ PA6-CF,以及作为定制电池内的电池支架的Polymaker™ PC-PBT,还有阻燃材料PolyMax™ PC-FR可用于打印高压电路和必要的电线的夹具和固定装置。
从与Sarolea合作中可以发现,Polymaker的材料不仅适用于原型制作,而且在摩托车零件的制造和终端生产中也能独树一帜。两家公司之间的技术合作伙伴关系使得Sarolea能够持续推动摩托车电动化进程。
比利时电动超级摩托车制造商 Sarolea 与 Polymaker 建立了技术合作关系。
Sarolea 是一家复兴摩托车品牌,目前专注于制造电动超级摩托车。在从0到1制造摩托车的过程中,每步生产阶段都使用了 3D 打印技术。Sarolea不仅在生产过程中使用了多种Polymaker材料,并向Polymaker应用工程师寻求专业知识,逐步与Polymaker建立起更密切的关系。
“我们在设计过程中使用Polymaker线材来打印部件和组件。得益于Polymaker线材的高品质和他们工程师的专业知识,我们赛车和量产自行车上的某些部件都可被精确打印。这些部件非常复杂,传统生产工艺难以制造。” Sarolea的 Rob Mitchell 如此说到。
Polymaker 将在 2019 年 Formnext 展会期间的 Polymaker 展位(展位号:1211-E111)展出 N60 电动超级摩托车,它代表着 Sarolea 正在使用的生产阶段的三个部件。此外,来自Sarolea的 Rob Mitchell 将于展会期间在Polymaker展台举办讲座,着重为大家解释 Sarolea 与 3D 打印的关系以及从原型设计到生产的过程。
HP Star 是一个高压研究实验室,可以模拟太阳系行星内核的主体环境。通过在微观尺度上创造巨大的压力和温度,HP Star 的科学家们可以仔细研究宇宙中最丰富的元素在最极端环境中的影响。
这项研究的目的是了解基本元素在承受巨大的压力和温度时会发生什么变化,这将使我们对行星内核的实际情况有更深入的了解。木星、土星和太阳系的类木行星主要由氢和氦组成。这两种丰富的元素是HP Star 实验室进行高压实验的重点。
为了让这座位于上海的实验室实现如此高压,HP Star 的科学家们在一个夹在两颗金刚石之间的小小空间内内捕获氢气。一小块金属箔通过激光钻孔形成一个 20-200 微米的空间。金属箔作为垫片被精确地压在两颗金刚石之间,为实验提供了一个样品空间。
一旦样品气体聚集在金刚石间,科学家们就可以通过拧紧夹住金刚石的钢圈来缓慢增压。由于金刚石具有惊人的硬度和碳结构,这样就能在腔体内将被困气体压成巨大的压力。使用金刚石制造高压室的另一个好处是利用了其光学清晰度。这样,科学家们就可以通过金刚石向高压室发射强力红外激光,重现行星核心的极端温度和压力。
Dalladay Simpson 博士正在使用 3D 打印技术制作细胞支架,作为进行实验的平台。细胞支架包含钢制细胞,可提供对金刚石施加的夹持力。这些电池座对材料的要求非常苛刻,因为舱内的局部压力和温度可达 400 GPa 和 3800°C 以上。虽然这种巨大的压力和温度在金刚石腔体内非常局部,而且只在短时间内出现,但电池座的材料仍然需要非常坚硬和耐热,才能进行可靠的实验。
"地心的压力为 320 千兆帕(GPa),在我们的实验中,可以达到 400 千兆帕的压力,当我们将压力提高到这个点之后,我们的金刚石往往会在压力下爆炸,当它们爆炸时,场面相当壮观"。
Polymaker 的最新材料 PolyMide™ PA6-CF 已成为实验室的首选材料之一。Dalladay Simpson 博士表示:"碳填充尼龙的刚度和强度产生了一个非常坚固的细胞支架,我们的焦距范围工作在微米公差内,细胞在增加压力后仍能保持稳定"。
PolyMide™ PA6-CF 的热变形温度为 215°C,这证明它不仅适用于这些电池座,还适用于多种定制实验室设备。以前,对于定制实验室设备,预计内部机械车间需要 2-3 周的交货时间,而且经常需要进一步改装设备。而这些新材料(PolyMide™ PA6-CF 和 GF)可迅速加快这一过程,同时还能生产出更优质、更成型的实验室设备。
在温度范围的另一端,PolyMide™ PA6-GF 被用于制造低温箱,用于研究极低温下的元素。这些低温箱用于对金刚石尖端进行低温冷却,直到其冷到足以在其上凝结样品,根据试样元素的不同,可以凝结成固体或液体。
这样就可以对固体氯、硫化氢和其他高温超导体进行高压研究实验。这项研究有助于深入了解太阳系气态巨行星所经历的大气条件。"我们一直将液氮直接倒入 3D 打印的低温箱中,以快速冷却细胞,我们经历过一些非纤维增强材料在热冲击下开裂的情况,但PA6-GF 在这些条件下有着非常好的表现"。Dalladay Simpson 博士说到。
对于Dalladay Simpson 博士来说,他的最终目标是在实验室中生产出金属氢,这被誉为高压物理学的圣杯。金属氢是氢的一种物相,在这种物相中,氢的行为类似于电导体,尤金·维格纳和希拉德·贝尔·亨廷顿于 1935 年首次提出了这一理论。研究人员认为,金属氢大量存在于木星和土星炙热且受到重力压缩的内部。通过使用内部开发的 RAMAN 散射技术,Dalladay Simpson 博士可以探测样品室内部的振动,他希望这将揭示金属氢。
世界上第一座 3D 打印高分子桥梁现已落地上海。它不仅是上海市区公园内的一大地标,也是大规模 3D 打印应用的里程碑。这座桥重 5.8 吨,整体采用Polymaker开发的ASA材料,为增加材料的硬度和韧性,Polymaker更在材料中添加了 12.5% 的玻璃纤维且贯穿整个桥体。该桥梁仅需30来天即可打印完成,也是上海建工集团新型大规模打印机完成的首个项目。
关于这一3D打印机规模,其构建体积为 144 立方米,Y轴长度为25米。这使得建工集团能够以前所未有的规模涉足挤压式3D打印领域。我们已经可以看到,3D 打印技术几乎融入到了所有行业,是时候让建筑行业参与这一时代趋势了。
这座人行天桥可承重 13 公吨,相当于每平方米可容纳 4 人,预计能够在公园内使用 30 年。人行天桥使用的打印材料是由 Polymaker 工业材料系列开发而成的玻璃纤维增强的丙烯腈-苯乙烯-丙烯酸酯(及ASA)。ASA 因其耐候性和良好的机械性能而被成为首选材料。玻璃纤维(占比 12.5%)的加入增加了材料的硬度和韧性,同时还降低了热膨胀系数。
热膨胀系数的降低意味着材料在加热和打印时,膨胀和收缩得到了较好的控制,从而形成平整的层,消除了材料内部的应力。3D 打印机上的挤出机由上海酷鹰科技有限公司开发,该公司采用了捣固系统,以确保所有层面都保持平整。挤出机是一个用于颗粒挤出的螺杆驱动系统,有三个加热区,在热端有一个 5 毫米的喷嘴,每小时可泵送 8 公斤的材料,层厚为 10 毫米。
在制造捣固系统的测试阶段,如何在这种大规模打印区域内保温成了一大难题,因为喷嘴每打印完成一层就需要 2 个多小时才能让材料完全冷却并结晶,否则会降低层间强度并产生强烈的翘曲。因此,上海酷鹰科技有限公司在挤出系统中增加了四个工业热风枪,在铺设新一层前将上一层加热,通过将上一层加热到玻璃转化温度,来增强层间粘合力,从而提高打印件强度,并消除翘曲。
随着大规模打印技术的不断发展,Polymaker也在认真思考这项技术能在更大范围内发挥什么作用,如果能将回收塑料重新用于 3D 打印桥梁,而不只是循环使用一次性塑料制品,情况会怎样?用于制造一次性饮料瓶的 PETG 是迄今为止全球回收利用率最高的塑料,它与 ASA 有许多相同的特性。而3D打印大型结构就可将所有再利用塑料集中在陆地上的某一个地方,这样既便于管理,又有明确的使用寿命,还能造福成千上万的人。虽然人们总是小心翼翼地把 PETG 瓶子扔进回收箱,让这个塑料瓶变成另一个一次性使用的瓶子,但又如何保证下一个人也会回收塑料呢?事实上,人们回收的这些材料,最终还是会流向错误的地方,污染我们的海滩和海洋。试想一下,在目前的回收箱和普通垃圾箱旁边,还有第三个垃圾箱,叫做 "再利用",在这个垃圾箱里,所有的材料都会被再利用,变成长期的3D打印项目,将塑料锁在陆地上,造福更多的人。
前不久,Polymaker为上海建工集团打造了一座3D打印人行天桥。这座天桥耗时30天完成,长度为15米,重量为5800公斤。上海建工集团以大规模建筑闻名,上海中心大厦就是他们的杰出作品。此次用的3D打印机则由沈阳机床集团制造,挤出系统由上海酷鹰科技有限公司制造,总投资约280万美元。Polymaker开发了一款用于打印的工业级ASA材料,使其具有良好的耐候性、耐化学性、热稳定性和韧性。由于这座桥需要承载13吨(及每平米4人)的重量,因此强度是一个非常关键的因素。所以在正式动工前,Polymaker用几种不同的化合物材料先行打印了一座5米长的桥梁,最终综合整体强度和可打印性等特点,选择了AS100GF。
这款材料含有12.5%的玻璃纤维,增加强度的同时,减少了困扰大型3D打印成品的翘曲问题。大物件打印并不是制造一个大型打印机那样简单,因为3D打印过程中的很多问题都与保温及均匀加热相关,而这些问题在打印机越大时会变得更加棘手。原本24米长、4米宽、1.5米高的建筑空间需要提升高度,计划将其扩展到3米高。这样一来,就需要再加热144立方米的空间。我们选择用一架大型的可伸缩帐篷来实现,该帐篷可以随着龙门架的移动而移动。打印过程中,我们会将帐篷加热到38°C,并在打印好的部件顶部放置毯子以减缓冷却过程,使聚合物链能够在没有翘曲的情况下放松。当然,毯子还能保护打印物免受遭灰尘。
然而,加热只是整个打印过程中的问题之一。随着规模的增大,如何保证层间平整度及层间结合力也成为了一大困扰问题。为保障层间结合力,打印时每层的温度需要几乎相同才能有效结合。而实际操作中,由于每一层打印都需要几个小时,所以当挤出机绕到下一层时,前一层已经明显冷却。虽说毯子和玻璃纤维有助于减缓冷却速度,但特制的打印头在这时起到了很大的作用:挤出喷头四周设置了四个600°C的热风枪,挤出机工作时,这四只热风枪也会持续加热打印件,以确保打印件在挤出机工作区域始终保持一定温度、实现层间结合力最大化。
层间平整度问题则通过一种全新的方法解决——夯实。这一方法在其他3D打印机上并不常见。由于打印机的喷嘴是圆形的,这意味着它们挤出的材料也是圆形。当它们被挤压至一层时,其顶部是锥形的,这对于层间平整度来说并不理想。对于喷嘴尺寸为0.35mm的桌面3D打印机来说,锥度问题大部分时候并不会被察觉。但SGC 3D打印机使用的喷嘴尺寸为5mm,是桌面打印机喷嘴尺寸的14倍多。所以尽管本次打印件尺寸巨大、每小时挤出的材料重达8kg、且打印机的精度达到0.1mm,材料在挤出后立即夯实对于层间平整度和附着力依然有非常大的作用。尤其是首层打印时,为使其成功粘附到打印平台上,ASA粒料被粘贴到木板上,然后夹在钢床上。不得不说,有时候简单的低技术解决方案才是最好的解决方案。
我们相信,这座横跨湖泊两岸的人行天桥是展示大型高分子3D打印作品的绝佳方式,因为它既是日常生活中的实际应用,又是一种互动体验,可以任人们触摸、倚靠的真切的3D打印成品。这对于许多从未接触过3D打印且将其视为幻想和未来科技的人们而言,是一个现实奇迹。
意大利电动汽车公司XEV与Polymaker携手,在中国3D打印文化博物馆(上海)举办了一场联合新闻发布会,向世界宣告第一辆可大规模生产的3D打印电动汽车就此诞生,并在发布会现场向公众展示。
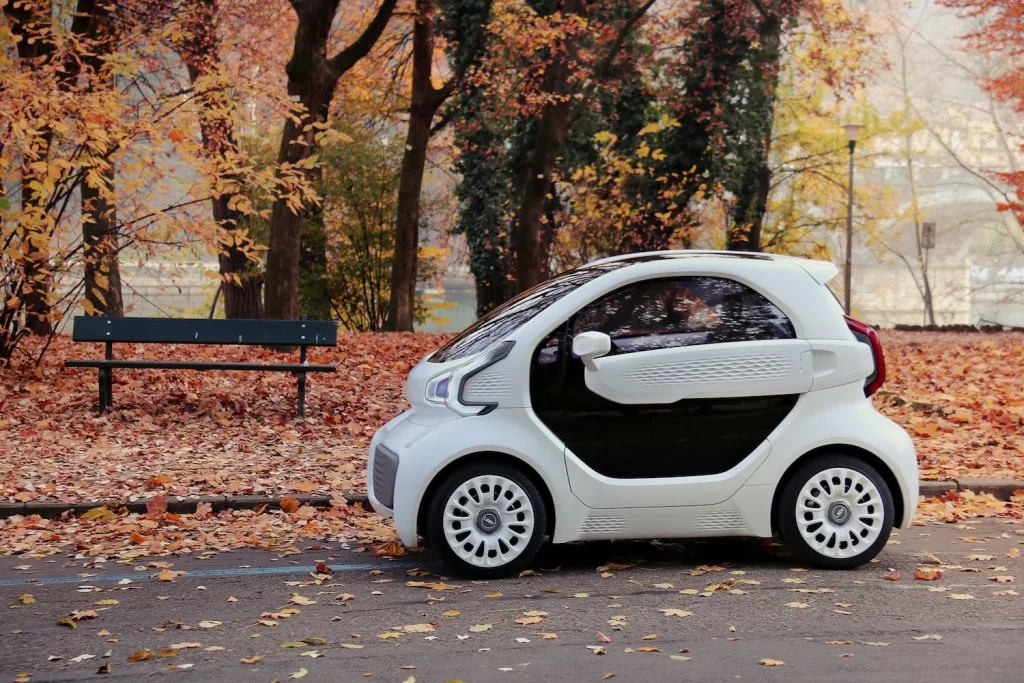
这款新车引起了媒体的广泛关注,但发布会不仅为展示车辆,更重要的是彰显了3D打印技术给汽车制造业带来的巨大变革。这款名为LSEV的汽车可能成为将3D打印技术引入主流生产的里程碑之作。
Polymaker的联合创始人兼首席执行官罗小帆博士表示:“XEV是第一个真正使用3D打印进行大规模生产的项目。我所说的真正是指还有很多其他公司在使用3D打印进行生产,但在规模、范围和强度上都不能与XEV相提并论。”
XEV首席执行官斯坦利谈及合作初衷:“在全球汽车市场的调研和调查后,我们决定设计一款小型电动汽车,实现C2M(顾客到制造商)制造。这也是工业4.0战略的主要目标。为实现这个目标,需要进行大规模定制生产,快速且具有成本效益的研发,并能生产出更轻的零部件,以提高燃油效率。然后,3D打印技术成为实现这一目标的唯一途径。”
当然,要将3D打印技术用于汽车批量生产中,还是会存在许多困难。Polymaker,作为XEV的战略合作伙伴,成功助其解决了这些难题——不仅提供了合适材料,还提供了符合汽车行业要求的后处理方案。
斯坦利称赞:“没有Polymaker,我们就无法实现这一切。与Polymaker的合作,我觉得可称之为知识和技术的结合。非常感谢Polymaker为我们所创造的一切,比起战略合作伙伴的称呼,我更愿意将这次合作称为兄弟齐心之举。”
Polymaker为XEV开发了几十款工程材料,以满足其实际应用的需求,并取得了三个方面的重要成就。
- 将传统汽车中2000多个塑料零部件减少到57个,完工的LSEV重量仅为450公斤,远低于类似大小的汽车1-1.2吨的重量。
- 除底盘、座椅和玻璃外,汽车的所有可见部件均通过Polymaker的材料3D打印而成。与传统的生产系统相比,这种生产方式减少投资成本70%以上。
- 传统生产方式里,一款车型的研发过程需要3至5年的时间,而XEV仅需3至12个月即可完成专属新设计。
Polymaker还提出了汽车表面处理和颜色解决方案,这些解决方案在定制生产和3D打印批量生产中提供了很大帮助。
在开始大规模生产前,XEV就已经收到了来自欧洲的7000个订单,其中5000个订单来自Poste Italiane,另外2000个订单来自BNP Paribas全资拥有的汽车租赁公司ARVAL。XEV计划在2019年第二季度投产。
XEV和Polymaker之间的战略合作伙伴关系引领了汽车制造业的变革发展。以此类推,与3D打印技术相关的变革很快可能会发生在制造业的各个方面。Polymaker证明了其高质量的3D打印材料不仅适用于最终使用零部件,还适用于批量生产的成品。
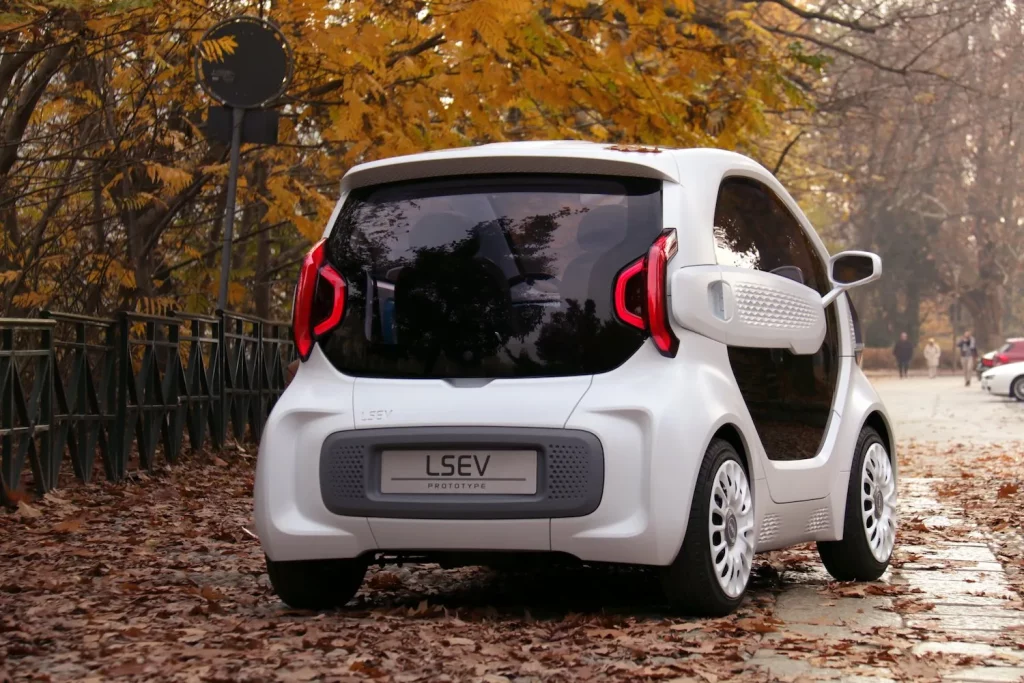
近几年间,大型的3D打印项目的数量与日俱增。还记得2015年创下吉尼斯世界纪录的世界最大的3D打印结构Vulcan Pavilion吗?它由1023个独立的3D打印单元组成,长8.08米,高2.88米。“纪录是用来打破的”,这句话正是在3D打印领域发生的事情。日前,北京展示的3D打印Rise Pavilion已经成为世界上最大的3D打印结构。
这一3D打印幕墙于2016年8月20日正式获得吉尼斯世界纪录,成为世界最大的3D打印结构。其设计绝对令人印象深刻——由5300多个打印单件构成,重达1.87吨,高度超过3.3米,占地面积超过1180平方英尺。展馆的5个拱门代表了5个不同的领域:健康、交通、社会、教育、艺术和设计。
制成幕墙的这5300多个打印单元在展出完成后,将被回收再利用,做成装饰品。这正是该项目的最终目标——让年轻一代思考可持续和生态保护,并鼓励这一思维“向多功能和环保商品转变”。目前,Rise Pavilion作为正在北京举行的青年创造者杯展览的一部分进行展出。该设计还考虑到了模块化,组装和重组都更加便捷。这意味着当展览于9月6日结束时,参与者都将可以带走一个打印单块,留作纪念或再制新的创意。
这些打印件都是无支撑打印,采用PolyMaker的PolyPlus可生物降解线材,这一线材拥有防堵头(Jam-Free™)技术,以确保顺利挤出并防止堵住喷头。为了完成这个项目,他们使用了70台桌面级3D打印机在45天内打印出所有零件。
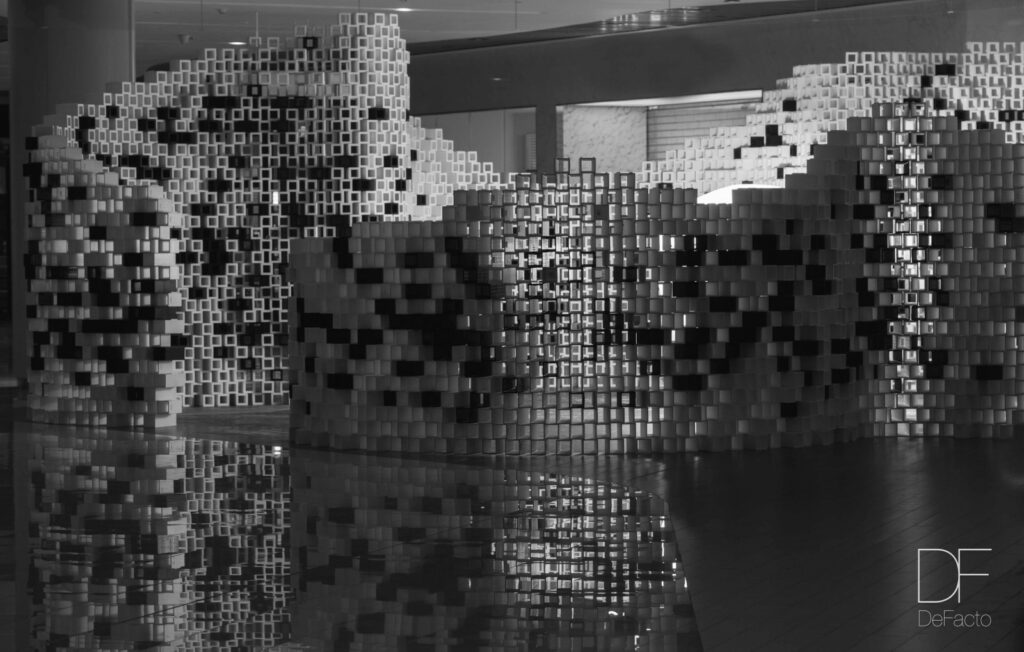